Customized sealing foams
for maximum packaging safety of metal drum lids
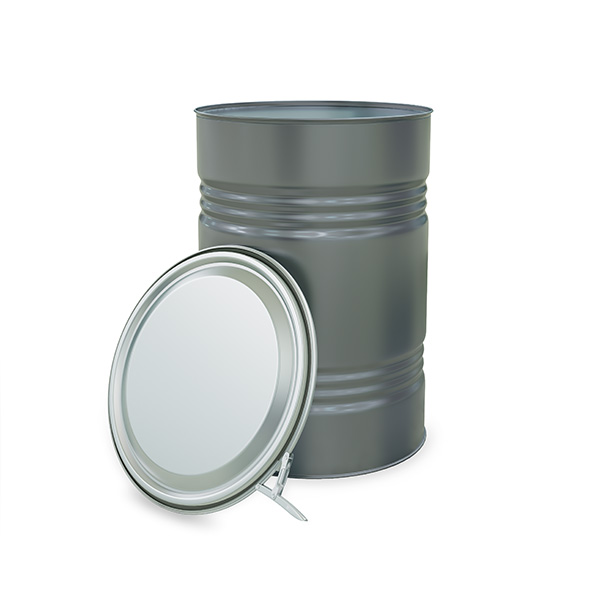
With its Sonderhoff brand, Henkel has acquired many years of experience in the manufacture of 2-component sealing systems and the accompanying mixing and dosing machines. We are recognized as experts when it comes to applying material using Formed-In- Place-Foam-Gasket (FIPFG) technology to seal lidded containers.
The requirements for lidded drums made of blackplate, tinplate and steel are as varied as their contents. For sealing the drum lids, we offer FERMAPOR K31 polyurethane sealing foams, which provide perfect protection against leakage or contamination of packaged goods as part of the overall design of the container. The drums are therefore leak-proof in accordance with UN approval, even in the event of drops, impacts or vibrations.
Provided that the container design is suitable for the transport of hazardous goods, the special formulations of FERMAPOR K31 polyurethane sealing foams also meet the sealing requirements of the UN hazardous goods approval.
Frequent opening and closing of the drums with a constant sealing effect

When the drum lid is closed, the elastic cell structure of the gasket is compressed and the housing is sealed.
The excellent resetting ability of the foam gasket allows repeated opening and re-closing of the drum lid without any loss of sealing performance.
Animation of sealing of steel drum lids with Sonderhoff DM 502 and conveyor belt for feeding parts
Material systems for drum lids made of metal

Our reference material FERMAPOR K31-A-6501-4-N / K31-B-5 is used for sealing the lids of metal drums for industrial products such as paints, varnishes, construction materials and aggregates. Pretreatment with plasma or primer is usually carried out for even better adhesion.
FERMAPOR K31-A-6505-1-N-FD / K31-B-28-FD meets the requirements of a lid gasket for the packaging of foodstuffs in metal drums.
This formula has been tested for safe use in direct contact with liquid, alcoholic, fatty and dry foodstuffs in accordance with the European standard EU 10/2011 and the German LFGB (according to §§30 and 31 para. 1 of the German Food and Feed Act).
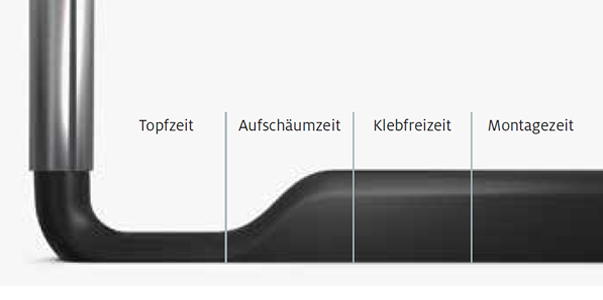
The different reaction phases of the sealing foam in the chronological sequence
Reference material
Metal drums |
Metal drums for food products |
|||
FERMAPOR K31 | A-6501-4-N | A-6505-1-N -FD | ||
B-5 | B-28-FD | |||
Mixing ratio |
4.4 : 1 | 3.05 : 1 | ||
Pot life |
60 Sek. | 35 Sek. | ||
Tack-free time |
7 Min. | 8 Min. | ||
Viscosity of the A component |
1,250 mPas | 6,200 mPas | ||
Density |
0.42 g/cm³ | 0.28 g/cm³ | ||
Hardness (Shore 00) |
67 | 80 | ||
Temperature resistance |
from -40 to + 80 °C | from -40 to + 80 °C | ||
Pretreatment |
Plasma or Primer | Plasma or Primer |
In addition to the reference products, we develop material systems according to your individual requirements. The influencing factors include the pot life until the start of foam formation, the curing time as well as the viscosity, the hardness and the adhesion properties.
Compression behavior
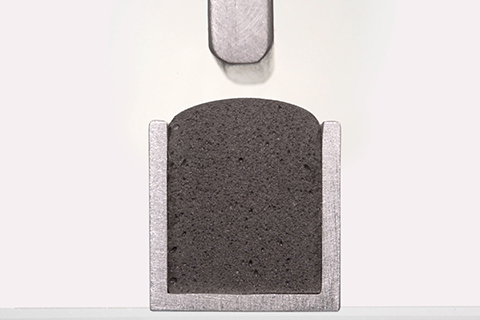
Cross-section of a polyurethane foam bead in groove uncompressed
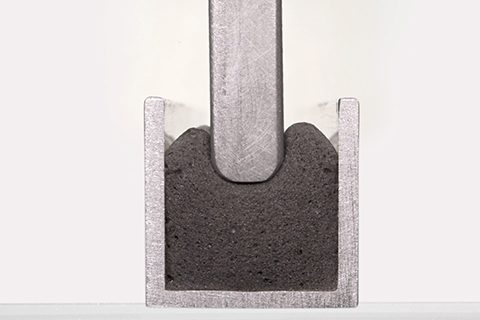
Cross-section of a polyurethane foam bead in the groove and compressed to approx. 50 %
Mixing and dosing system DM 502 with 3-axis linear robot and conveyor belt for feeding parts
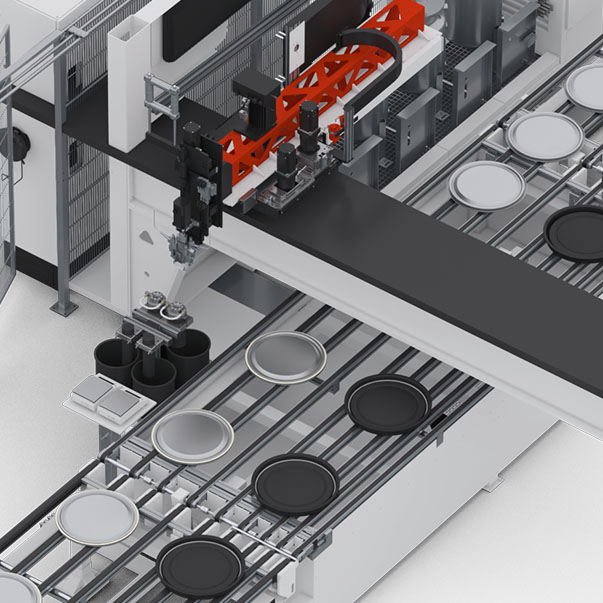
Flexible and fully automatic –
according to your requirements
As a process expert, we offer economical and efficient solutions for the customized automation and integration of our mixing and dosing systems into your production processes.
The reference configuration shown here is used for the fully automatic and contour-accurate application of 2-component sealing foams into the groove of the lids of metal or plastic drums. It consists of the DM 502 mixing and dosing system with a 3-axis linear robot and a conveyor belt system for feeding parts and clocking out.
The drum lids are fed to the dosing station at the cycle rate specified for your production, where they pass under the 3-axis linear robot. At the centering station, the lid is positioned on the belt in such a way that the mixing head controlled by the linear robot can move along the lid groove with contour accuracy and apply the precisely dosed discharge quantity into the groove.
Alternatively, the sealing foam can also be dispensed into the groove by rotating the lid. The discharge quantity is fed into the groove of the lid via the mixing head in relation to the rotational speed.
With the high quantities and short cycle times in drum lid production, our dosing machines with FIPFG technology enable efficient and precise material application. The highly dynamic LR-HD or alternatively the highly efficient 3-axis linear robot LR-HE plus ensures precise contour guidance of the MK 825 PRO precision mixing head over the contour of the lid.
Both application variants apply the sealing foam into the lid groove with high dosing and repetition accuracy. The coupling point of the foam gasket closes seamlessly and is therefore almost invisible. After expanding by several times the specified material volume, a soft foam gasket with the desired foam hardness is produced and cures at room temperature.
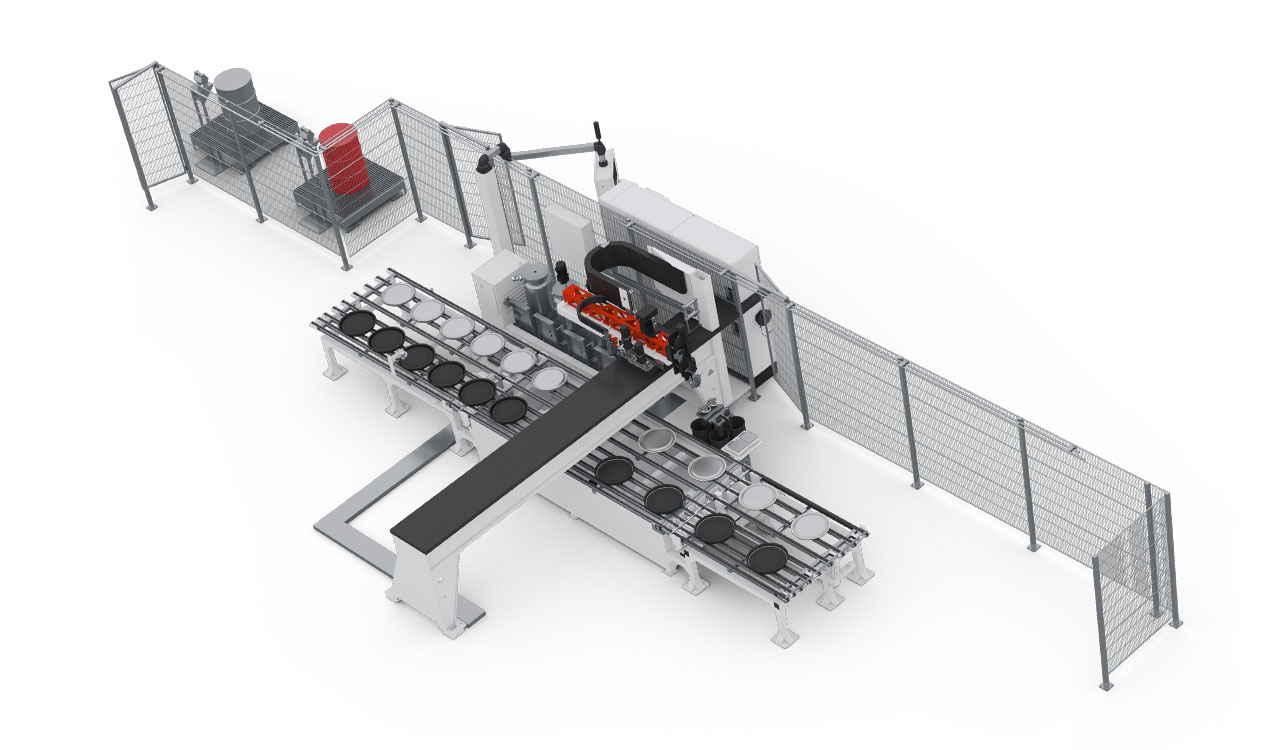
Elevator
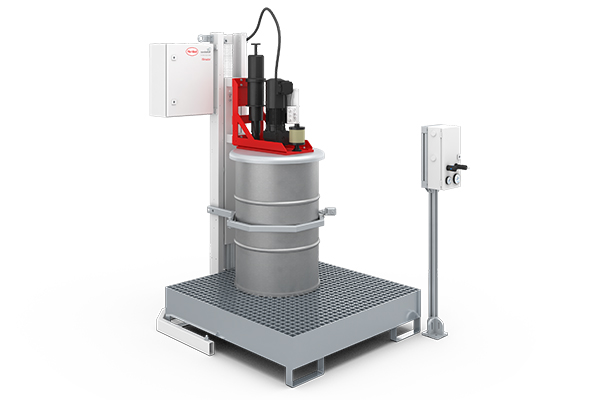
Optional: Automatic ELEVATOR drum refilling station for the A-component with pneumatic lift and agitator
More information to our refilling stationsSupply Tap
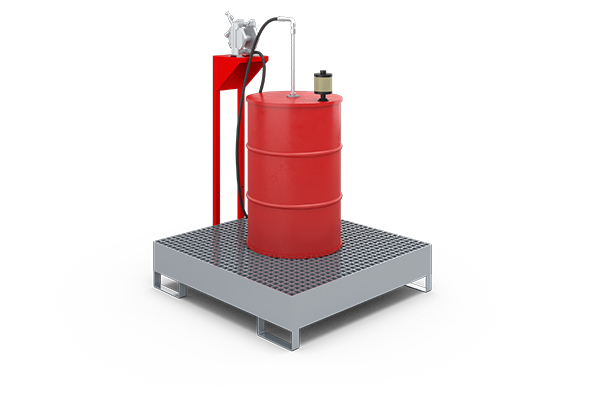
Optional: Automatic SUPPLY TAP drum refilling station for low-viscosity products, e.g. isocyanate (B-component)
More information to our refilling stationsMaterial pressure tanks
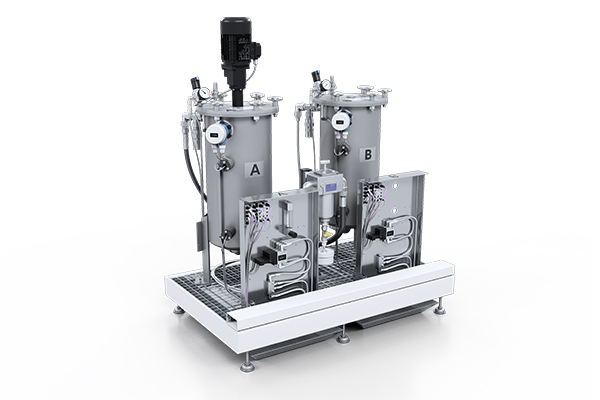
Material pressure tanks (24 l or 44 l, single-walled or double-walled) with minimum level sensors, on a grating platform with adjustable leveling feet and drip tray
More information to our material Pressure TanksCONTROL 2
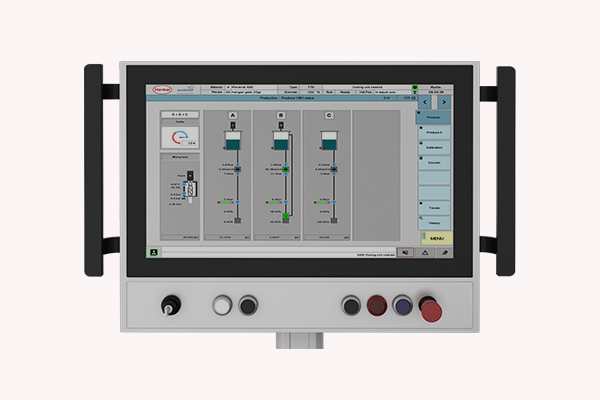
Optionally available: CONTROL touchscreen operating panel (21.5“) for operating the dosing system
More information to our operating panelsDosing machine cabinet
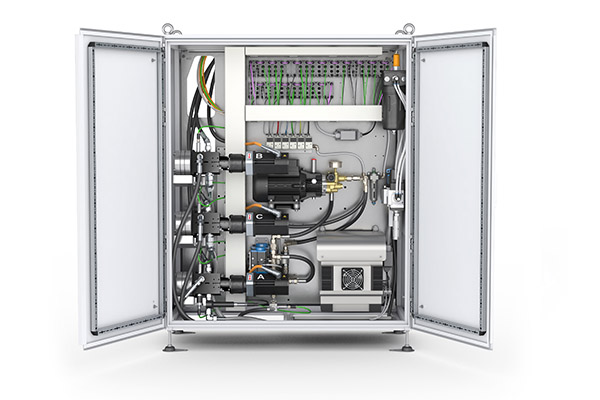
The dosing machine cabinet contains the components of the dosing periphery, e.g. the dosing pumps.
More information to our dosing machine cabinetsControl cabinet
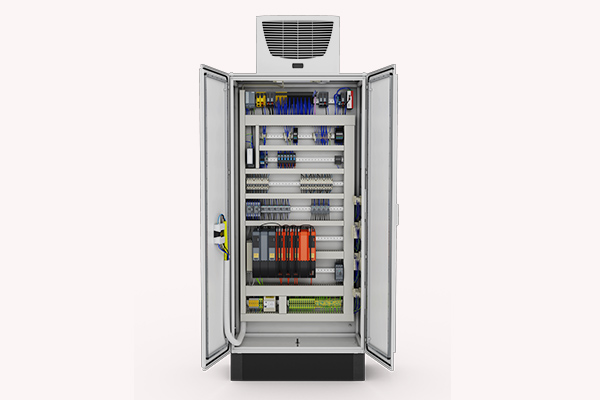
The control electronics, safety engineering and industrial PC are installed in the control cabinet.
More information to our control cabinetsMischkopf 825 PRO
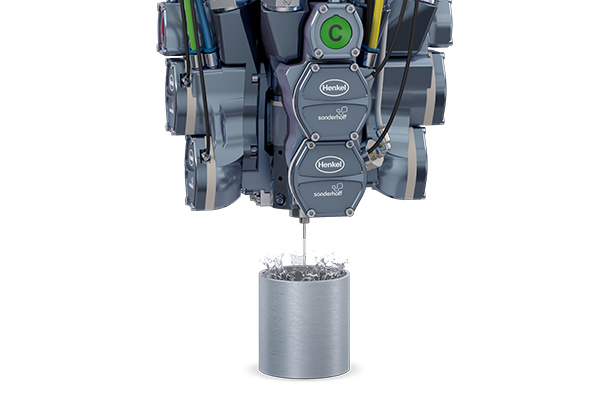
MK 800 PRO precision mixing head with high-pressure water rinsing or alternative component rinsing system
More information to our mixing headsMP 2 Mobilpanel
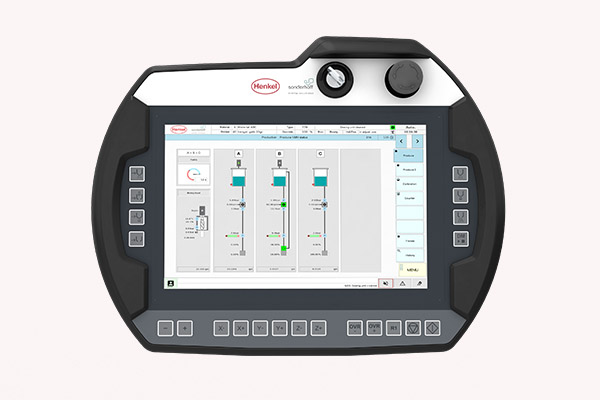
The multifunctional MP 2 mobile panel (10.1” WXGA TFT) enables convenient operation of the dosing system.
More information to our operating panels