System solutions for sealing of battery housings for e-bike and e-scooter
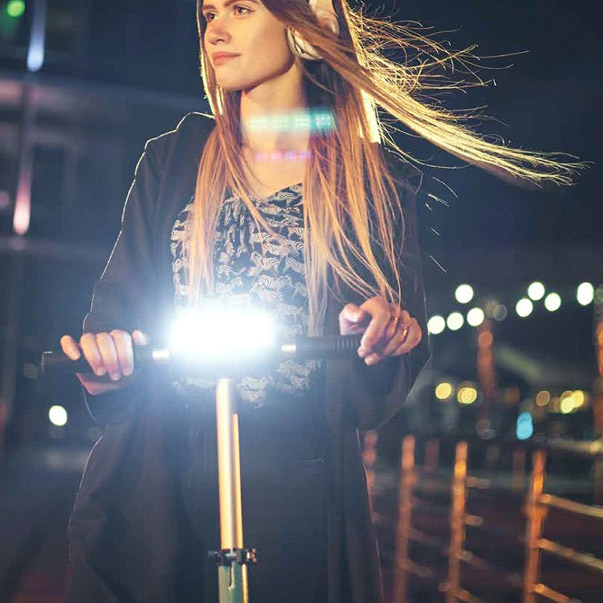
In the sharing economy, the focus is no longer on ownership but on the service: Instead of owning a car, mobility itself is far more important. It should be digital and emission-free. Urban micromobility in particular is becoming increasingly electrified, and air quality is improving as a result. Especially because of the growing number of pedestrian zones in city centers, and because fuel and car parking are becoming increasingly expensive, new urban mobility concepts are becoming essential. Where public transit coverage ends, new forms of transportation like e. g. battery-powered e-scooters can have a positive impact on often crowded city streets and parking lots.
This is, because e-scooters and e-bikes are particularly suitable as a means of transport for the first and last mile to the destination. A wide range is available to those who want to get from the train station or parking lot to their workplace, or go shopping in the city center. Various rental and sharing services are recording enormous levels of growth. Some e-scooters are folding and portable, and can be conveniently taken along in subways or buses. In effect, this means you can ride from your front door to your desk.

When it comes to sealing your battery housings for e-scooters and e-bikes, are you looking for a solution consisting of a material system, dosing system and process automation from a single source?
Our perfectly coordinated system solutions enable you to reliably seal a wide variety of battery housing designs against moisture and shocks, allowing robust use in road traffic.
Do you need an automation system that adapts to your production requirements?
The modular design of our mixing and dosing systems allows flexible use, with excellent integration into existing production concepts. These can be operated easily and intuitively without requiring much training. Our robot-controlled mixing and dosing systems offer high levels of repeatability and dosing accuracy, and are highly efficient thanks to systematic process monitoring.
Our solutions therefore offer you precisely the levels of durability, quality and reliability that your customers expect from your products.
Tailored material systems for maximum product safety

We carry out developments individually for your specific requirements
For sealing the battery housings of e-bikes and e-scooters, we provide you with a perfectly coordinated system solution consisting of a sealing foam or potting compound that meets your requirements, as well as a mixing and dosing system for high precision, fully automatic material application controlled by contour robots.
For the seamless sealing of battery housings, we supply the reference material FERMAPOR K31-A-9675-5-VP and B-4 ( B- component). This 2-component polyurethane foam has proven effective over many years in use by leading manufacturers, and reliably seals battery housings against moisture and other external influences. The foam gasket is seamlessly applied with our fully automatic dosing machine, providing excellent sealing in the installed state due to compression of the foam structure.
Our 2-component FERMADUR polyurethane potting systems are used to seal the electrical connections and electronics of e-bikes and e-scooters against moisture and shocks. The two material systems for sealing foam and potting can also be processed in combination with a mixing and dosing system for 3 components.
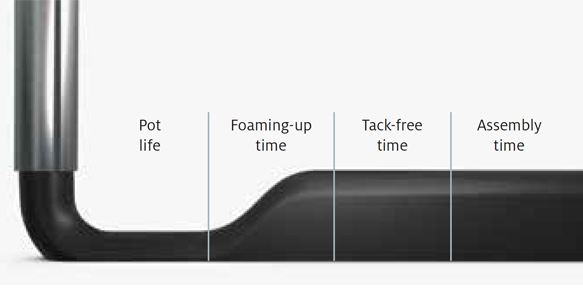
The different reaction phases of the sealing foam in the chronological sequence
Reference material
FERMAPOR K31-A-9675-5-VP | ||
FERMAPOR K31-B-4 | ||
Mixing ratio |
4.5 : 1 | |
Pot life time | 40 sec. | |
Tack-free time | 7 min. | |
Viscosity of the A component |
1,500 mPas | |
Density of the foam |
0.23 g/cm³ | |
Hardness (Shore 00) | 43 | |
Temperature resistance | from -40 to + 80 °C | |
Pretreatment |
Adheres well to powder-coated surfaces. To improve adhesion on plastic |
In addition to the reference products, we develop material systems according to your individual requirements. Influencing factors include pot life until start of foaming, curing time, and the viscosity, hardness and adhesion properties.
Repeated opening and reclosing of the battery housing with constant sealing effect
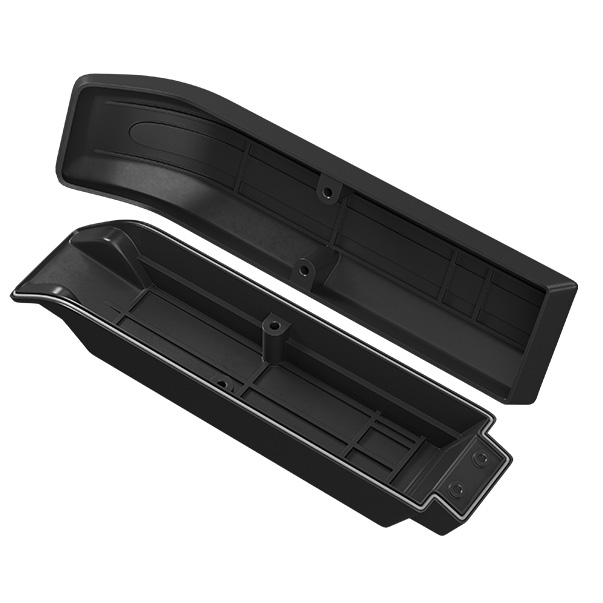
Thanks to the mixed-cell foam structure, the closing forces when installing the foam gasket are low.
Due to its excellent shape recovery characteristics, the mixed-cell foam structure of the polyurethane seal can still be compressed well even after years (tested according to DIN EN ISO 1856). It is therefore possible to repeatedly open and close the battery housing for battery changes, and the sealing effect of the foam gasket remains consistent.
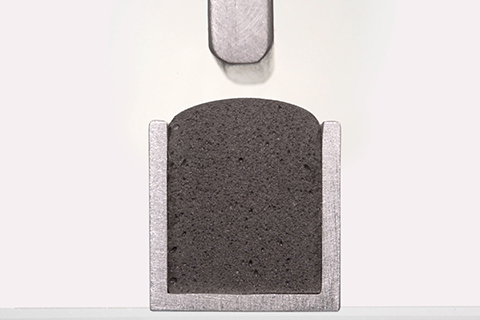
Cross-section of a polyurethane foam bead in the groove without compression
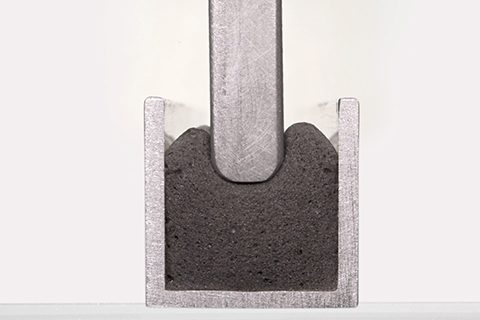
Cross-section of a polyurethane foam bead
in the groove and compressed to approx. 50 %
Mixing and dosing system with 6-axis robot and shuttle table for sealing battery housings with sealing foam
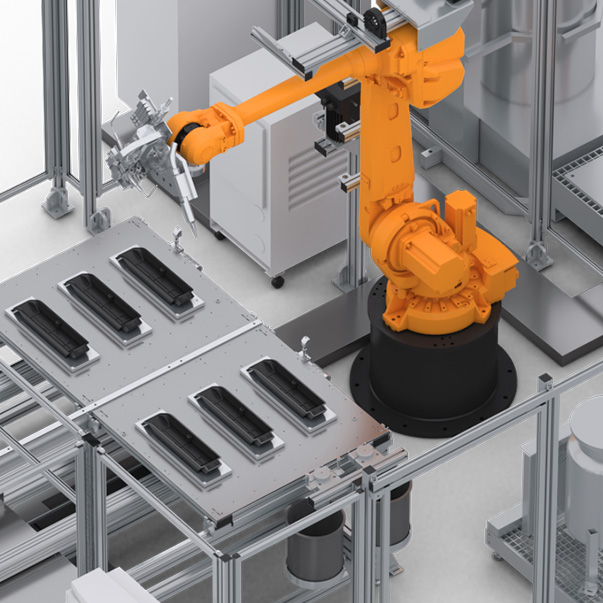
Flexible and fully automatic – fully in line with your requirements
The reference configuration shown here for sealing the battery housings of e-bikes and e-scooters consists of the DM 502 mixing and dosing system and the MK 825 PRO precision mixing head, as well as a 6-axis robot and the WT 1-LEVEL shuttle table.
Parts are picked up and processed here in continuous shuttle mode, operating in a single plane. The battery housing to be sealed is positioned and fixed in place on the shuttle table, either by a machine operator who can also check the parts for quality, or alternatively by a Pick & Place Robot. In the latter case, an optionally installed camera or sensor system could carry out the quality control of the parts.
The precision-contour, robot-controlled Formed-In-Place-Foam-Gasket (FIPFG) application process is crucial in precisely applying sealing foams into the housing groove of the battery housing. The 6-axis robot used ensures repeatable accuracy in guiding the robot arm’s MK 825 PRO precision mixing head over the component. In this process, the 2-component polyurethane sealing foam is applied very precisely into the groove of the two or three- dimensional battery housing.
After the dosing cycle, the coupling point of the room-temperature curing foam gasket closes seamlessly, and is thus almost invisible. Even with short cycle times and high unit numbers, the material application process using the FIPFG method is carried out with high dosing precision and repeat accuracy.
As a result, you achieve foam gaskets of uniformly high quality. During final assembly of the battery housing, the foam gasket applied is evenly compressed over the entire housing contour, and once installed will result in a high degree of tightness compliant with IP protection classes. It compensates for component tolerances when sealing, and has a very high temperature resistance from -40 to +80 °C.
In addition, our fail-safe mixing and dosing system can be operated easily and intuitively without the need for extensive training. Thanks to the automatic logging of dosing program data, all process data can be traced and evaluated by the machine operator via the CONTROL 2 operating panel while production is running. In all solutions, our main focus is on extremely reliable plant engineering, minimized maintenance times and consistent dosing quality.
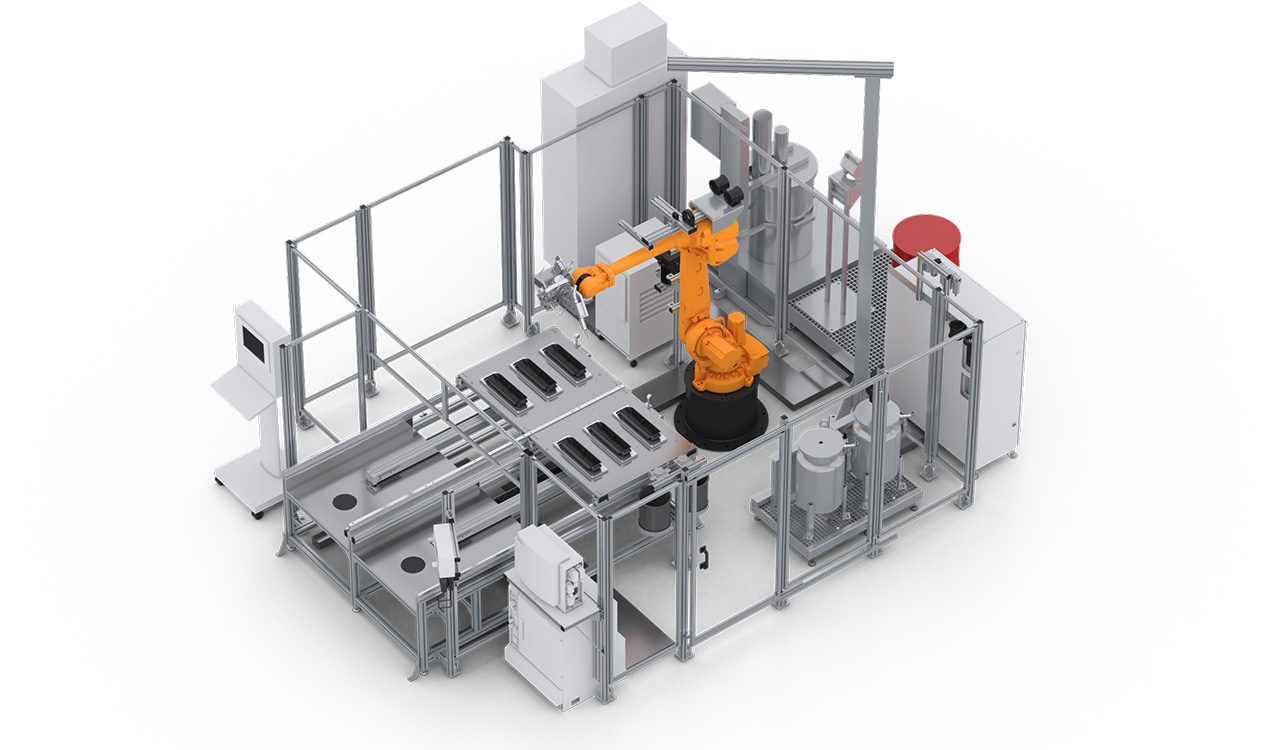
CONTROL 2
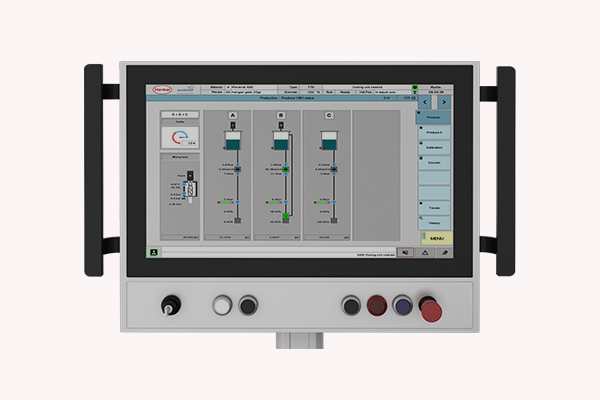
Optionally available: CONTROL touchscreen operating panel (21.5“) for operating the dosing system
More information to our operating panelsWT 1-LEVEL shuttle / sliding table
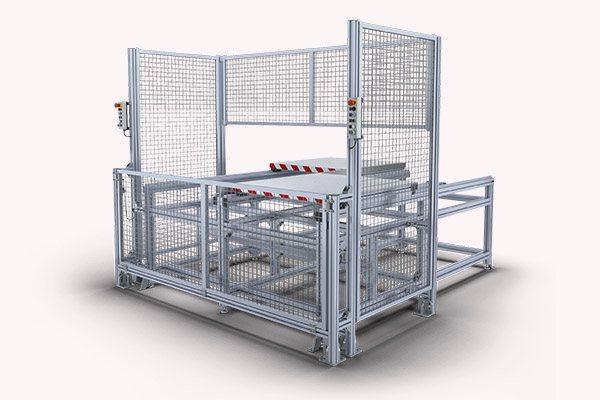
Two pick-up plates operating in pendulum mode in one plane
More information to our shuttle tablesMixing head 825 PRO
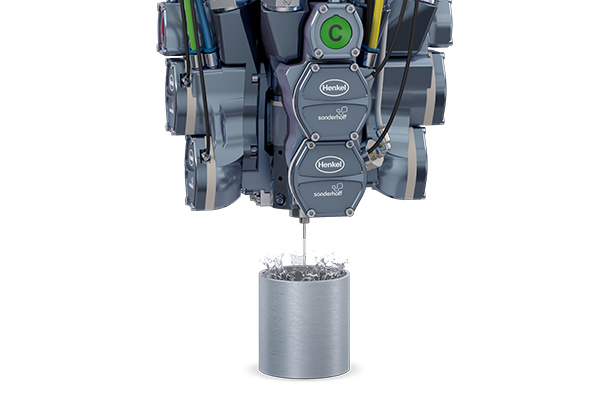
MK 800 PRO precision mixing head with high-pressure water rinsing or alternative component rinsing system
More information to our mixing headsMaterial pressure tanks
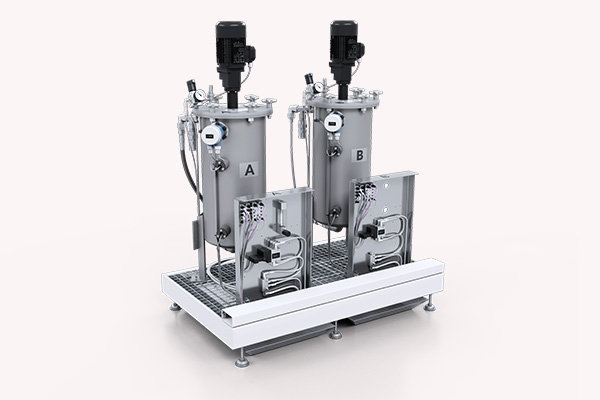
Material pressure tanks (24 l or 44 l, single-walled or double-walled) with minimum level sensors, on a grating platform with adjustable leveling feet and drip tray
More information to our material Pressure TanksControl cabinet
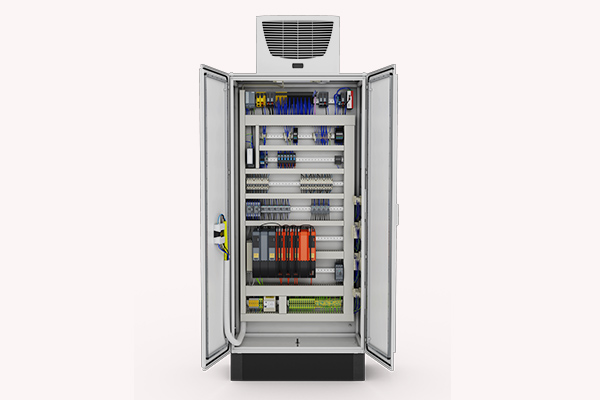
The control electronics, safety engineering and industrial PC are installed in the control cabinet.
More information to our control cabinetsDosing machine cabinet
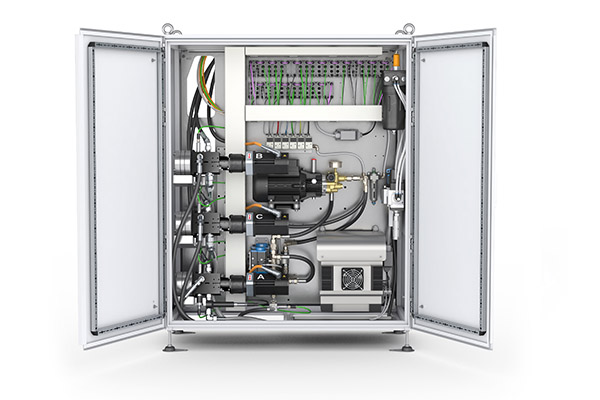
The dosing machine cabinet contains the components of the dosing periphery, e.g. the dosing pumps.
More information to our dosing machine cabinetsElevator
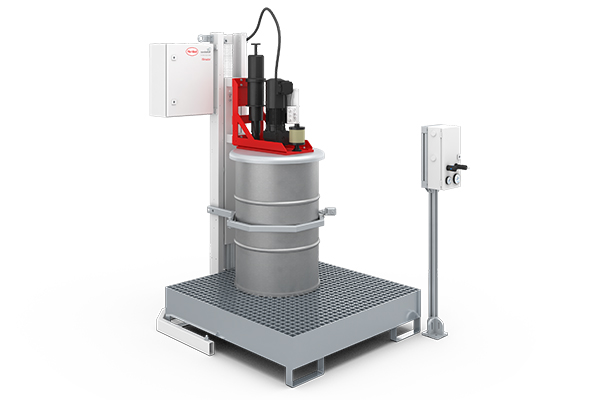
Optional: Automatic ELEVATOR drum refilling station for the A-component with pneumatic lift and agitator
More information to our refilling stationsSupply Tap
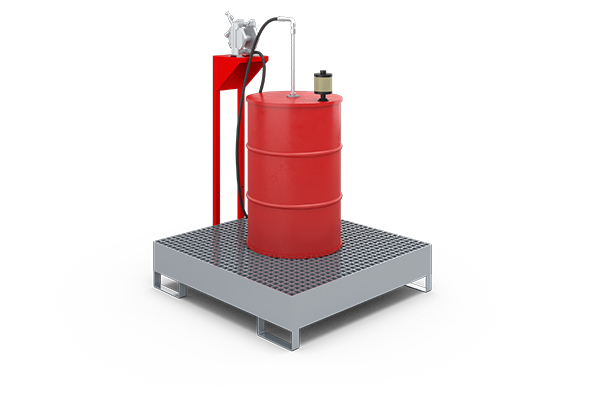
Optional: Automatic SUPPLY TAP drum refilling station for low-viscosity products, e.g. isocyanate (B-component)
More information to our refilling stations