Compact, mobile, reliable and easy to operate
The mobile workstation for processing and dispensing of highly filled, abrasive and highly viscous LOCTITE 2K epoxy structural adhesives
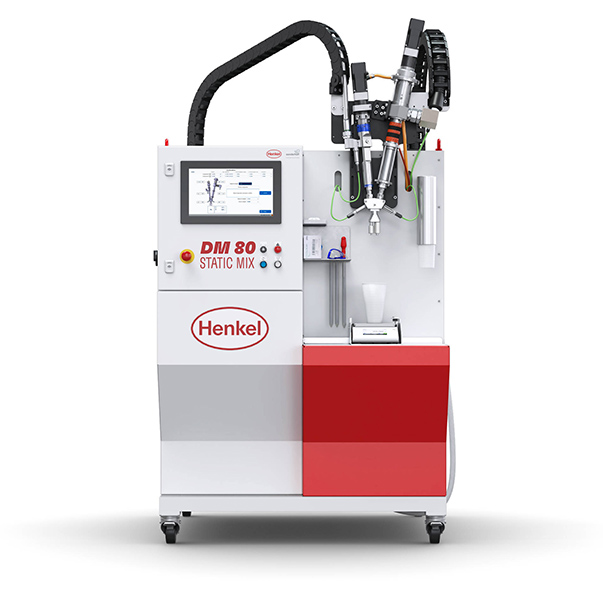
The DM 80 STATIC MIX is designed to be used in various industrial sectors, such as aircraft construction, car body construction, commercial and special vehicles, agricultural machinery, defence, railway and mobile homes, to name a few.
Flexible today and tomorrow
The compact design of the DM 80 STATIC MIX fulfills all the technical and quality requirements of suppliers for aircraft construction and other industrial applications, where precise processing and dispensing of 2K materials, automation of manual processes as well as traceability of process sequences are crucial to the quality of component bonding.
Guaranteed quality
With the launch of the DM 80 STATIC MIX, we guarantee the quality you require.
The DM 80 STATIC MIX enables efficient material consump- tion and shorter production times, as well as higher quality, consistency and reliability in mixing and dosing. Additionally, it incorporates Industry 4.0 functionalities, a worldwide service network, and offers the possibility of integrating into your automation systems.
Simple processing and space-saving use
The DM 80 STATIC MIX is designed so that the operating personnel can fulfill the most diverse tasks easily and safely. Operation and visualization are carried out via a
15.6“ touchscreen.
A further feature is the process data logging, in which material pressures, pump torques, weighing data, correc- tion factors and alarm data are recorded and saved. In addition parameters for the discharge quantity, mixing ratio and the dosing time can be set. Particularly note- worthy is the interactive, menu-guided calibration and dosing process, which is permanently monitored and checked by a precision scale.
The dosing machine is mounted on a rollable chassis.
Spare mixing elements, separator for calibration, gloves and filling cups are within easy reach. The easy accessibility of the machine makes it quick and easy to carry out main- tenance and servicing work.
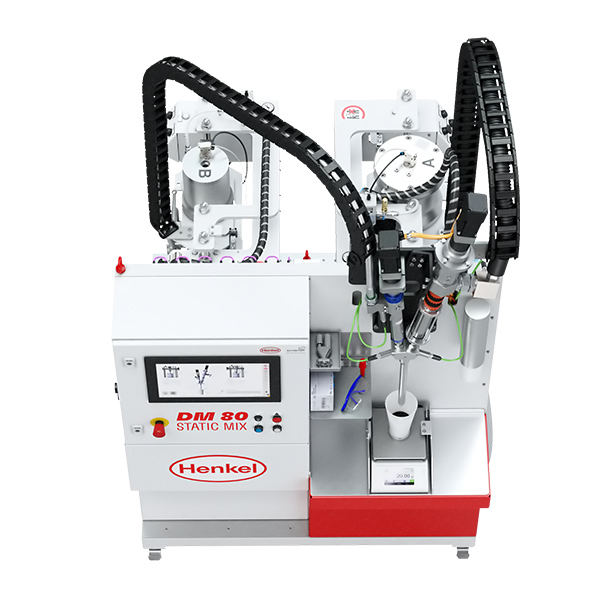
Animation of SONDERHOFF DM 80 STATIC MIX - Long Version
Animation of SONDERHOFF DM 80 STATIC MIX - Short Version
DM 80 STATIC MIX - Overview and special features
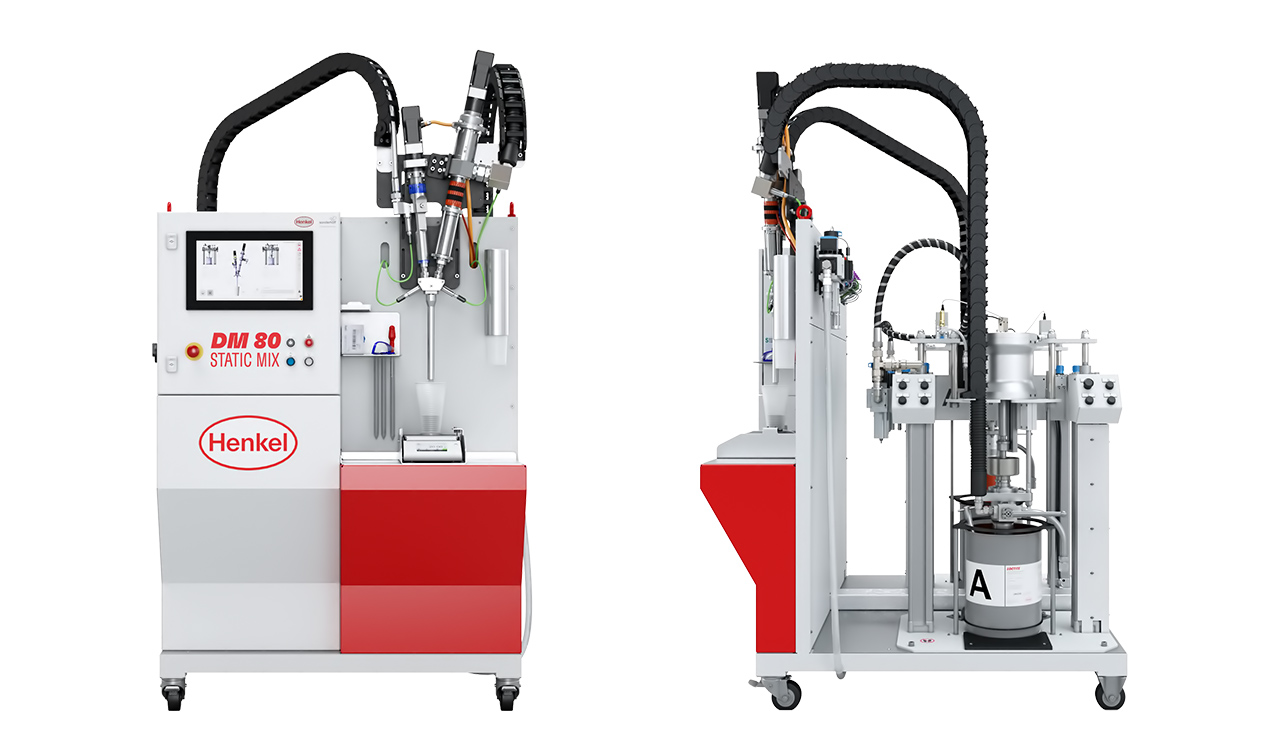
Touchscreen
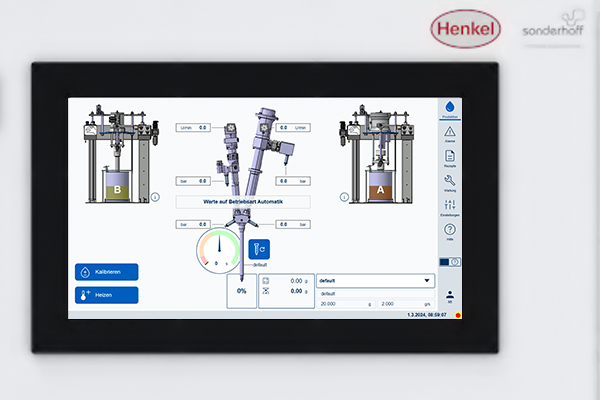
Visualization and operation via 15.6“ touchscreen with interactive menu- guided calibration and dosing process
Process data logging
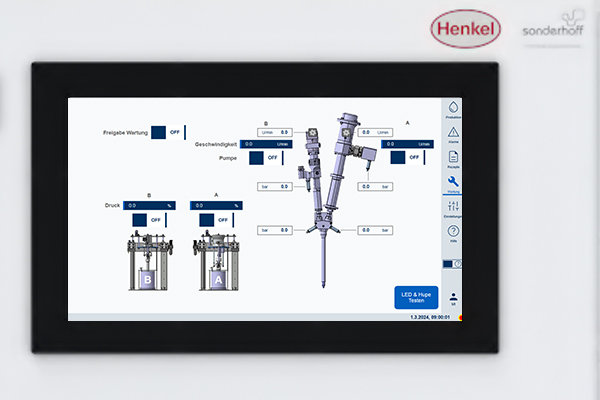
of material discharge quantities, mixing ratios, material pressures, pump torques, weighing data, correction factors and alarm data
Operating mode control panel
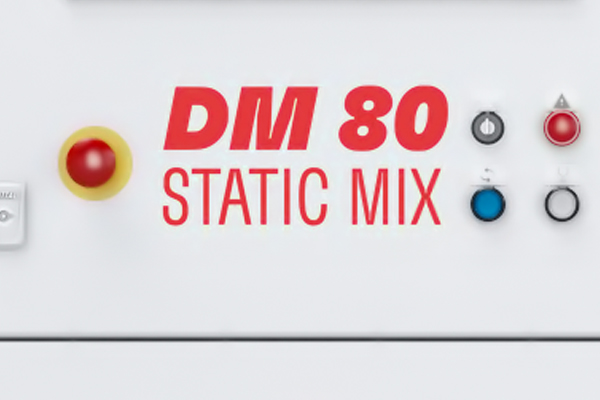
with warning lights, key switch for preselecting the operating mode and EMERGENCY STOP shutdown
Rollable chassis
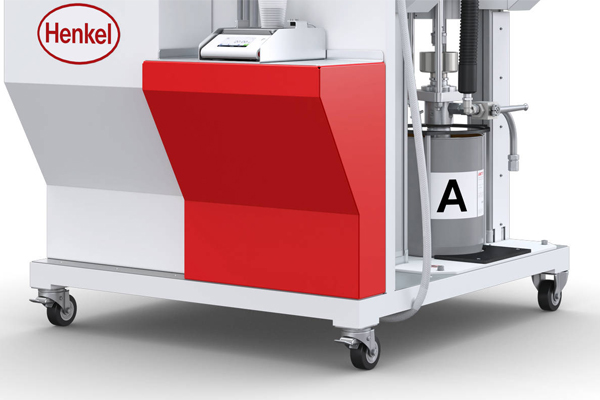
Dosing machine mounted on rollable chassis
Precision eccentric screw pumps
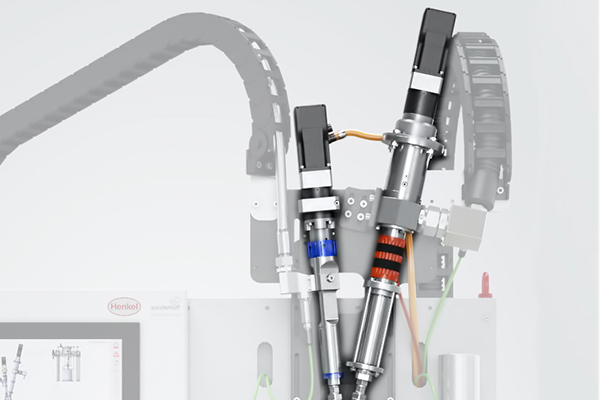
in sizes 8.2 ccm/rev (A comp.) / 1.8 ccm/rev (B comp.), with servo drives and automatic pressure control
2K precision mixing head with static mixing
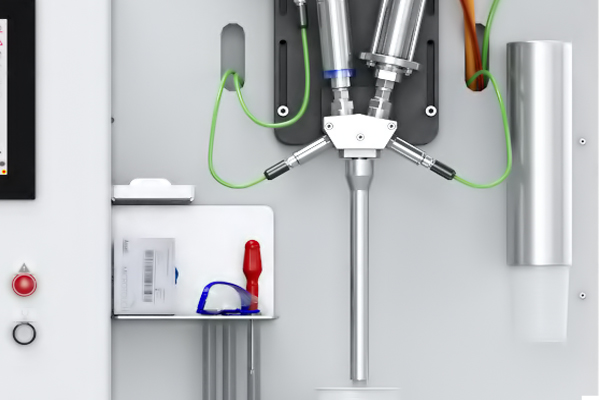
with servo drives, for discharge rates infinitely variable from 1.0 to 2.5 g/s and mixing ratios from 10:1 to 1:1 (depending on pump size and material viscosity)
Integrated precision scale
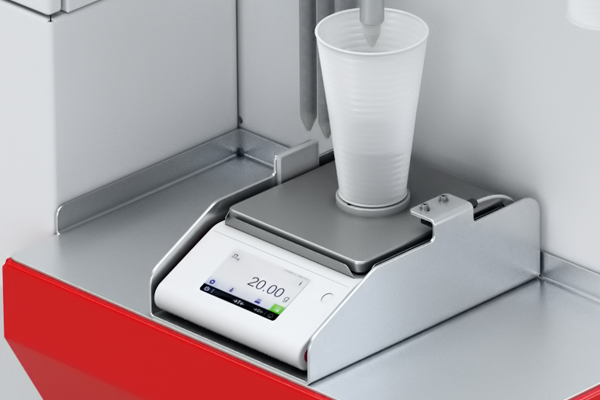
for permanent weighing check for calibration and dosing
Accessories
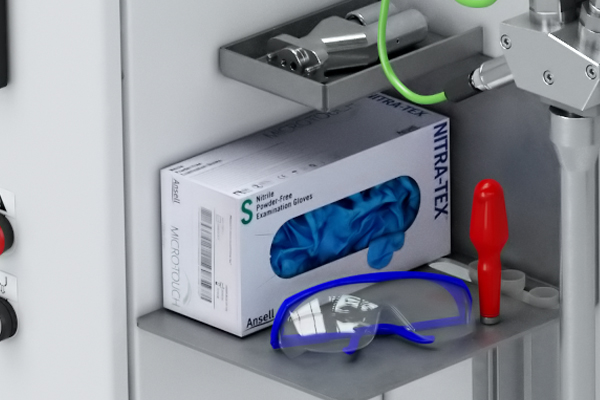
such as spare mixing elements, separator for calibration, gloves and filling cups are immediately available
Pressure-controlled separator
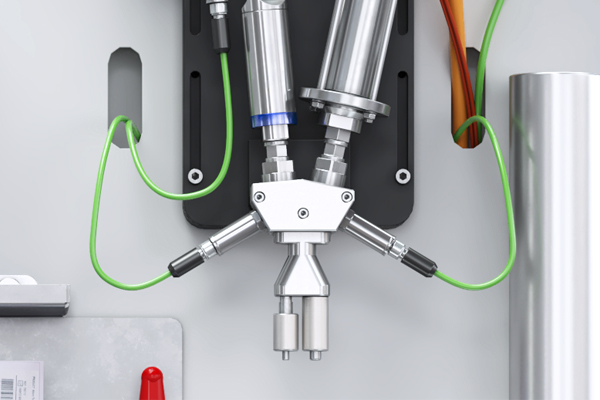
for interactive, menu-driven calibration function
Cartridge filling
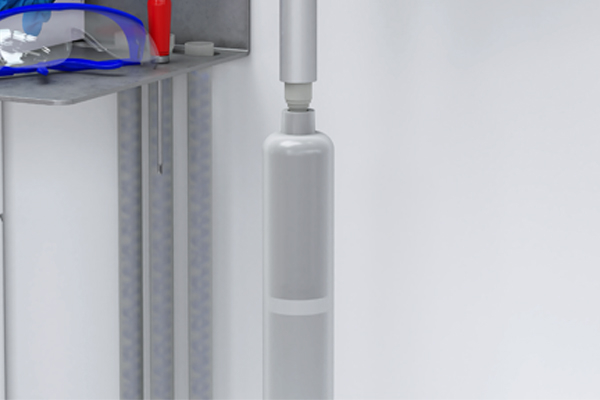
in 230 ml Semco cartridges (optional)
Pressure gauge
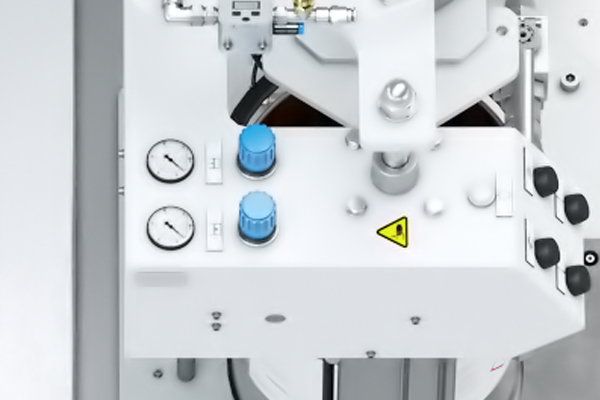
Setting and pressure display by means of pressure gauge for barrel pressing and aeration pressure
Compressed air connection
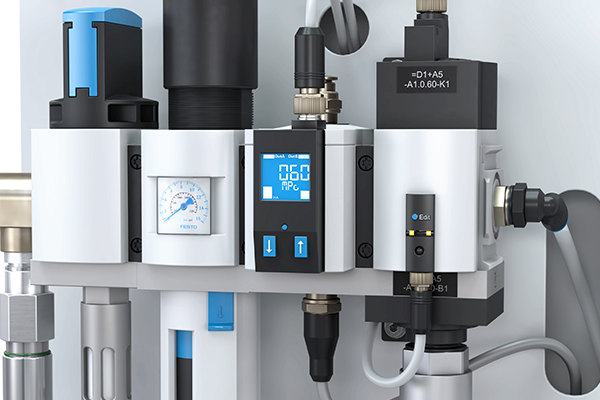
with filter pressure reducer and maintenance unit for supplying the pneumatic consumers
Pail change
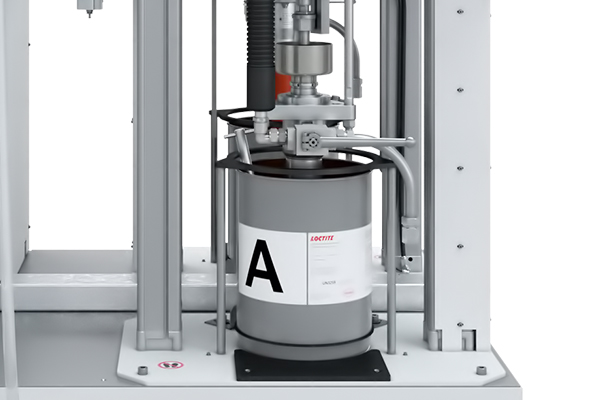
easy to implement, with little material loss
Safety ram press
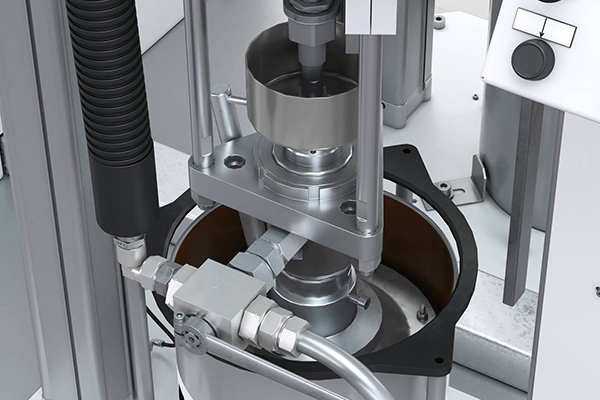
for conveying material from 20 liter pails and functions for automatic (de-)aeration
Material tempering
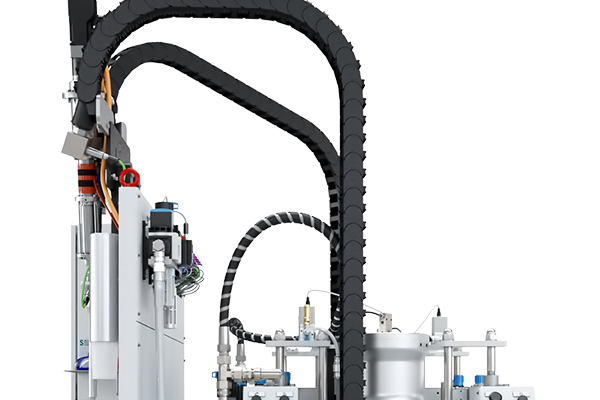
Four individually controllable heating circuits: Scoop piston pump, hose package, dosing pump and mixing head incl. support tube (only for A-component)
Mixing head with pressure monitoring
and flow-optimised material dosing
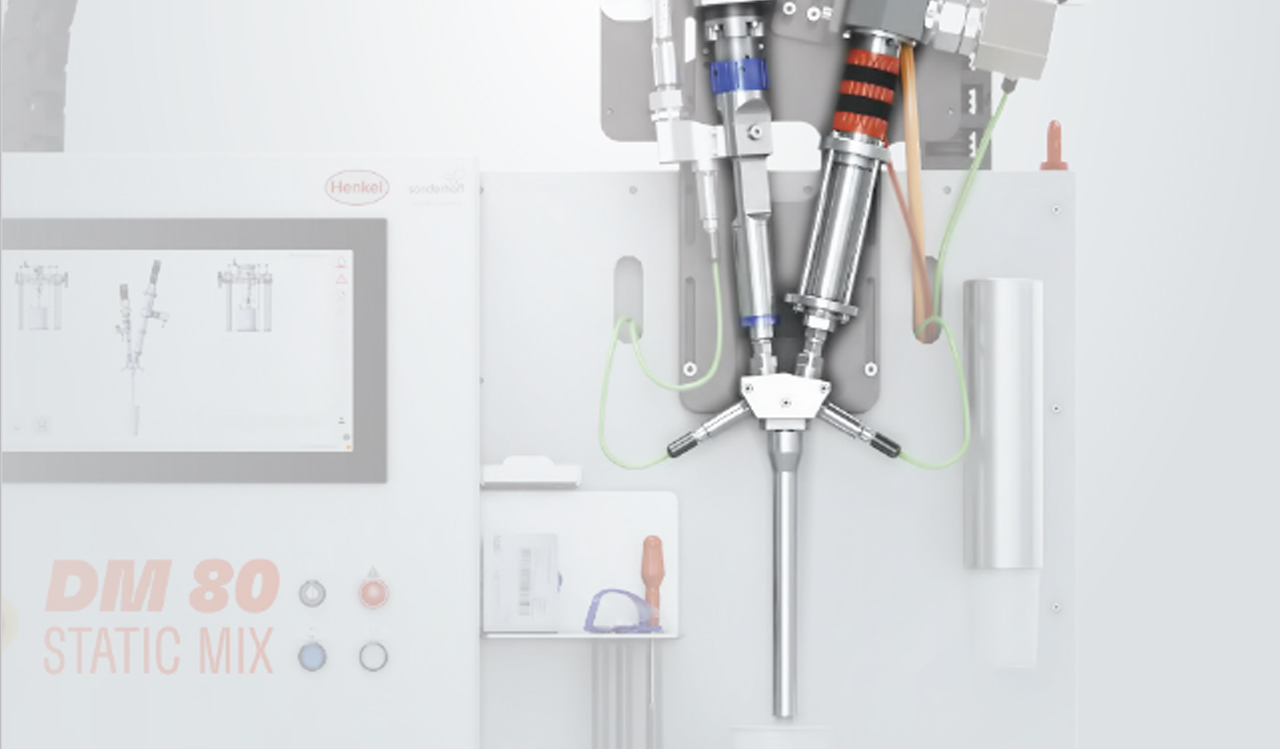
The servomotor-driven 2K precision mixing head MK 34 in stainless steel design and with integrated heating function is intended for pressure-monitored, static mixing of the material components for discharge rates from 1.0 to 2.5 g/s, although other discharge rates can also be configured. The mixing head has an optimized installation space which ensures flow-optimized material dosing.
The mixing ratio is infinitely variable from 10:1 to 1:1, but this depends on the pump size and material viscosity. Mixing is carried out by the ME 13/24 static mixer with low back pressure and high flow rate.
The automatic, pressure-controlled material feed to the mixing head is carried out by servo-driven precision eccentric screw pumps in sizes of 8.2 (A-comp.) and 1.8 (B-comp.) ccm/rev. For this purpose, pressure sensors are installed for process monitoring with reduced interference contours.
General description
- Pressure-monitored and servomotor-driven mixing head (in stainless steel design) for static mixing
- Designed for flow-optimized material dosing
- With integrated heating function
- Pressure sensors before and after the precision eccentric screw pumps for controlling the material feed of the scoop piston pumps of the RAM press
- Mixing by the ME 13/24 static mixer with low back pressure and high flow rate
- Additional support tube for pressure safety and prevention of a pulsing ME 13/24 static mixer
- Min. dosing volume: 20 g
- Max. dosing volume: container quantity for A and B material component
- Pressure-controlled separator for interactive, menu-guided calibration function
Technical data | 2K Precision Mixing Head MK 34 |
Dimensions (H x W) | 1,113 x 413 mm |
Operating pressure | max. 30 bar |
Application rate | from 1.0 to 2.5 g/s, other application rates on request |
Dosing accuracy | approx. +/- 3 % |
Mixing ratio | 10:1 to 1:1 infinitely variable (depending on pump size and material viscosity) |
Viscosity processing range | from 10,000 to 1,000,000 mPas, other viscosities on request |
Operation and visualisation
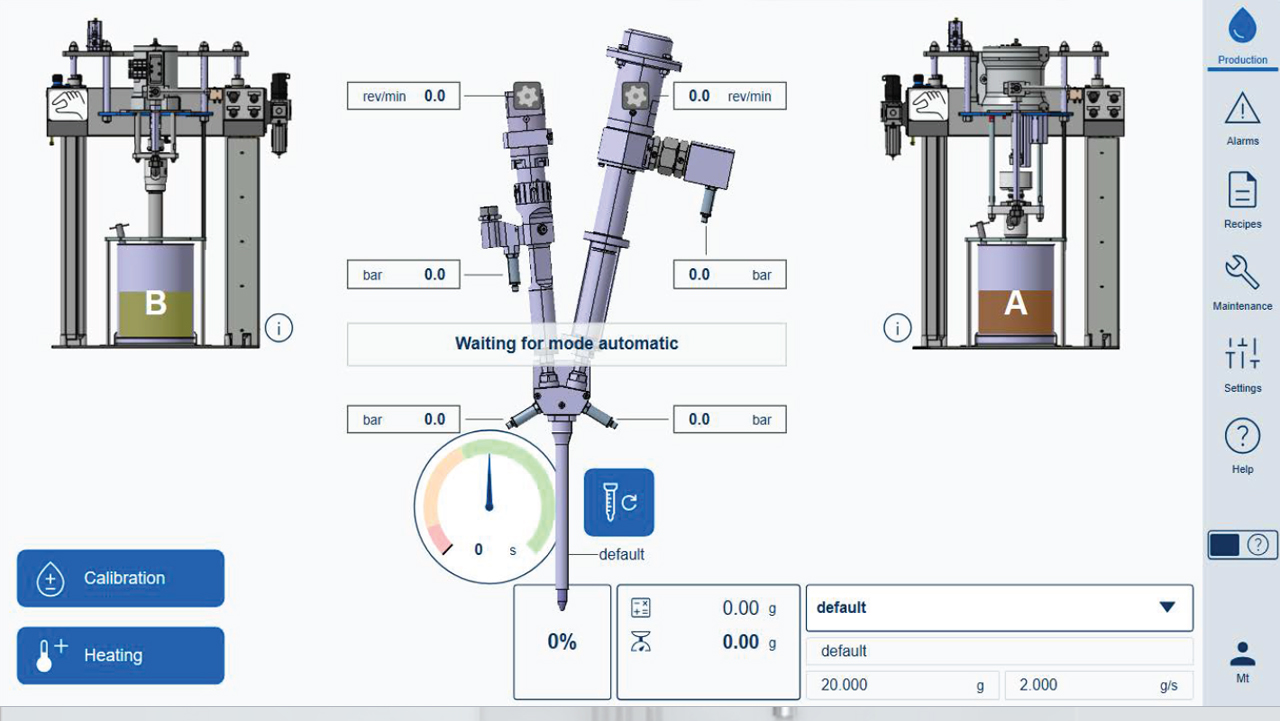
Production Menu
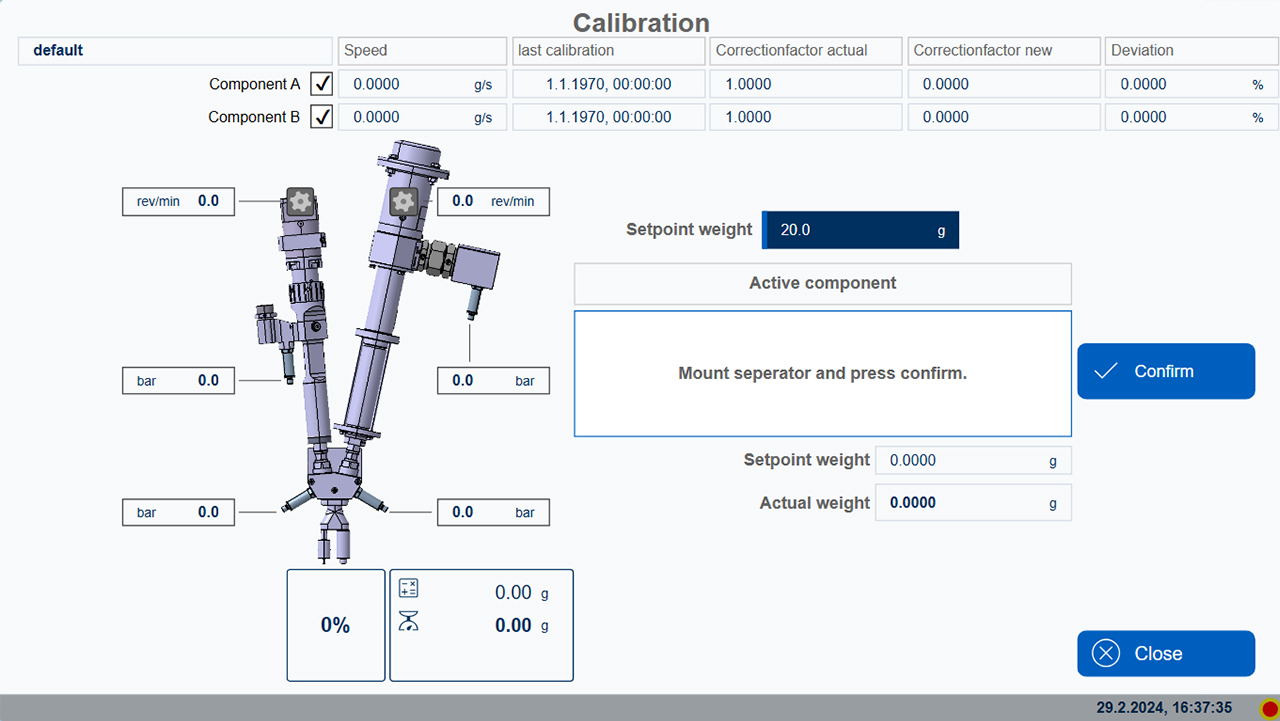
Calibration Menu
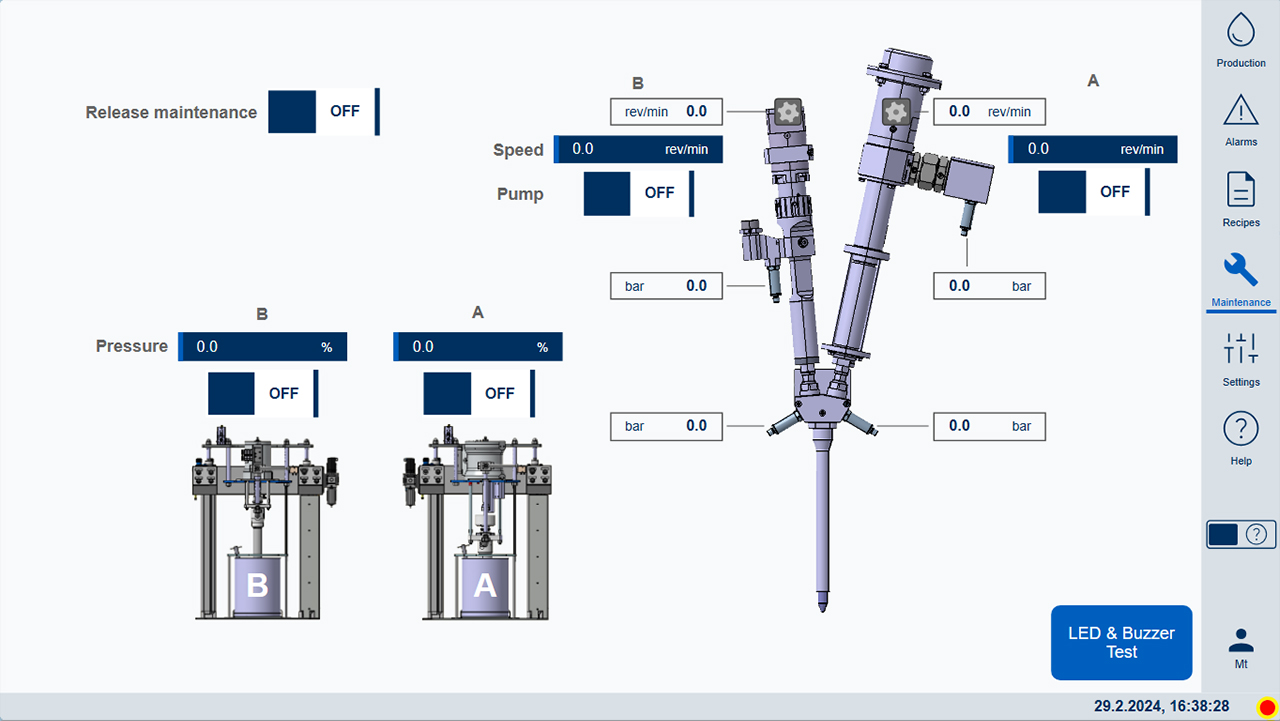
Maintenance Menu
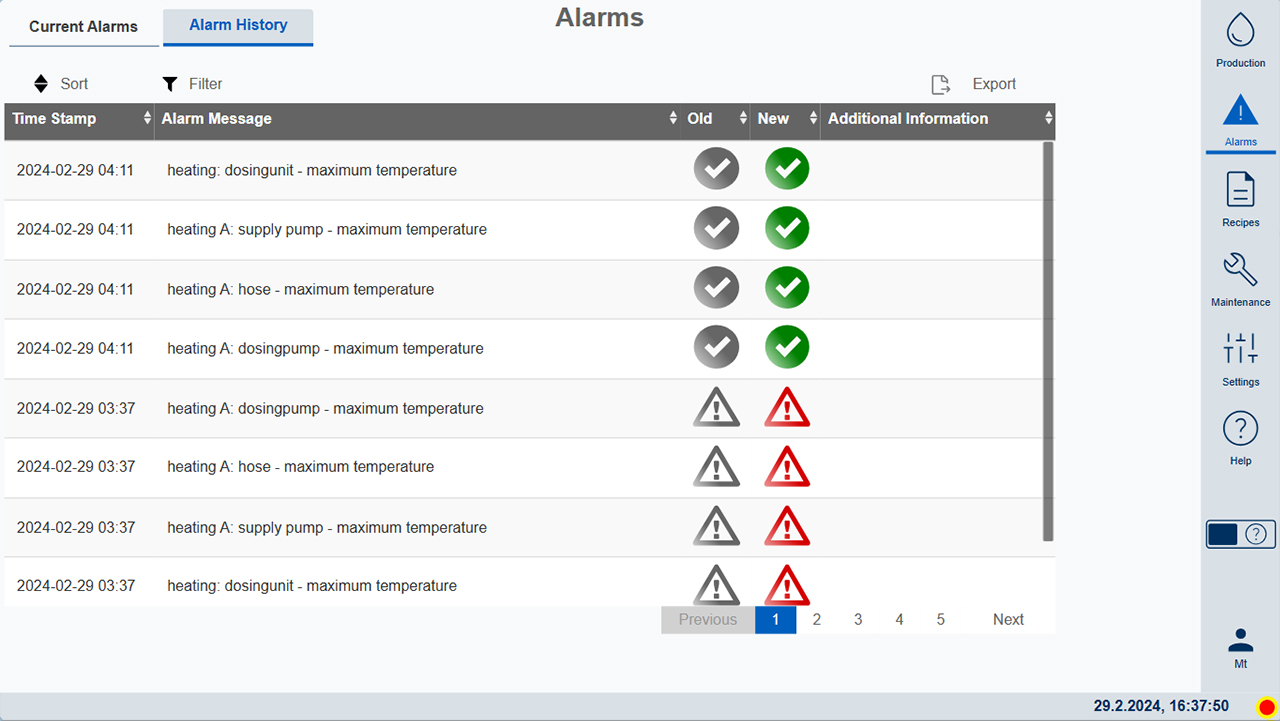
Alarm Messages
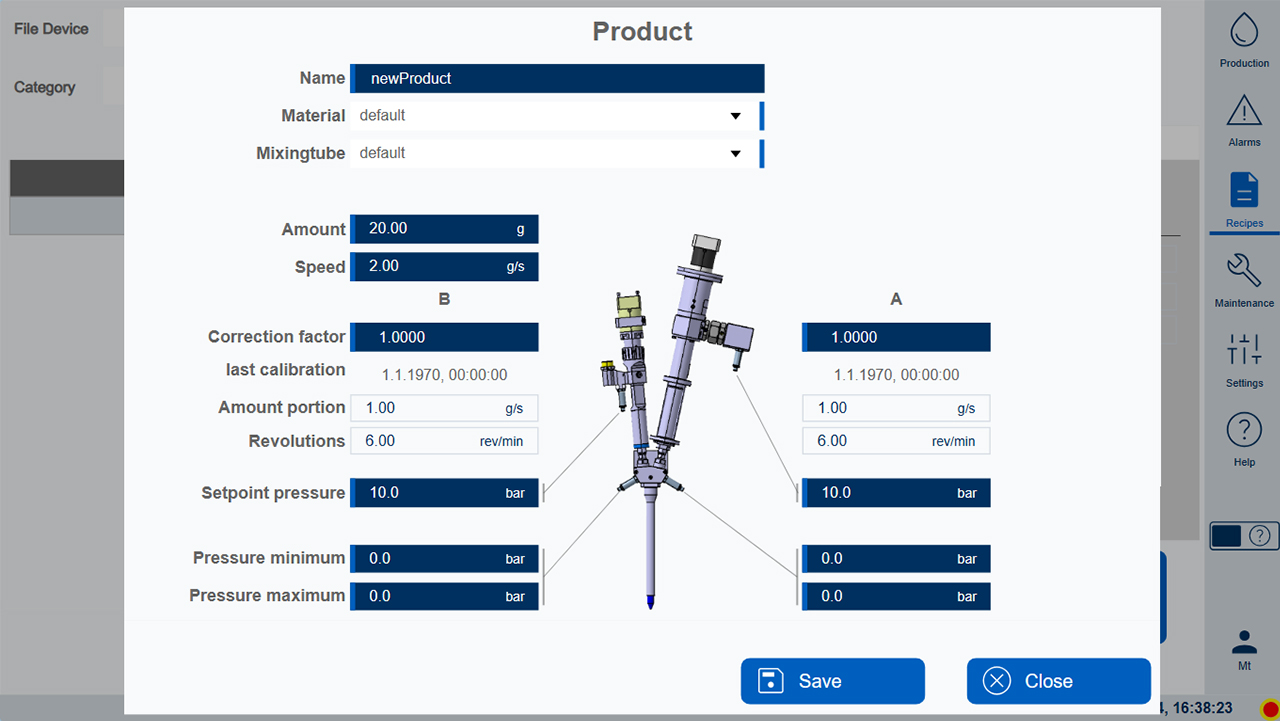
Recipe Setting
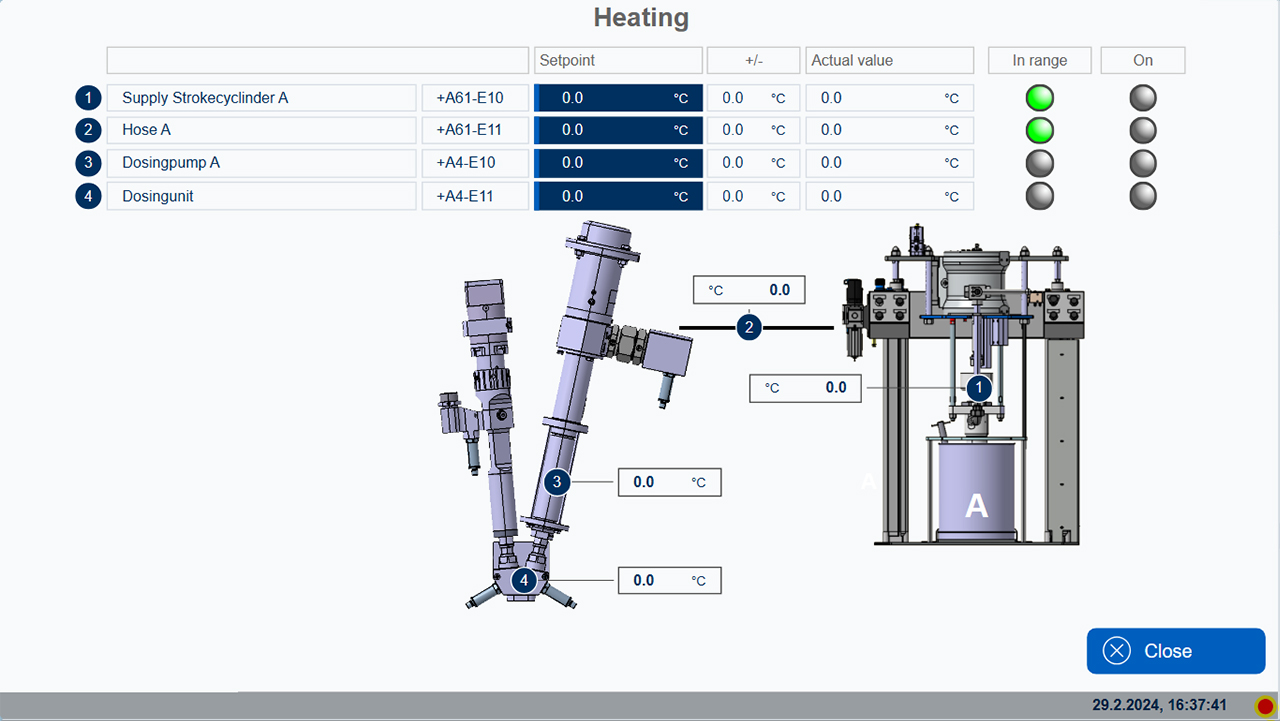
Tempering
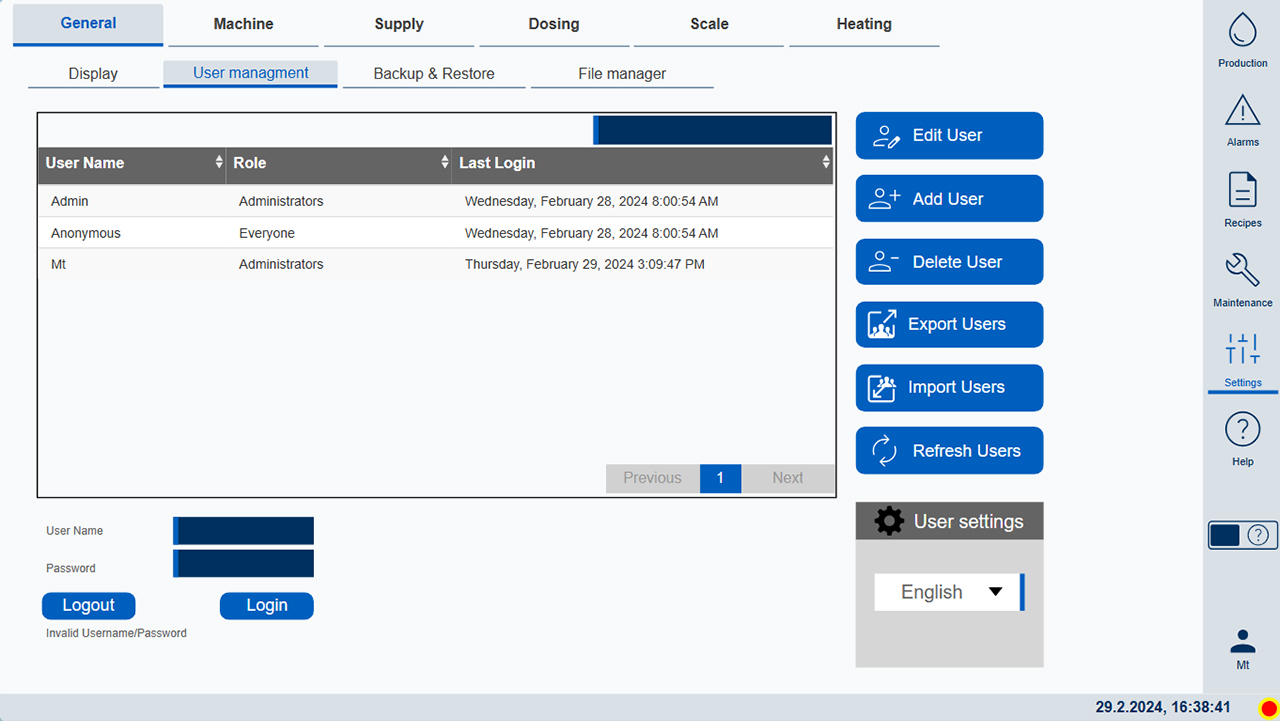
User Administration
Technichal Data
Control CONCEPT |
|
CONTROL |
|
MIXING HEAD |
|
MATERIAL PREPARATION / CONVEYING |
|
HOSE PACKAGE |
|
MATERIAL TEMPERATURE CONTROL |
|
PNEUMATICS |
|
CONNECTION VALUES |
|
QUALITY ASSURANCE |
|
GENERAL |
|
DIMENSIONS AND WEIGHT |
|
Dimensions in mm
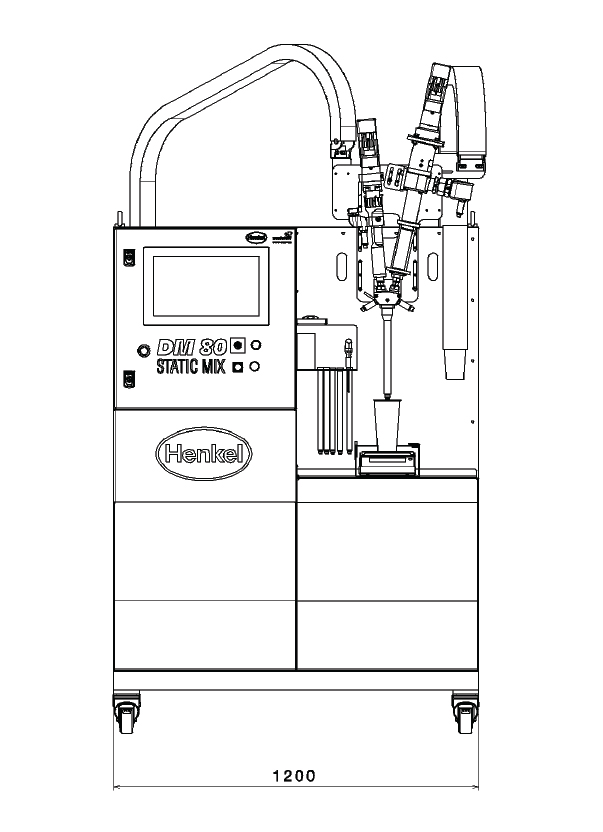
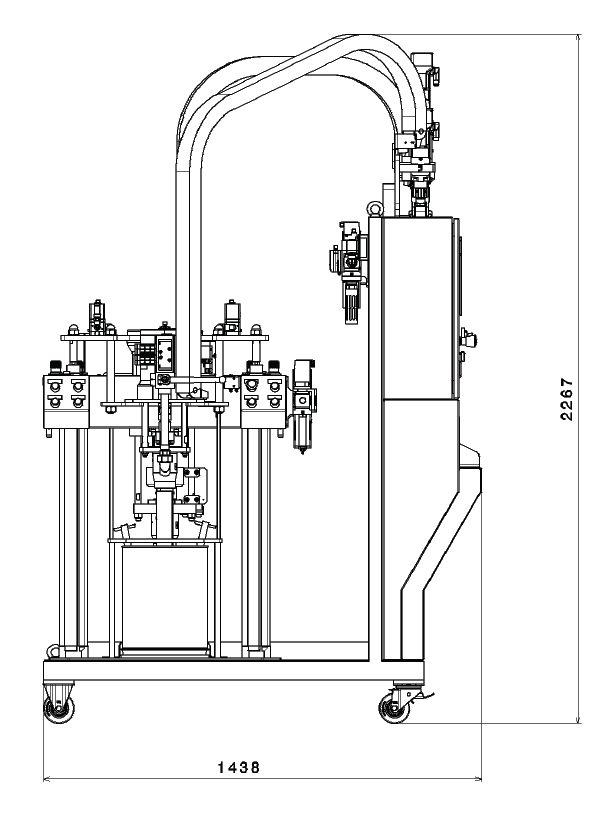