The plastics industry is doing well, the industry's willingness to invest in new machinery remains high, and the Fakuma trade fair is continuing to grow, the media unanimously reported. Sonderhoff also wants to profit from this and presents the advantages of the new FIP CC technology at booth A5 5109 at the Fakuma from 16 to 20 October 2018. FIP CC combines the high resistance of the silicone world and the attractive material costs of the polyurethane world.
The DM 402 CC mixing and dosing system developed for the new FIP CC foaming process will be demonstrated live at the Sonderhoff stand. It is used to meter the very fine-cell, predominantly closed-cell PU soft foam seals Fermapor CC. With a slightly glossy surface, they also make a very high-quality impression visually. At the trade fair stand, Sonderhoff will also demonstrate the low water absorption of the CC foam seal with an endurance test for water resistance.
The FERMAPOR CC foam seals are room temperature curing 2-component PU-based systems that cure without oven or moisture. They represent a significantly less expensive alternative to 1-component and silicone applications. Unlike comparable mixed-cell seals, the CC foam seal requires less compression with the same sealing performance. A robust, mounting-resistant surface of the CC foam seal withstands possible mechanical stresses in the parts handling. Even after damage to the surface, such as tears, the water absorption changes only slightly. The polyurethane-based Fermapor CC foam gaskets are very weatherproof and even ice water resistant at water temperatures up to 1 °C.
Fermapor CC PU foam complies with REACH / EC regulation 1907/2006 and RoHS and is generally used for sealing components at temperatures from -40 °C to +80 °C, for short periods even up to +160 °C.
The FIP CC application process with the new dosing system DM 402 CC follows the well-known FIPFG process (Formed-In-Place Foam Gasket), which is the production standard for component sealing in many industrial sectors. What is new is that already with the metering, the CC foam is applied stable to the component contour in an almost complete sealing dimension by physical foaming. As a result, the user can check immediately after applying the seal whether the seal has been applied at the same height over the entire component contour. That's why FERMAPOR CC is particularly suitable for 3D applications and process-oriented quality control.
In addition, foam density and hardness can be adjusted in the current process via the machine parameters. The DM 402 CC has a much shorter set-up time, because the classic air loading via the storage containers is eliminated. The change of material is easier, because no material circulation is necessary for the CC foaming process. This simplifies and speeds up potential process adjustments.
Due to the increased efficiency of the FIP CC technology, automated seal foaming opens up new fields of application.
High tightness due to low water absorption of the closed-cell PU foam seal
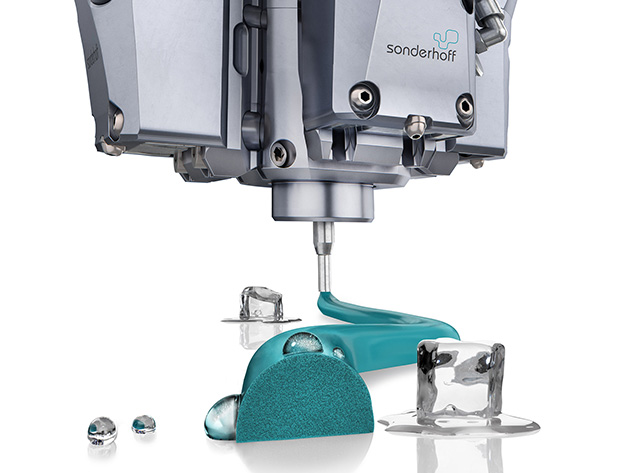
The machine and sealing specialist Sonderhoff, part of Henkel AG & Co. KGaA since July 2017, will be focusing on the FIP CC technology (Formed-In-Place Closed-Cell) successfully introduced last year at the Fakuma 2018. The special highlight of the new physical foaming process: Already with the metering, the CC foam is stable in almost complete sealing dimension applied to the part contour. The new predominantly closed cell foam seal Fermapor CC based on PU has been developed by Sonderhoff especially for applications with high demands on water resistance. The seal cures without oven or moisture and closes the gap between the more expensive silicone foams and the cheaper mixed-cell PU foam seals.