Bonding of Automotive Displays
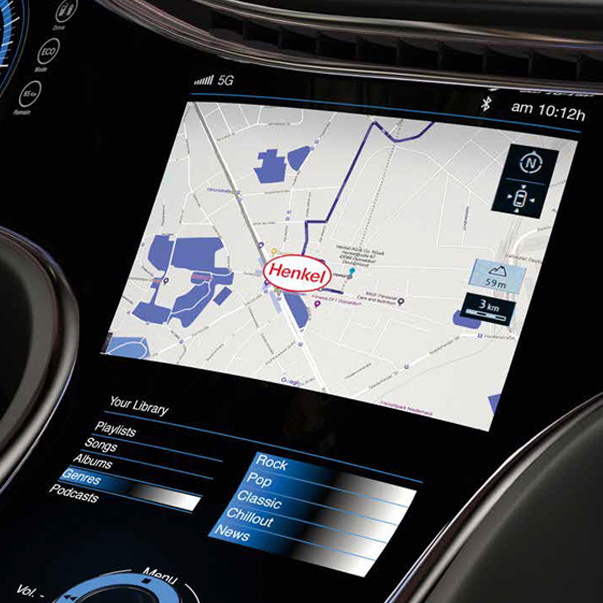
The digitization of the car for modern mobility requires interfaces that offer a more individualized and interactive approach to road users. With increased development of self-driving vehicles, multidimensional infotainment and safety functions are required to accommodate networking. In addition to creating a comfortable cockpit environment, automotive displays support driver safety by providing up-to-date information about traffic events and car functionality.
Automotive infotainment systems provide audio or video entertainment for all occupants via their displays. Advanced driver-assistance systems (ADAS) provide graphical visualization of driver information such as parking assistance, navigation, traffic assistance, control functions and internet connectivity. All setting options in the car can be operated via touch displays.
Freeform and curved automotive displays are the future, enabling larger and more attractive dashboard displays. Housing designs are evolving to better utilize interior space and accommodate these larger and more responsive screens.
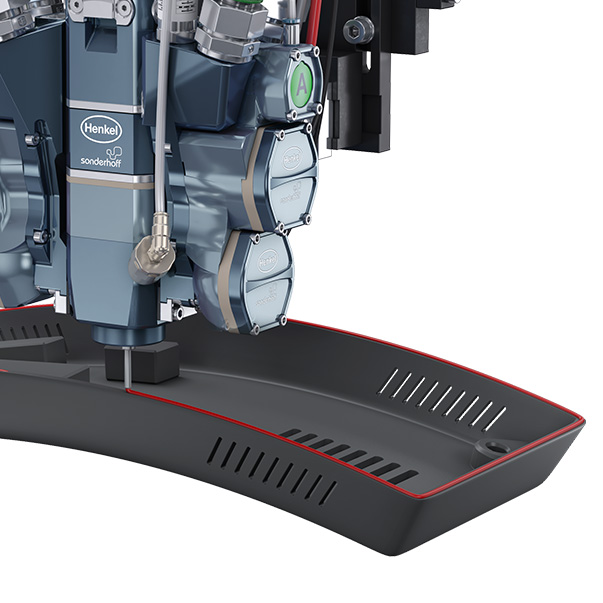
Our solutions for structural bonding of automotive displays meet the needs of market trends, such as the increasing demand for design flexibility. High-precision metering with Henkel’s fully automatic mixing and dosing systems ensure high contour accuracy during adhesive application.
How do you ensure perfect display bonding when cost and design considerations are increasingly narrowing the bonding surfaces of the display housing?
What can you do to compensate for component tolerances during adhesive application, so as to achieve an adhesive bead of uniform width after joining?
We provide the solution for you, with Active Quantity Adjustment (AQA). This method makes it possible to adapt the dosing quantity during application of the adhesive to the part contour. This compensates for production-related differences and irregularities in the bonding surfaces as well as applies a precisely calculated and accurately metered quantity of adhesive. To achieve this, a 3D line scanner measures the part geometry and compares the data with the previously defined CAD reference of the part before the adhesive is dispensed. The result after joining is an adhesive seam that is consistent in height and width.
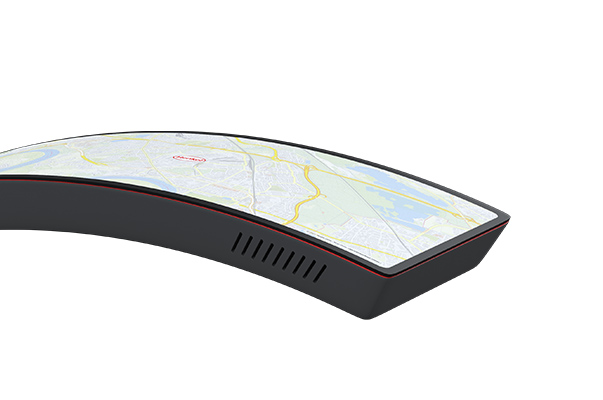
The trend towards larger displays in vehicles, combined with the need for space-saving installation, has led to narrow-edged display solutions. The challenge is to still achieve strong adhesive bonding with narrow bonding surfaces and thus thin bonding lines.
The adhesive must not protrude at the edges once joining the display to the housing. Fully automatic adhesive application and tolerance compensation are handled by Henkel’s mixing and dosing systems.
Brand new animation of the AQA (Active Quantity Adjustment) process for display bonding with LOCTITE MS 650 using a Sonderhoff dispensing machine. The process steps from injection molding, the vision scanner, bonding and joining with and without the AQA process are shown to illustrate the differences and advantages.
Animation of System Solution for Display Bonding with LOCTITE MS 650 using a Sonderhoff Dosing Machine / AQA Process
Precise bonding on narrow adhesive surfaces
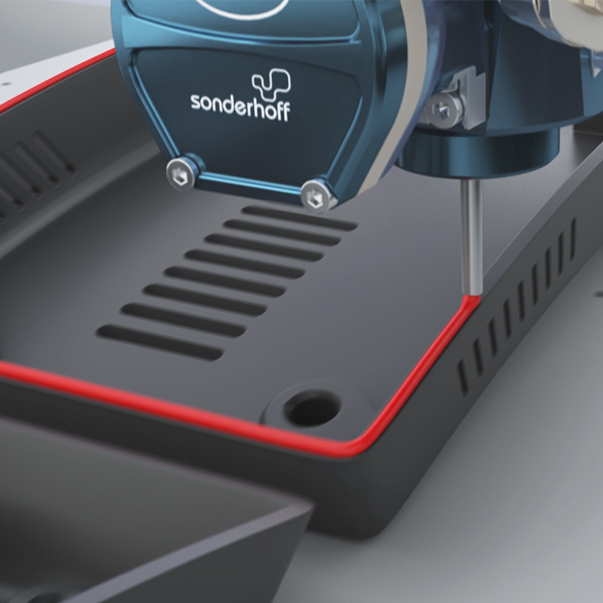
LOCTITE® MS 650 – Polymer adhesive for elastic structural bonding with high initial strength
Free-form and curved designs of automotive displays dominate the interior of modern cars and are fully integrated into the overall interior design. The design and manufacture of automotive displays require a variety of materials, ranging from ensuring the strength of the display housing structure to bonding the cover glass to the TFT / LCD display.
To bond the automotive display to the housing, LOCTITE® MS 650, a thixotropic silane-modified polymer adhesive, is used for elastic structural bonding of medium to high strength. This can be used to create multi-substrate bonds such as plastic to plastic, plastic to glass, and glass to glass for free-form and curved design displays.
LOCTITE® MS 650 is available as a 1-component adhesive for moisture cure or as a 2-component adhesive for accelerated, ultra-fast cure. They offer high green strength and fast skin formation. Due to very fast curing properties, the 2K adhesive achieves high initial strength at room temperature shortly after joining the components.
The 2K adhesives based on MS polymers used for display bonding are mixed dynamically and homogeneously in a specific mixing ratio using the Sonderhoff mixing and dosing machine and applied to the adhesive surface of the display housing fully automatially and very precisely by the Formed-In-Place technology.
Reference Material
LOCTITE MS 650 2C | |
Mixing Ratio, by weight | 10 : 1 |
Open time (DIN 50014 standard climate) | approx. 4-5 min. |
Handling stability | approx. 9-12 min. |
Tack-free time | approx. 2-10 min. |
Viscosity A-Component | approx. 180-330 pa.s |
Viscosity B-Component | approx. 150 pa.s |
Density | approx. 1.4 g/cm³ |
Shore-A hardness | approx. 55 |
Service temperature | from -40 to +90 °C (short exposure/up to 1 h: 120 °C) |
Application temperature | 15 to 40 °C |
Curing | Cure at ambient temperature (above 5 °C) or cure at elevated temperatures |
Technical data sheet of LOCTITE MS 650 2C
Sonderhoff solutions for Display Bonding under magnifying glass
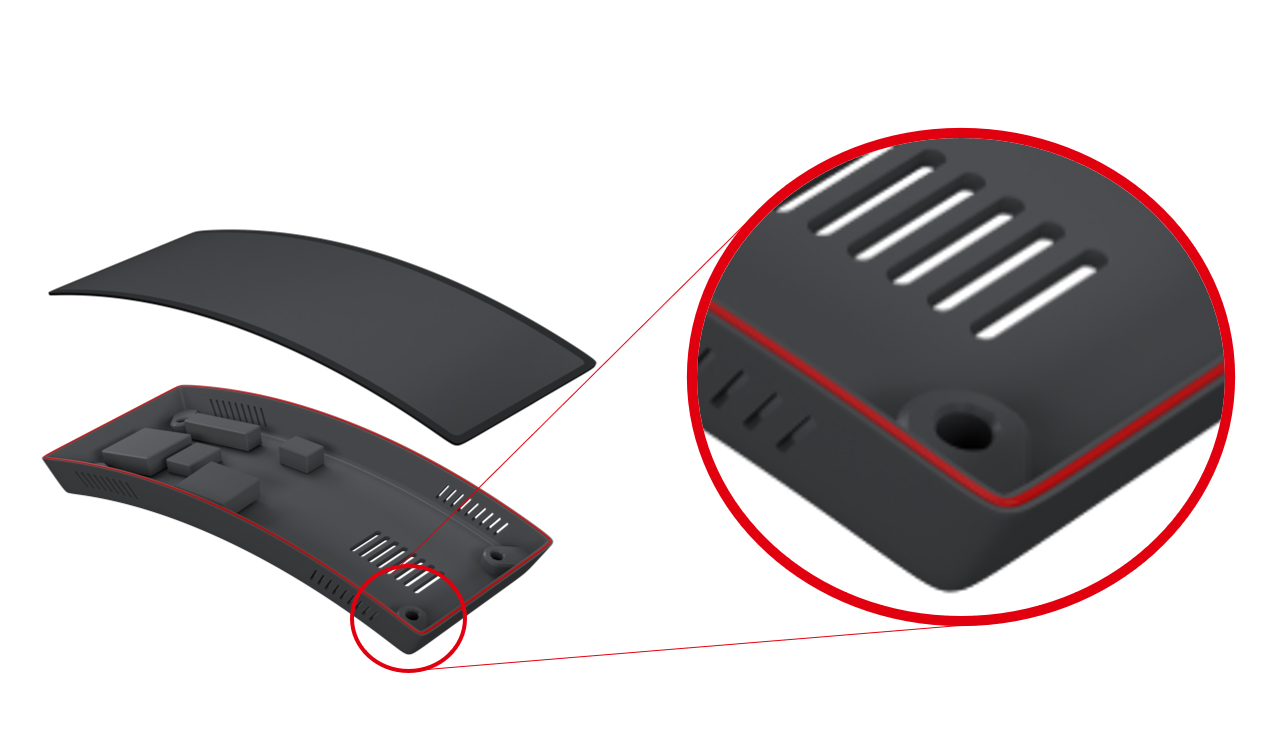
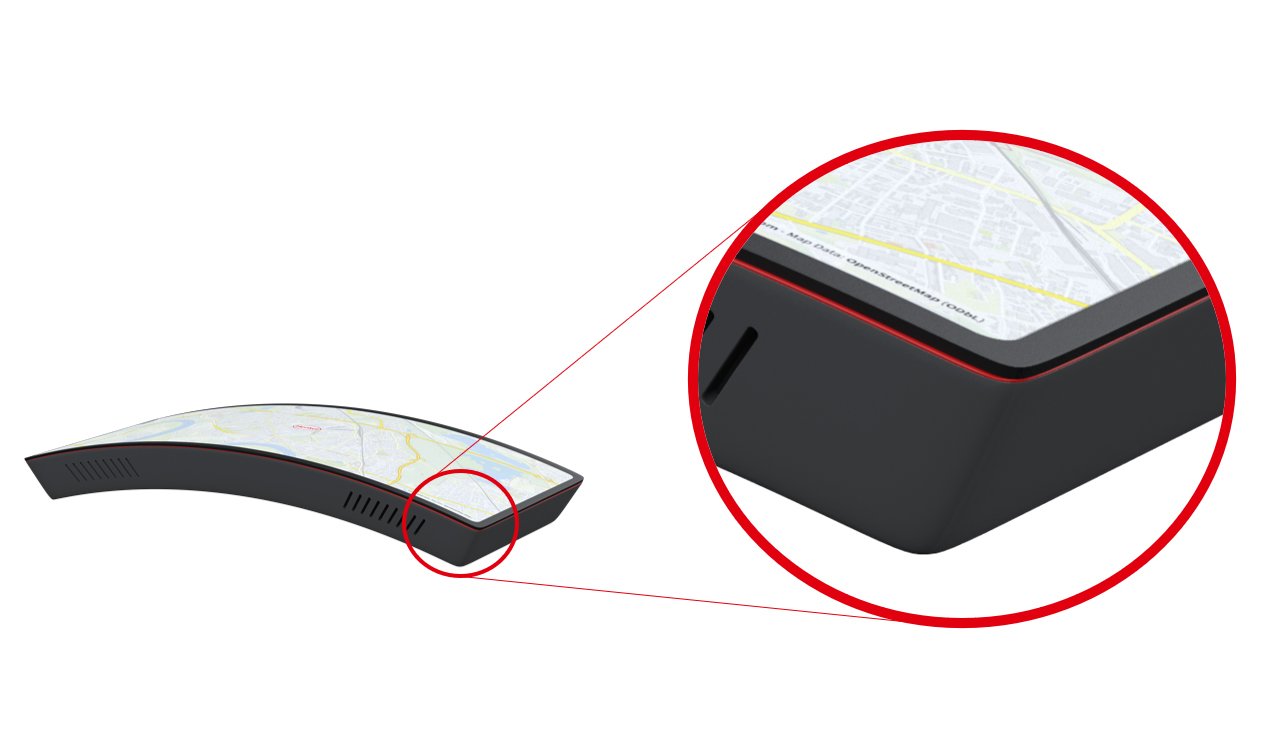
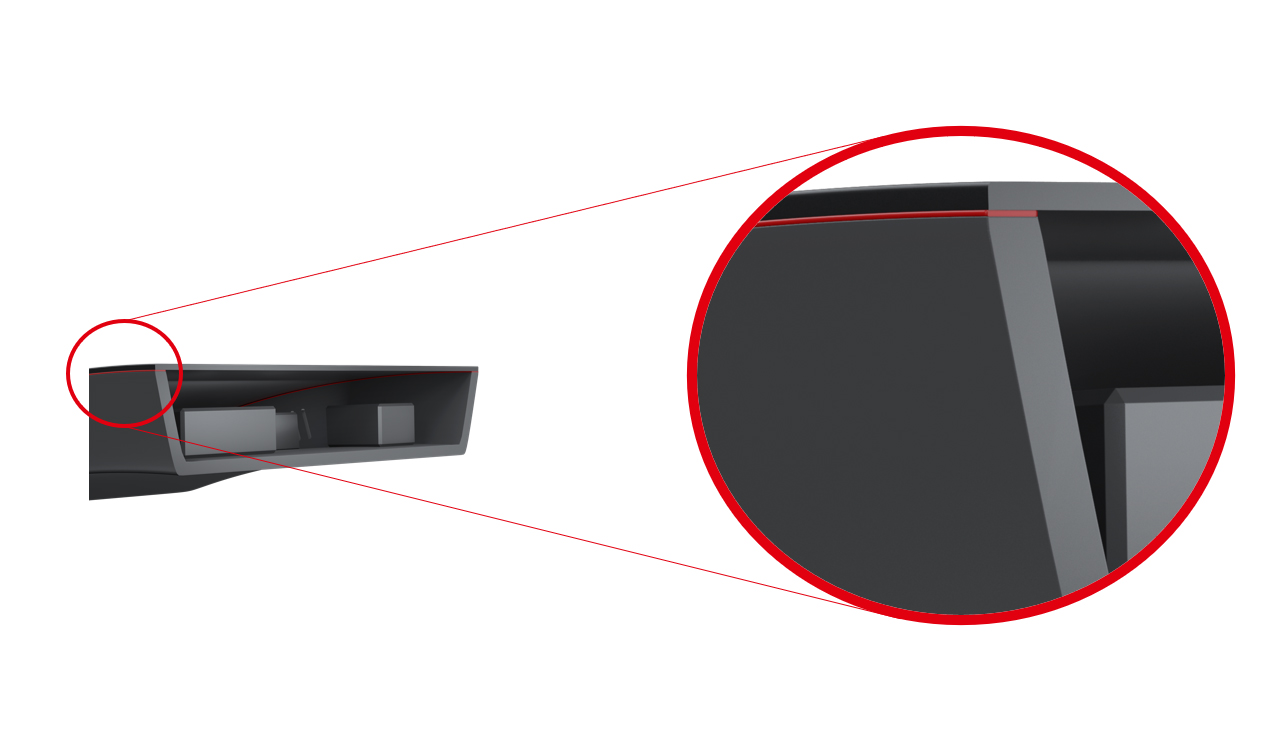
Flexibly adjustable dosing quantity for compensation of component tolerances
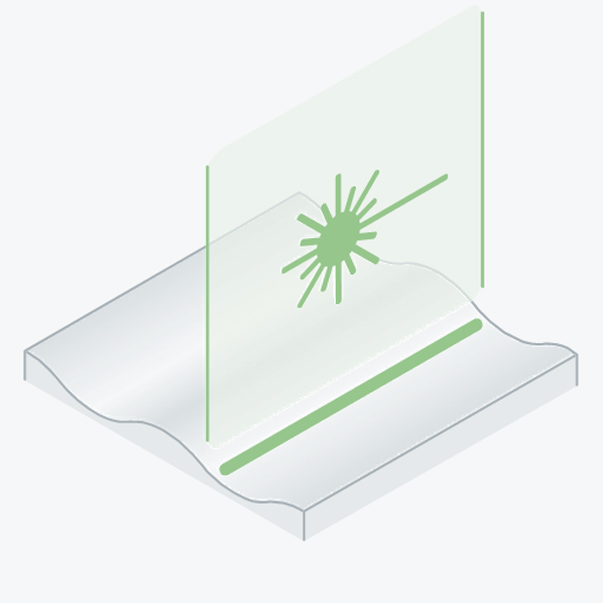
With the Active Quantity Adjustment (AQA) process developed by Henkel, it is possible to control the amount of adhesive dispensed for bonding displays to the housing. This ensures the correct quantity dosage at all times based on the respective height profile of the component. This method makes it possible to adapt the dosing quantity during application of the adhesive to the part contour. This compensates for production-related differences and irregularities in the bonding surfaces as well as applies a precisely calculated and accurately metered quantity of adhesive.
Before dispensing, a 3D line scanner scans the geometry of the components. The scanned data are transmitted to the dosing machine’s programmable logic controller (PLC) and compared with the predefined CAD reference of the component. Any deviations detected are used to adjust the dosing program in advance for the next adhesive application.
Wavy unevenness of the bonding surfaces can occur during the injection molding of the display housing. In order to compensate for this, the robot travels more slowly over slightly recessed application areas so that more adhesive is applied there, and travels faster over the slightly raised areas so that less adhesive is dispensed there.
The AQA process can compensate for differences in the dimensional tolerances of the component. With a target glue gap of 1 mm, the specified tolerance for pressing the glue line is +/- 0.5 mm when the display and frame are joined. Since cost and design factors are increasingly resulting in narrower display housing bonding edges, the AQA process ensures that the adhesive trace on the housing contour, despite possible dimensional tolerances, remains uniform after the display glass is attached.
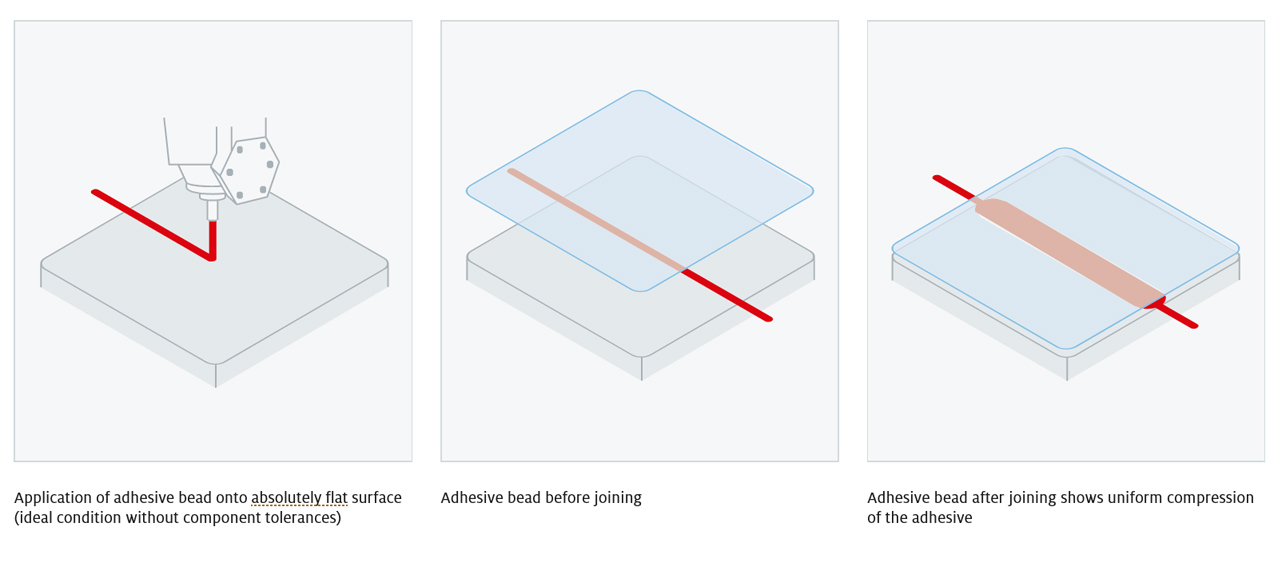
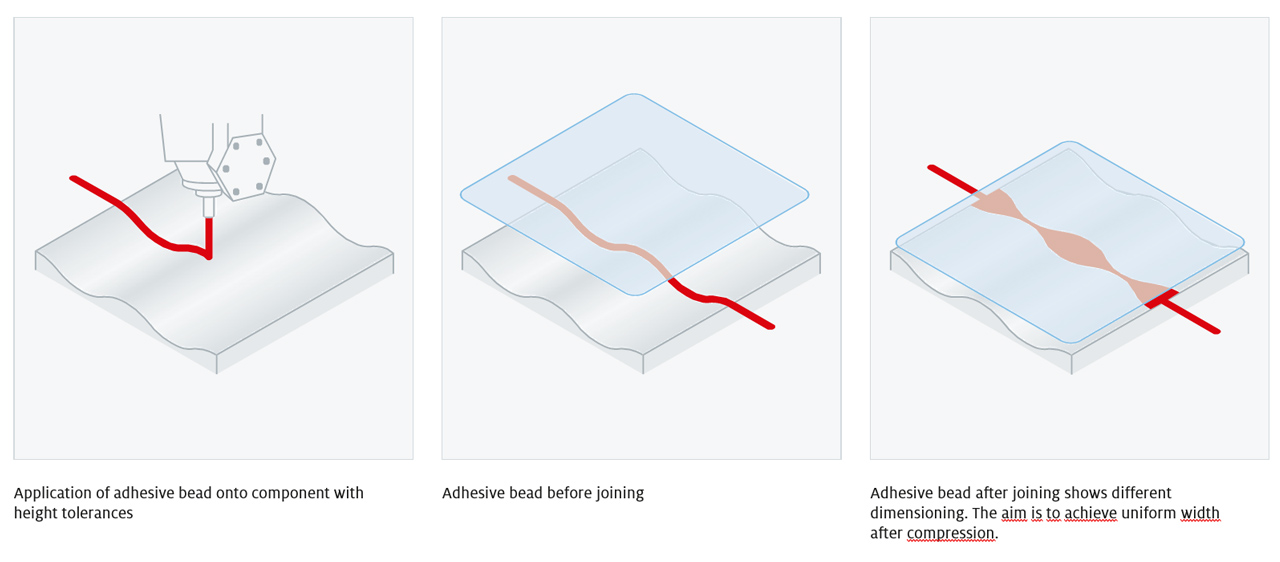
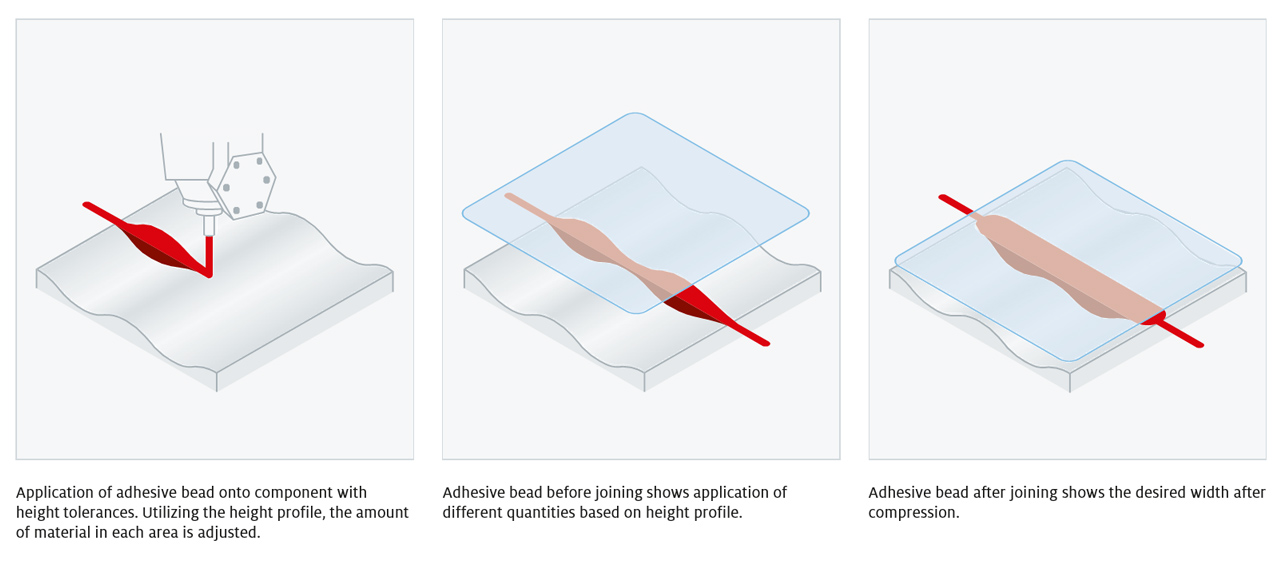
Mixing and dosing systems with 6-axis robot and shuttle table for bonding display housings
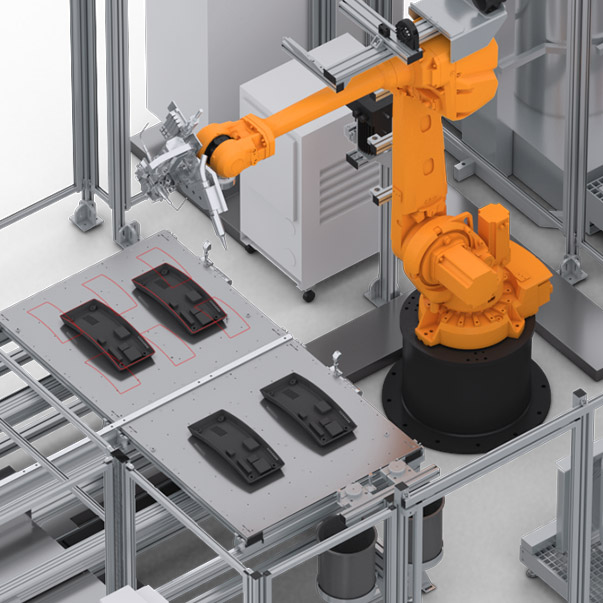
Efficient and fully automatic – to meet your exact requirements
In the reference configuration shown, the fully automatic adhesive application process for bonding the automotive displays to the housing is carried out using the DM 502 mixing and dosing machine with a 6-axis robot guiding the MK 825 PRO precision mixing head and using WT 1-LEVEL shuttle table for the parts handling. The display housings are attached to the two pick-up plates, and are positioned within range of the robot in shuttle mode utilizing a single plane.
This ensures a continuous adhesive application process. Depending on the plastic used for the display housing, it may be necessary to apply plasma to the contour of the display housing beforehand in order to achieve an improved adhesive effect. For this purpose, the robot can optionally be equipped with a plasma nozzle.
To measure and check part tolerances of the display housing, a separate pre-dispensing process step scans the surface of the housing using a 3D line scanner. The measured data are transmitted to the dosing system’s programmable logic controller (PLC) and compared with the predefined CAD reference of the component. The detected deviations are used to adjust the dosing program in advance for the next adhesive application.
The mixing head mounted on the robot arm moves over the contour of the display housing and applies a precise, narrow bead of adhesive to the contour. Thanks to the AQA process, it is possible to automatically adjust the adhesive discharge quantity to match the dimensional deviations of any component tolerances.
Wavy unevenness of the bonding surfaces can occur during the injection molding of the display housing. In order to compensate for this, the robot travels more slowly over slightly recessed application areas so that more adhesive is applied there, and travels faster over the slightly raised areas so that less adhesive is dispensed there.
The result is a bead of adhesive that compensates for the height tolerances and will remain consistent after the display glass is joined to the housing.
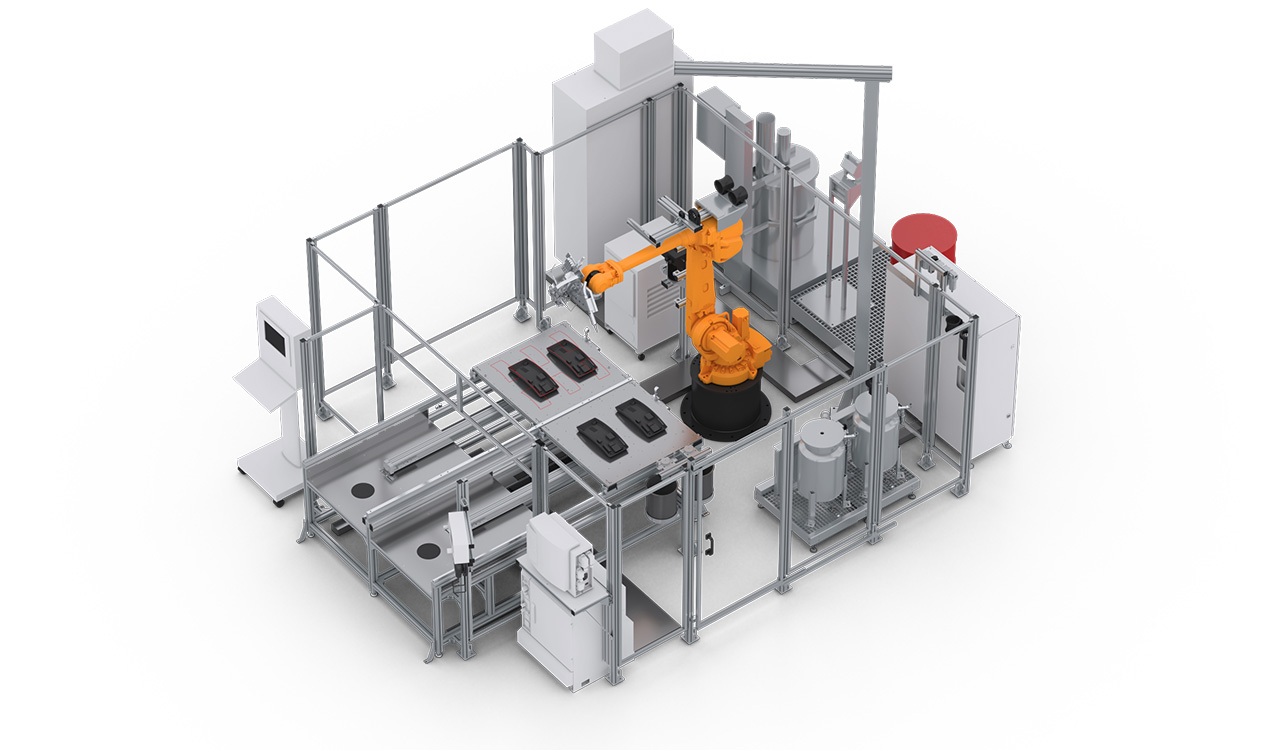
Supply Tap
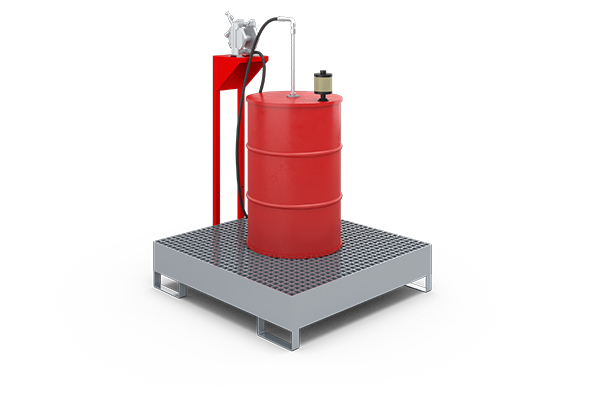
Optional: Automatic SUPPLY TAP drum refilling station for low-viscosity products, e.g. isocyanate (B-component)
More information to our refilling stationsElevator
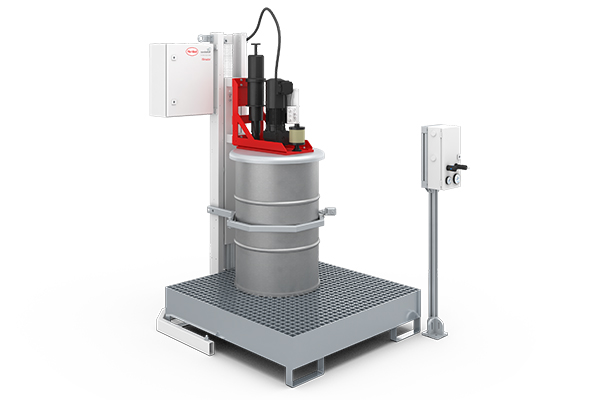
Optional: Automatic ELEVATOR drum refilling station for the A-component with pneumatic lift and agitator
More information to our refilling stationsControl cabinet
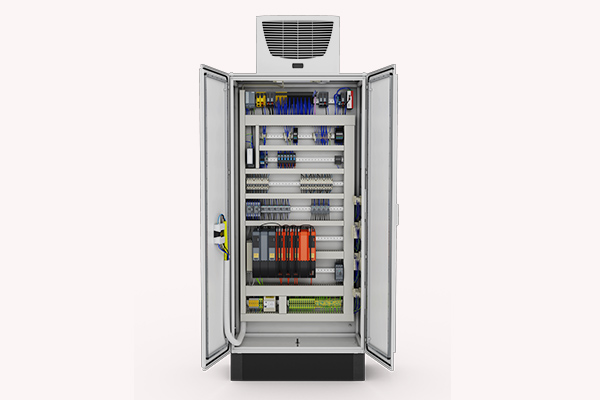
The control electronics, safety engineering and industrial PC are installed in the control cabinet.
More information to our control cabinetsMixing head 825 PRO
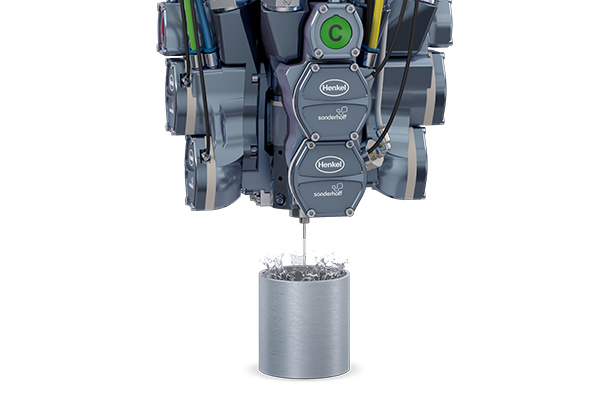
MK 800 PRO precision mixing head with high-pressure water rinsing or alternative component rinsing system
More information to our mixing headsWT 1-LEVEL shuttle / sliding table
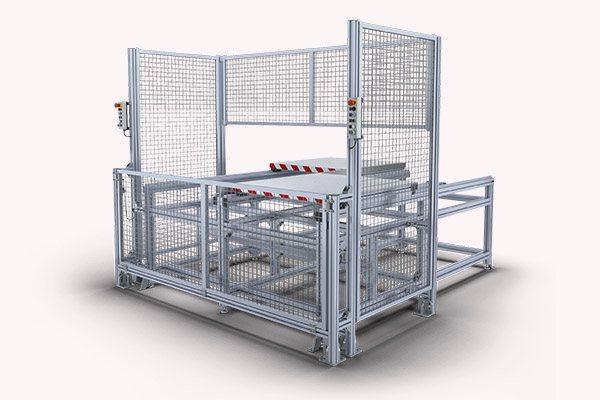
Two pick-up plates operating in pendulum mode in one plane
More information to our shuttle tablesCONTROL 2
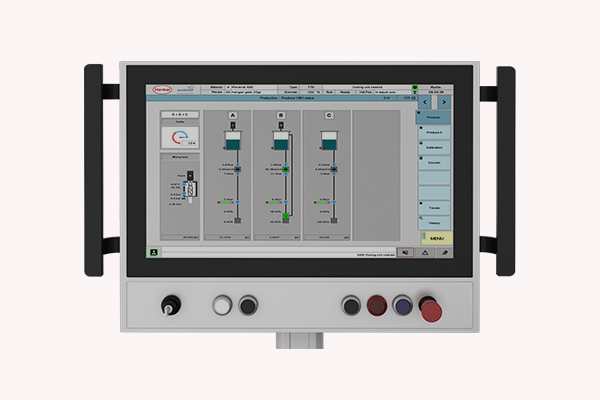
Optionally available: CONTROL touchscreen operating panel (21.5“) for operating the dosing system
More information to our operating panelsMP 2 mobile panel
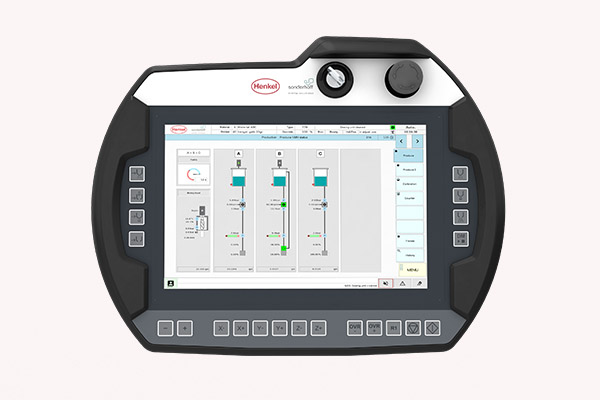
The multifunctional MP 2 mobile panel (10.1” WXGA TFT) enables convenient operation of the dosing system.
More information to our operating panelsMaterial pressure tanks
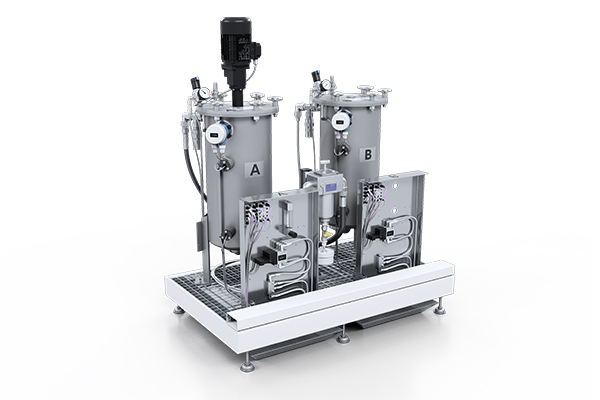
Material pressure tanks (24 l or 44 l, single-walled or double-walled) with minimum level sensors, on a grating platform with adjustable leveling feet
Read moreDosing machine cabinet
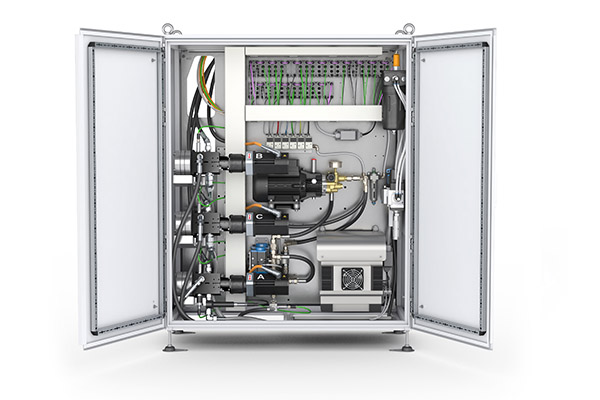
The dosing machine cabinet contains the components of the dosing periphery, e.g. the dosing pumps.
Read more