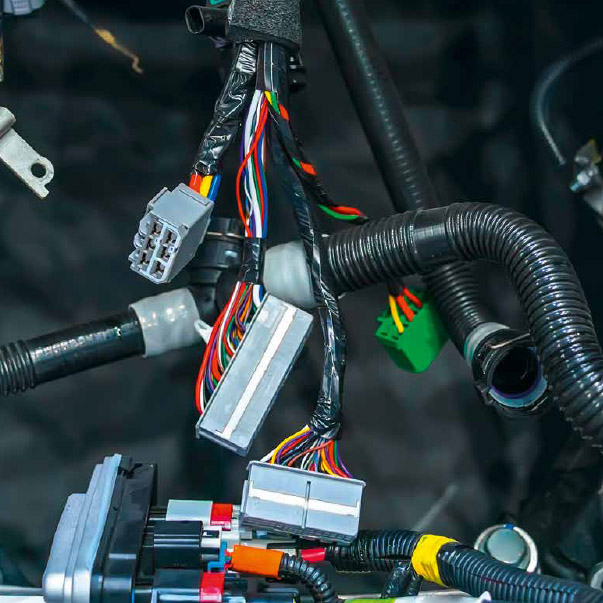
The modern and soon to be self-driving car is increasingly becoming a computer on wheels with more than 100 control devices and up to six kilometers of cable. The reasons for this are increased safety and comfort aspects as well as the electrification of the drive train for electric mobility. Cables also supply power to every consumer – from the oil pump to the vehicle lighting and from the radio to the sensor-controlled accelerator pedal.
This is why the number of control devices, sensors, actuators as well as electrical consumers and advanced driver-assistance systems is growing, and with it the amount of cabling. The cable harness distributes the energy for the consumers and the signals from the sensors and control devices in the car via multiple branching cable bundles.
This is where Henkel's products come in. We offer a range of suitable material systems for polyurethane foam-in-place molding, e. g. for connectors, cable grommets and battery fingers for the alternator, for potting the pins of connector plugs and for sealing electronics with polyurethane potting.
When it comes to foaming molded parts, sealing cable grommets, and sealing your electronics, are you looking for a complete solution consisting of a material system, dosing system and process automation from a single source?
Our perfectly coordinated system solutions allow you to reliably seal your cable grommets, connectors, battery fingers and electronics for robust use in road traffic so that they are waterproof and resistant to vibrations. The connectors or their cable connections and electronic components must be resistant to heat, vibration and other environmental influences and therefore receive special protection from our material systems to ensure a high level of reliability.
Do you need an automation system that adapts to your production requirements?
Our CNC-controlled mixing and dosing systems offer a high level of repeatable dosing accuracy and, thanks in part to systematic, sensor-based process monitoring, are also highly efficient. Thanks to their modular design, they can be flexibly integrated into existing production concepts.
Through our combination of individual material systems, customer-specific mixing and dosing machines and skilled process expertise, we offer solutions to address your technical and economic challenges.
Sealing, bonding and potting out of one hand
With SONDERHOFF SYSTEM SOLUTIONS (S3), you get everything from a single source, from material systems to mixing and dosing systems to contract manufacturing.
As a process expert, we offer OEMs and suppliers individual consulting for automation and application technology. Our material solutions with different properties include foam gaskets based on polyurethane or silicone as well as systems for bonding and potting. We support you with application engineering advice from the component design phase to fully automated material application using FIPFG technology.
Alternatively, with our contract manufacturing service, you get the option of us taking over the sealing, bonding or potting of your components directly for you, from the sampling of prototypes and small series to large-scale production.
Molded foaming of battery fingers
For the production of molded foam parts low foaming polyurethane potting is used. The 2-component reference material FERMADUR A-173-3-VP1 and B-81 (B component) is available for this purpose. It is characterized by excellent thermal insulation as well as high dielectric strength and heat resistance. There is also an optimal stiffness-to-weight ratio. In addition, the molded parts are characterized by their excellent elasticity and abrasion resistance, even under continuous stress.
Molded foaming of cable grommets
During the molding of a foam-in-place cable grommet, the material is also distributed into the spaces between the cable strands. This achieves excellent longitudinal watertightness, which prevents moisture from entering the interior from the engine compartment along the cable strands.
Molded foaming of connectors
Our perfectly coordinated system solutions for molded foaming allow your connectors to be protected for robust use in road traffic so that they are waterproof and resistant to vibrations. The connectors must also be resistant to heat and other environmental influences and therefore receive special protection from our material systems to ensure a high level of reliability.
Sealing of cable grommets
Loose parts in the wiring of vehicles are not permitted, as they can cause operational malfunctions and damage. Therefore, they must be particularly solid and well protected. The wiring from the engine compartment through the firewall of the engine compartment partition into the interior is made via cable grommets. The contour of the underside of the cable grommet is sealed to the installation side of the engine partition with sealing foam. Possible component tolerances are fully compensated.
Potting of electronic components
Electronic components such as windshield wiper electronics or the pins of a connector plug are potted with our polyurethane potting systems. The reference material presented for this purpose, FERMADUR-A-117-37 and B-RF (B component), is a room-temperature curing 2-component polyurethane potting compound. This material has a temperature resistance of -40 to +80 °C, is particularly mechanically stable and tear-resistant, and is resistant to shrinkage and stress.