Sealing of street lamps
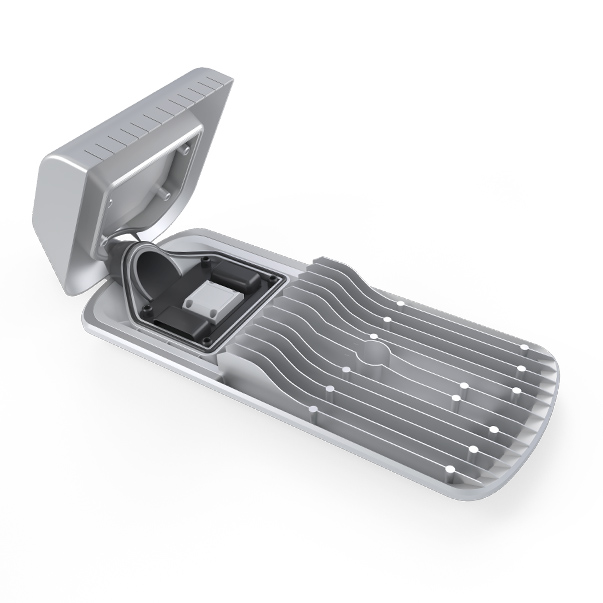
Street lights are sometimes exposed to extreme weather conditions. Regardless of whether they are fluorescent lamps, high-pressure sodium lamps or LED systems; the lamps, ballast and electrical components must be protected from rain, dust, sunlight and other weather conditions.
The street luminaire housings, which are usually made of die-cast aluminum or glass-fiber-reinforced plastic, are equipped with a seamless seal in the housing groove using polyurethane or silicone sealing foams.
Depending on requirements, the weatherproof protection of the light sources and electrics used demands the highest IP protection ratings for the entire construction of the housing, housing cover and seal: up to IP 68 with outdoor-rated FERMAPOR K31 polyurethane foam, or up to IP 69K or NEMA 4-6p with FERMASIL silicone foam.
Safely protect light sources and
lighting electronics in street lamps
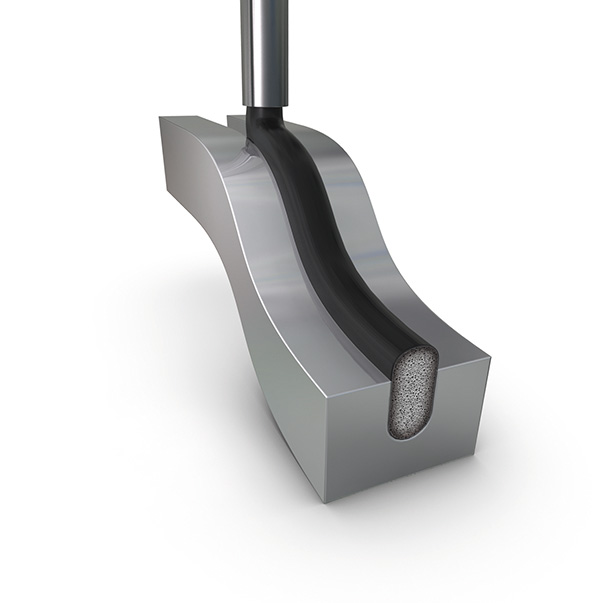
Our temperature-resistant silicone foam seals are particularly UV-resistant and offer permanent protection even under very low and high temperatures from -60 to +180 ° C. Thanks to the almost closed-cell foam structure, the silicone seal is very water-repellent.
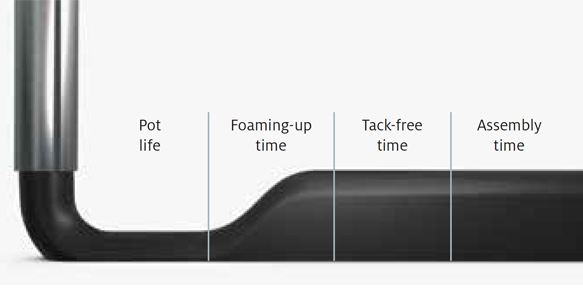
The different reaction phases of the sealing foam in the chronological sequence
Reference material
Street lighting |
Outdoor street lighting |
||
FERMASIL A-3150-1 | FERMAPOR K31-A-9212-3-VP | ||
FERMASIL B-3130-1 | FERMAPOR K31-B-4 | ||
Mixing ratio |
1 : 1 | 4.5 : 1 | |
Pot life time |
38 sec. | 41 sec. | |
Tack-free time |
13 min. | 5 min. | |
Viscosity of the A component |
98,000 mPas | 61,000 mPas | |
Density |
0.32 g/cm³ | 0.31 g/cm³ | |
Hardness (Shore 00) |
40 | 59 | |
Temperature resistance |
from -60 to + 180 °C | from -40 to + 80 °C | |
Pretreatment |
Plasma, Corona or Primer | Plasma, Corona or Primer |
In addition to the reference products, we develop material systems according to your individual requirements. Influencing factors include pot life until start of foaming, curing time, and the viscosity, hardness and adhesion properties.
Frequent opening and reclosing for maintenance purposes with remaining sealing effect
The very good resilience of the foam seal allows the street lamp to be opened and closed again for maintenance purposes without losing its tightness. After closing, the housing is tight and the sensitive lights are protected against splashing water and the effects of the weather.
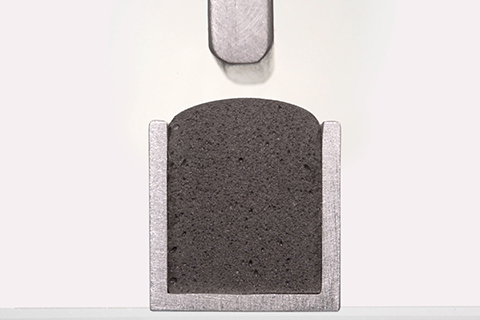
Street lamp when open, the seal is uncompressed
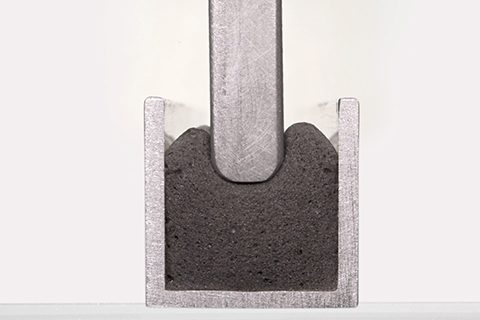
Street lamp when closed, the seal is compressed
DM 502 mixing and dosing system with 3-axis linear robot and a shuttle table for the parts holder
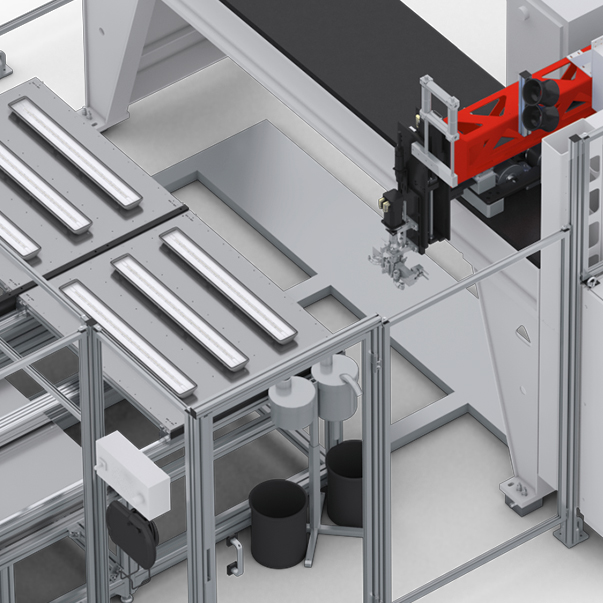
Flexible and fully automatic -
according to your requirements
As process experts, we support you with our application engineering expertise, from the design phase for your components through to fully automated material application using formed-in-place foam gasket (FIPFG) technology.
Our flexibly configurable DM 502 mixing and dosing system has a 3-axis linear robot and sliding table solution, and can be adapted to your production concept for the seal-foaming of luminaire housings or for LED potting.
To this end, we offer equipment options for semi-automatic or fully automatic production systems. If desired, CNC-controlled plasma application is also possible to achieve surface activation of the housing contour, resulting in better adhesion of the foam gasket to plastics such as PP or PE.
The reference configuration shown here for sealing linear luminaires consists of the DM 502 mixing and dosing system with LR-HD 3-axis linear robot and WT 1-LEVEL shuttle table for picking up parts. Two alternately operated pick-up plates facilitate continuous operation by allowing workpieces to be fixed and processed in a single plane.
The positioning of the luminaire housings on the pick-up plate is performed either by a machine operator, who can also check the parts for quality, or by a Pick & Place Robot. In the latter case, a camera or sensor system can optionally be installed to perform quality control on the parts.
The material components of the sealing foam used are mixed dynamically and homogeneously in the mixing head of the DM 502. The resulting fine-cell foam structure is crucial for low water absorption levels.
For material application using the FIPFG process, the MK 800 PRO precision mixing head is moved over the housing groove of the linear luminaire with high repeat accuracy by the CNC-controlled linear robot, and the sealing material is applied into the groove in accurately metered doses via the mixing head nozzle. The dosing loop completes the foam gasket with a seamless, almost invisible coupling point.
Highly efficient and precise material application by the DM 502 allows quick application processes in your production facility, and rapid processing of the parts through to final acceptance.
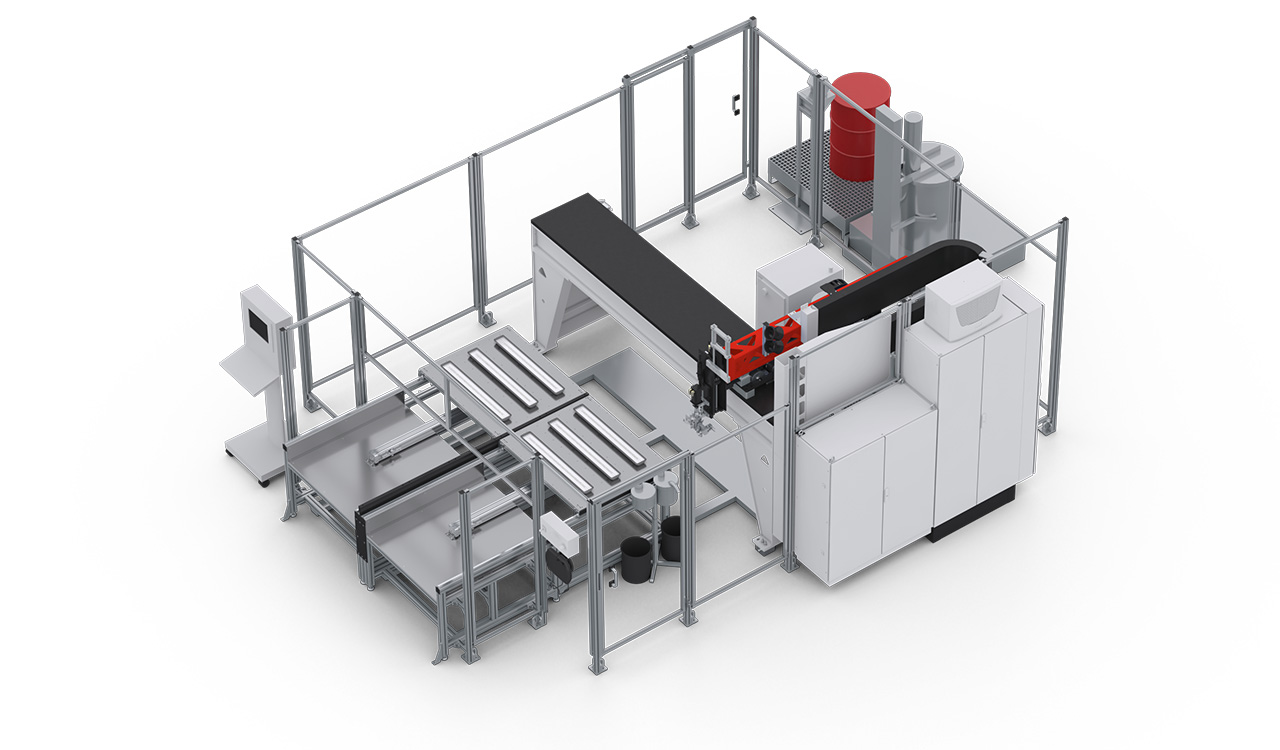
CONTROL 2
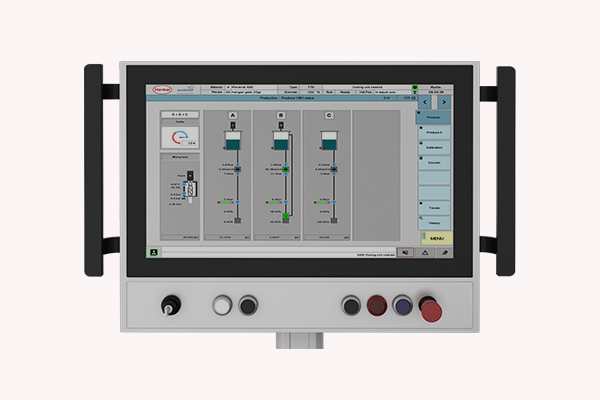
Optionally available: CONTROL touchscreen operating panel (21.5“) for operating the dosing system
More information to our operating panelsMP 2 Mobile panel
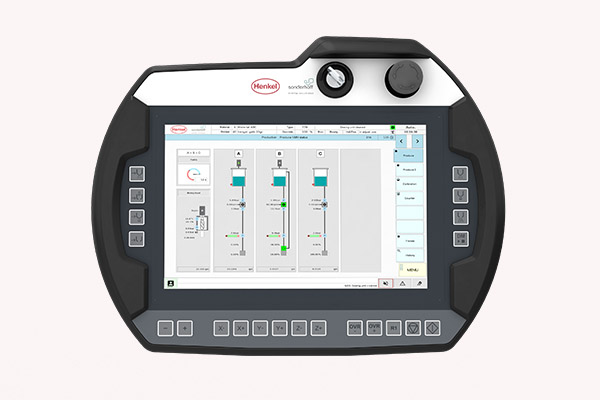
The multifunctional MP 2 mobile panel (10.1” WXGA TFT) enables convenient operation of the dosing system.
More information to our operating panelsWT 1-LEVEL shuttle / sliding table
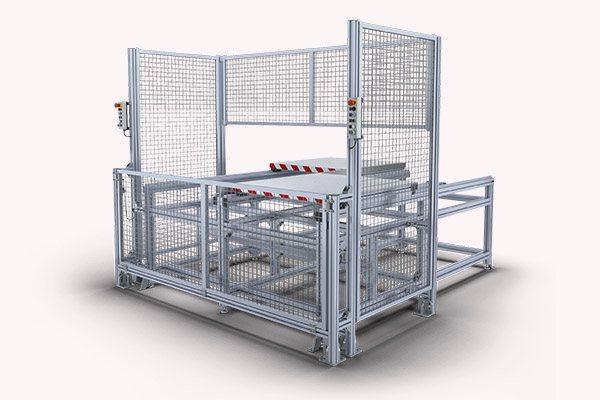
Two pick-up plates operating in pendulum mode in one plane
More information to our shuttle tablesMixing head 825 PRO
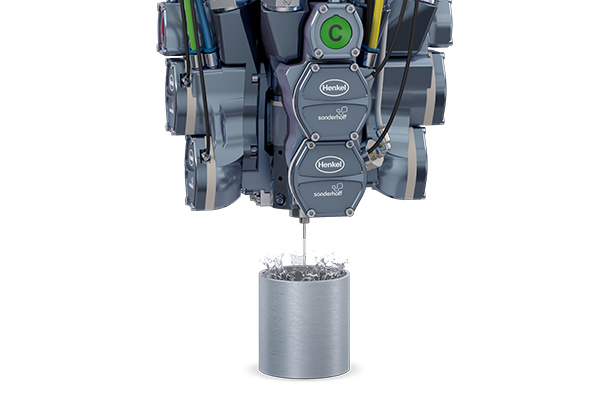
MK 800 PRO precision mixing head with high-pressure water rinsing or alternative component rinsing system
More information to our mixing headsDosing machine cabinet
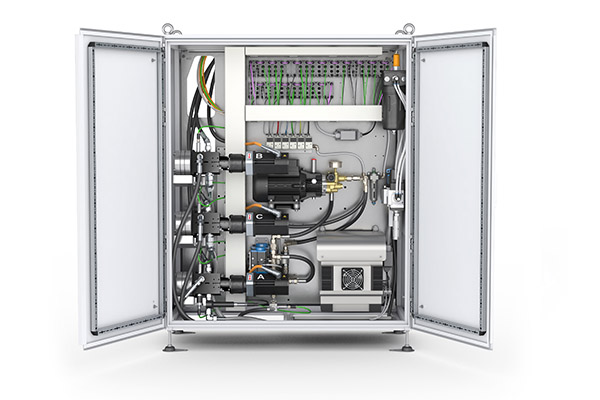
The dosing machine cabinet contains the components of the dosing periphery, e.g. the dosing pumps.
More information to our dosing machine cabinetsControl cabinet
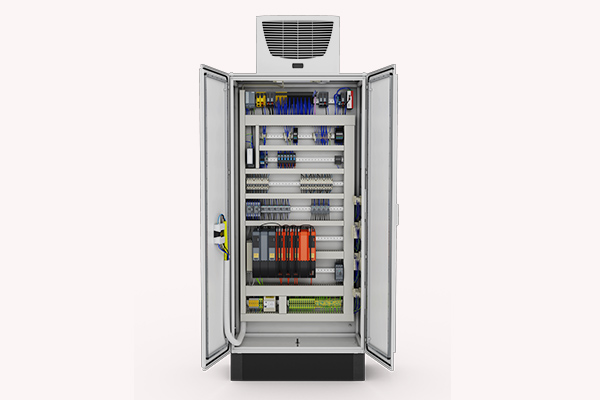
The control electronics, safety engineering and industrial PC are installed in the control cabinet.
More information to our control cabinetsSupply Tap
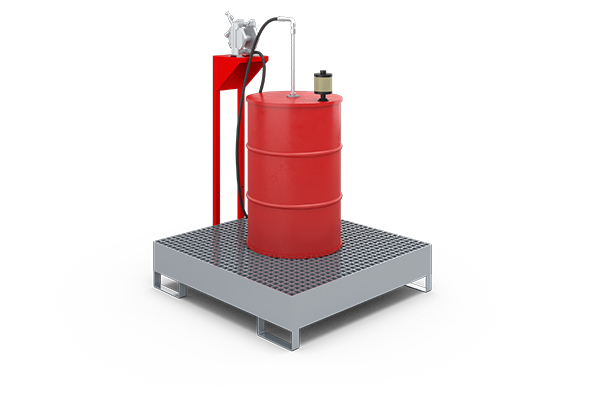
Optional: Automatic SUPPLY TAP drum refilling station for low-viscosity products, e.g. isocyanate (B-component)
More information to our refilling stationsElevator
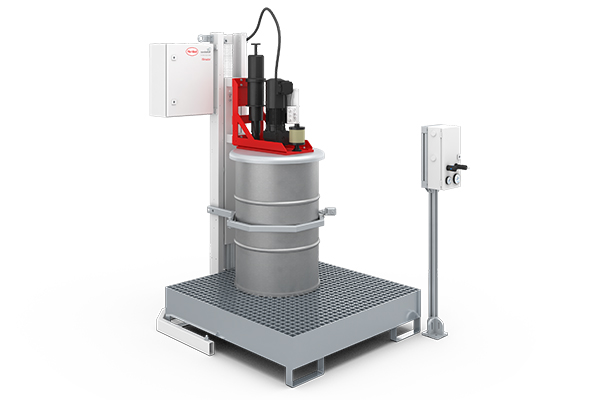
Optional: Automatic ELEVATOR drum refilling station for the A-component with pneumatic lift and agitator
More information to our refilling stationsThe basic solution for standard applications
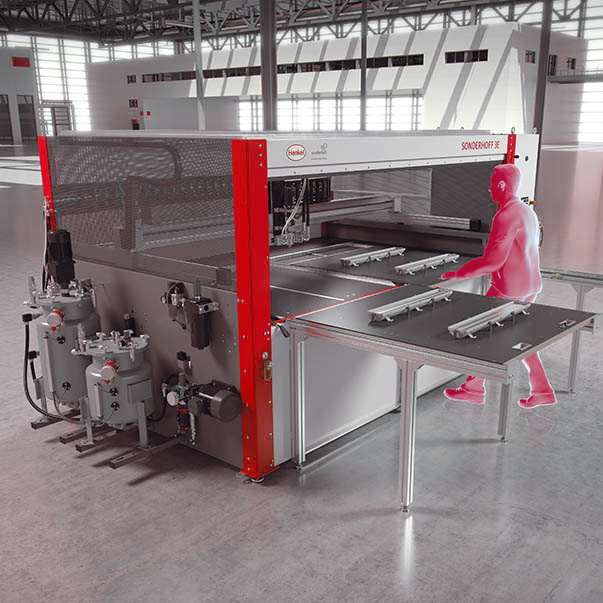
Dosing cell for easy handling and high process stability
The reference configuration of the 3E dosing cell shown is a low-pressure mixing and dosing system for two components for the partially and fully-automatic application of sealing foams.
The already compact design of the 3E dosing cell also takes up little space as a result because, as a CE-compliant dispensing cell, it does not require any additional safety fences or light barriers.
This is a pre-programmed Plug & Work version that is delivered pre-assembled in a container. As soon as electricity, water and compressed air are connected and the material is prepared in the material pressure tanks, production can begin. The costs of installation and training courses can therefore be kept to a minimum.
The dosing cell can process non-viscous, medium-viscosity and highly viscous material systems based on polyurethane. The application rate is adjustable from 0.5 to 5.0 g/s. Experience shows that this range covers 90 % of industrial applications.
The optional shuttle table allows components of different sizes to be processed in a single plane. Continuous operation is guaranteed by the two pick-up plates that can be moved manually in alternation. For larger parts, the two pick-up plates can be connected to form one large sliding table.
The CNC-controlled MK 825 BASIC precision mixing head for two material components applies sealing material into the housing groove of the linear luminaires with contour precision. With the sometimes very narrow and deep grooves, the metering of the sealing foams needs to be very precise.
The MK 825 BASIC precision mixing head performs this task with high metering precision and repeat accuracy. The dosing loop completes the foam gasket with a seamless, almost invisible coupling point.
With the CE-compliant 3E dosing cell, an immediate, safe start to production is possible, as well as efficiency-enhancing space and cost savings.
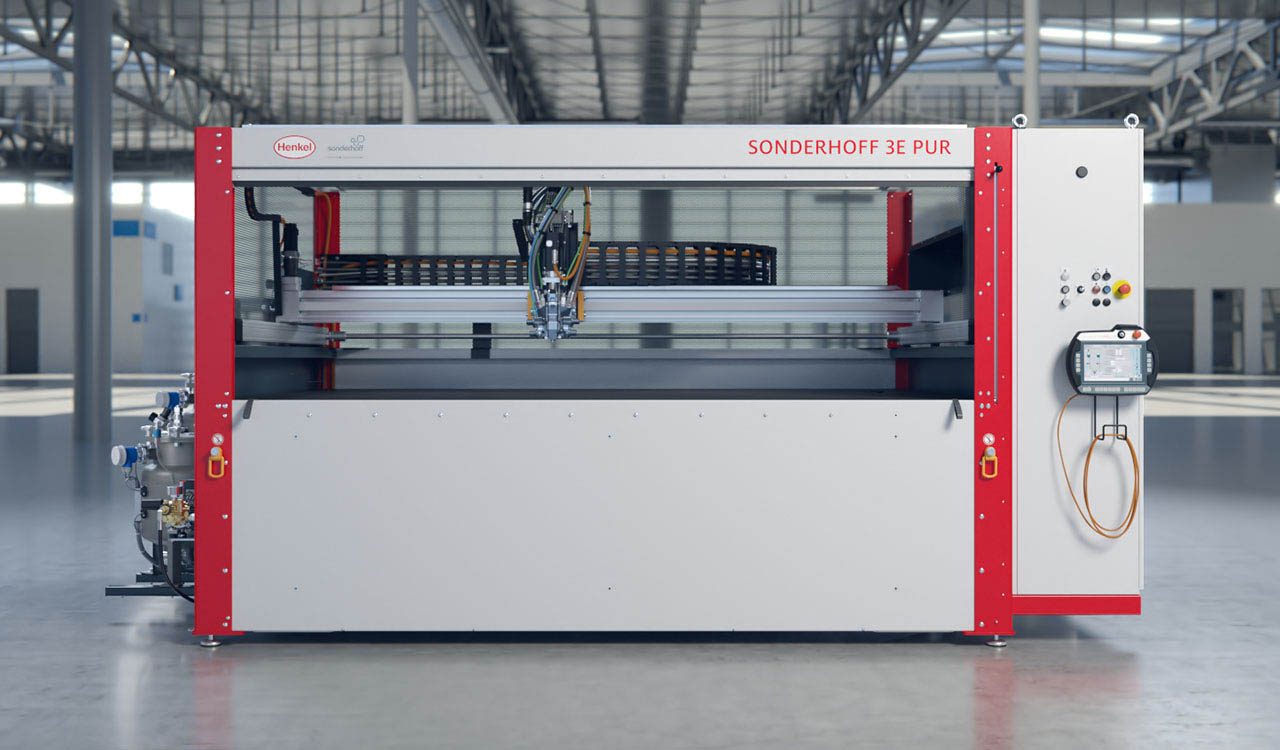