SONDERHOFF DYNAMIC SPEED
Up to now, the speed of the dispensing application for sealing and bonding components has generally been determined by the component geometry, particularly the radius size. In tight radii, the application speed of the CNC-controlled mixing head is lower than with larger radii. This means that the radius for applying the seal determines the constant application speed for the entire component.
With the new speed-dependent dispensing technology SONDERHOFF DYNAMIC SPEED, this radius-dependent traversing speed no longer applies. Instead, the speed of the material application and the component geometry are decoupled from each other, so that the maximum possible application speed is always achieved throughout the entire component contour during dispensing.
During programming, the operator enters the maximum speed and the radius size, and the dosing system automatically calculates the maximum possible speed on the straight lines and in the radii.
The basic prerequisite is that the pumps are positioned as close as possible to the mixing head valves.
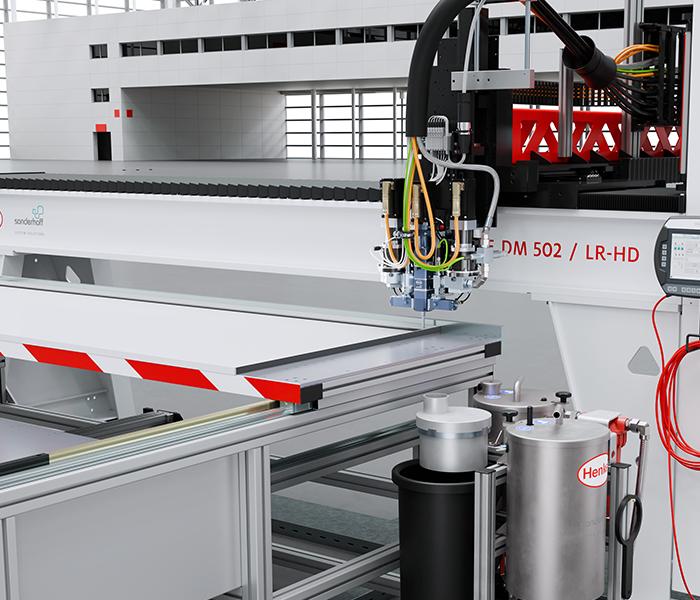
As a user, you can save up to 50 % of the cycle time with SONDERHOFF DYNAMIC SPEED and thus achieve almost twice the production output.
If you are already using a Sonderhoff mixing and dosing system, your CNC dosing programs created for different components can be easily adopted.
Dosing application with SONDERHOFF DYNAMIC SPEED
Animation of SONDERHOFF DYNAMIC SPEED
(radius 13 mm and maximum speed at 44 m/min)
Animation of SONDERHOFF DYNAMIC SPEED
(radius 8 mm and maximum speed at 34 m/min)
The CNC-controlled mixing head accelerates from the starting point at the maximum application speed set by the operator, e.g. 44 m/min, and maintains this speed until shortly before the radius, then automatically decelerates to the maximum possible radius speed and travels with this speed through the radius.
After the radius, the CNC accelerates the mixing head back to the specified maximum speed of 44 m/min. on the straight line. This sequence is repeated up to the coupling point, which is closed with the maximum radius speed.
To ensure that a consistently precise sealing contour is always achieved with SONDERHOFF DYNAMIC SPEED, the dosing system controls the material discharge depending on the speed currently being travelled.
The illustrations below show a control cabinet panel with external dimensions of 2500 x1250 mm (length x width) and the application of a seal, particularly the start/stop point, the dispensing direction and the various areas in which the mixing head is accelerated, decelerated and travelled at full application speed.
Compared to a seal application at a constant speed, SONDERHOFF DYNAMIC SPEED allows you to save up to 50 % of the cycle time and thus achieve almost twice the production output.
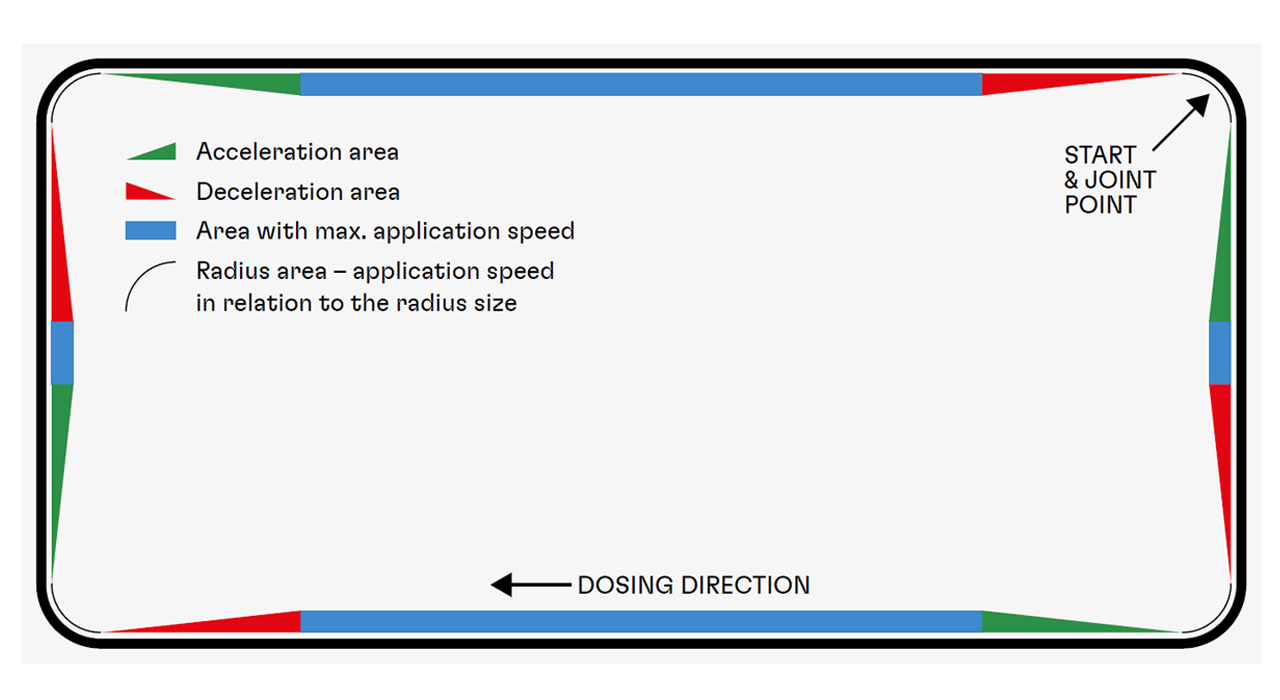
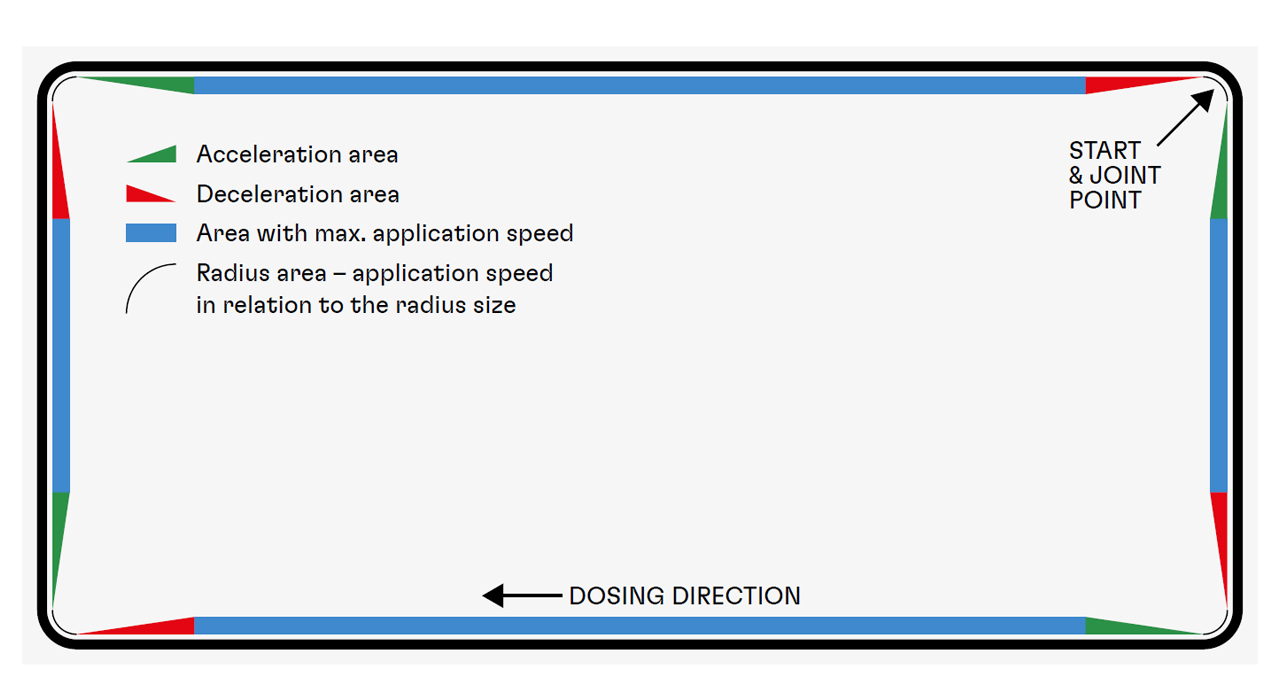