Reliable mixing and dosing
With our DM 50x series equipment portfolio, we offer automation solutions for the mixing and dosing of 2-component reactive materials – especially polyurethanes, silicones and epoxy systems.
For this, the material components have to be prepared, i. e. stirred in the tank and loaded with air, and then conveyed to the mixing head. In the mixing head, the components are then mixed dynamically and the liquid sealant system is dosed in precise quantities.
Each of the process steps involved has its own specific requirements, which show how good a machine actually is. Our experience acquired over decades of machine development makes the difference and ensures the reliability of our machines.
Dynamic mixing makes the difference
The greatest possible level of material homogeneity after mixing 2-component material systems with different viscosities – even in the case of demanding, asymmetrical mixing ratios – can only be achieved with dynamic mixing. This is performed by our MK 800 mixing heads .
Material preparation begins with stirring
Depending on the material system, it may be necessary to load the A component with air, for example in order to obtain a fine-cell foam, or – just the opposite – to degas it for bubble-free clear potting. The agitator therefore has the function of not only counteracting sedimentation, but also of ensuring uniform air loading or degassing and temperature distribution. For an optimal degassing process there is also the option of thin-layer degassing. This takes place in the material pressure tanks.
Recirculation for a constant flow of materials
No matter how precise a pump is: It is a real challenge to achieve accurate dosing – especially in the case of long hose routes – if the material always comes to a standstill after dosing and has to be set in motion again for the next dosing step.
An exact application rate is particularly difficult to achieve when small quantities are to be dosed and the valve opening times are correspondingly short. For this reason we keep the material flowing at a consistent rate with our recirculation principle and keep the pressure in the system at a constant level as a result.
This is ensured by the precision gear pumps installed in the dosing machine cabinet.
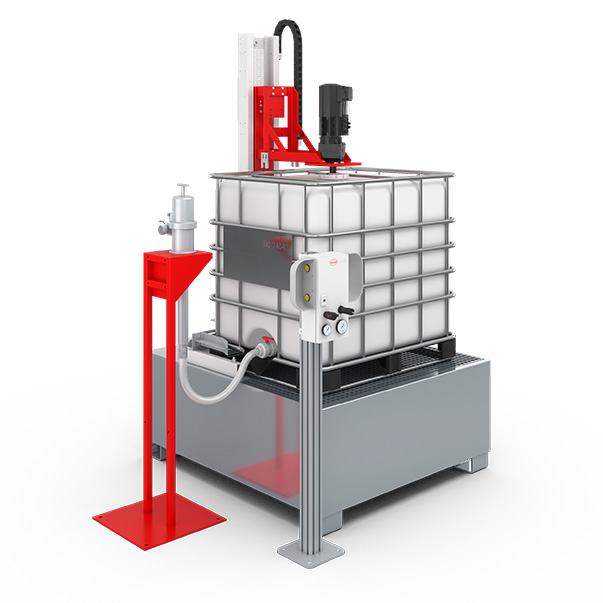
Accurate refilling for a continuous supply of material
When used in fully automated manufacturing processes, automatic refilling stations ensure material-specific preparation, homogeneous consistency and a continuous supply of materials to the component containers of the mixing and dosing system – without exposure or contamination of the products to be filled. Partially equipped with an automatic lifting device for more operating convenience and greater occupational and system safety. Production interruptions are therefore a thing of the past.
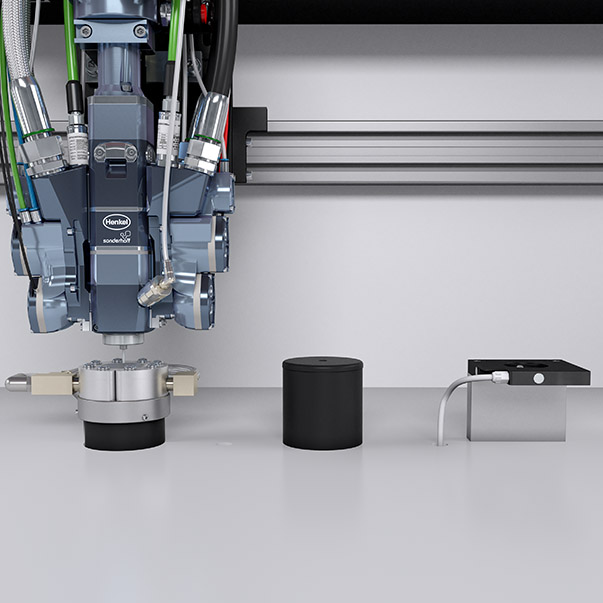
Optional Equipment used to increase process and dosing accuracy
Additional equipment options can be ordered for the DM 50x dosing machine series which further increase the process and dosing accuracy, e. g.:
- Sensor for spare part recognition
- Pneumatic AIR-CLEAN nozzle cleaning
- NOZZLE-CONTROL nozzle measurement unit
- WEIGHT-CONTROL dosing weight control
- High pressure water flushing of the mixing chamber
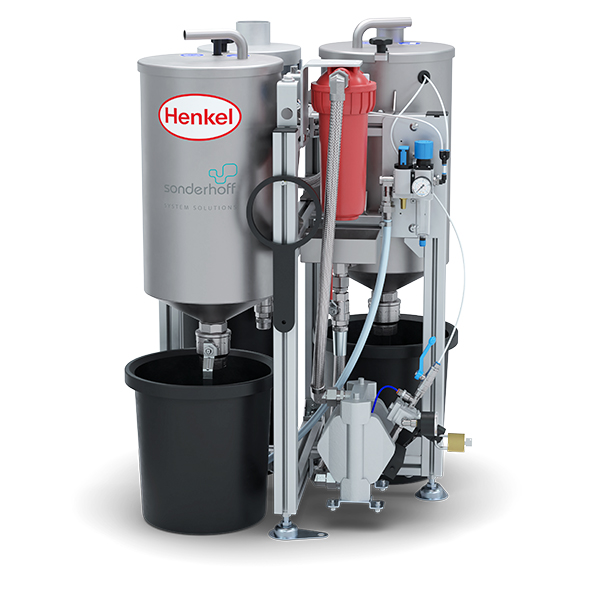
The new Sonderhoff Rinsing Water Recylcing System
Sonderhoff mixing and dispensing machines are sustainable because they use Formed-In-Place-(Foam-Gasket) / FIP(FG) technology to apply only as much material as necessary. In addition, the mixing chamber is cleaned of material build-up using an ecological high-pressure water rinsing system. Compared to conventional solvent rinsing, only tap water is used. Solvents, on the other hand, are not ecologically degradable and cause costs for additional purchases and disposal.
With the newly developed rinsing water recycling system, the rinse/process water for high-pressure water rinsing is cleaned in a two-stage filtering process. The filtered rinse water is then available as process water for several further rinsing cycles.
This significantly reduces the freshwater consumption of the high-pressure water rinsing system as well as the amount of water that needs to be disposed chargeable to the sewage system.