Optimal bonding of glass doors in microwaves
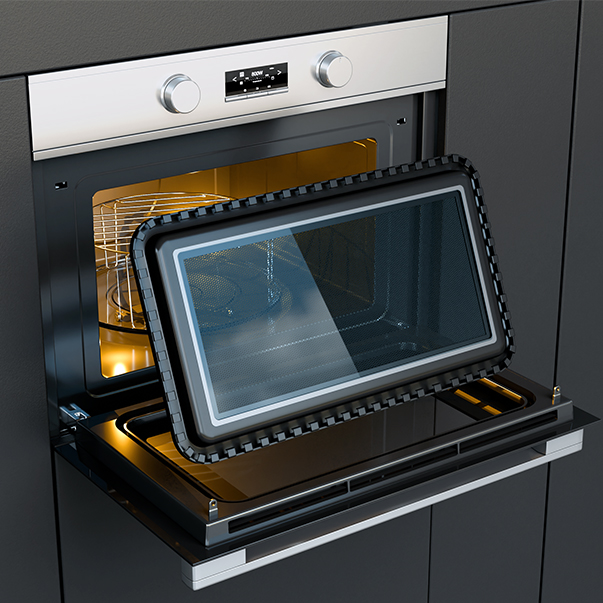
Microwaves have become indispensable in modern kitchens. The functionality and safety of these appliances depend heavily on the quality of their components and workmanship, as well as optimal bonding and sealing.
In microwaves, the glass door is both a design and functional element. Brackets are bonded to the glass door inside with a structural adhesive from Henkel to attach the door frame, which holds the inner glass pane inserted there.
The heat-resistant glass of the door not only provides a clear view of the cooking or baking process but is also an essential part of the safety mechanism of microwave ovens to contain microwave radiation.
The accurate bonding and sealing of the door glass and the door latch ensure that microwave radiation remains inside the appliance when the door is closed.
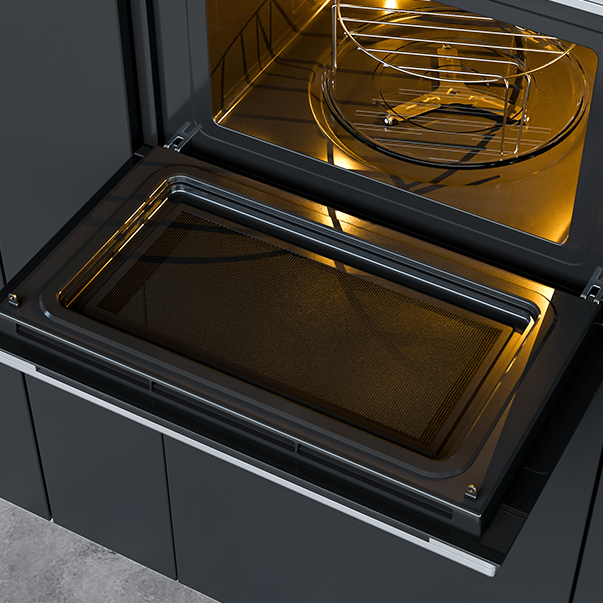
Whatever the material of your product, from plastic to glass ceramic to stainless steel, we offer a wide range of innovative structural adhesives with a variety of properties.
Are you looking for a complete system solution for bonding glass doors of microwaves from a single source?
We can provide you with an optimally coordinated system solution consisting of adhesive, dosing system and process automation. It offers fully automatic material application and high-precision dispensing controlled by contour robots. This allows you to meet your various technical requirements optimally and reliably.
Our system solutions give you exactly the longevity, quality and reliability that your customers expect from your products.
Customized adhesive solutions for microwave doors
LOCTITE® 2-component silicone structural adhesives for bonding interior door glazing
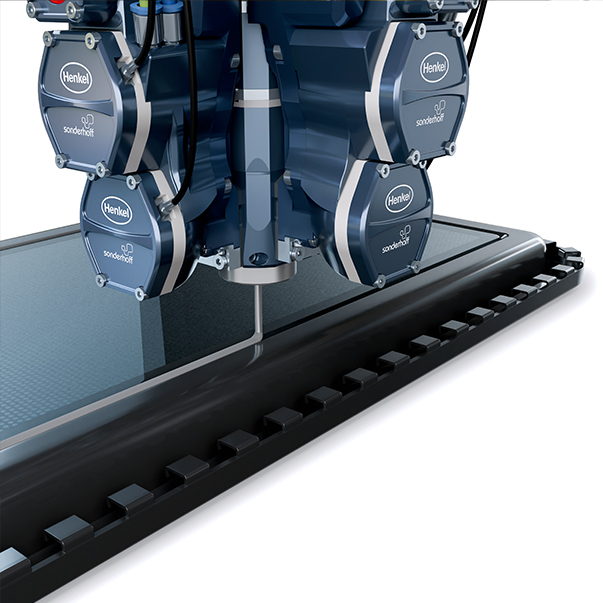
For many years, leading appliance manufacturers have relied on our wide range of innovative adhesive systems for bonding the inner glass pane of microwave doors. The glass bonding of the microwave door also acts as a seal to prevent microwave radiation from escaping the microwave chamber.
LOCTITE® SI 5619 A/B is a fast curing 2-component silicone structural adhesive with low viscosity for easy dispensing and self-leveling. The surface of the adhesive forms a skin after approximately 10 minutes upon exposure to atmospheric moisture at 23 °C / 50 % RH.
The self-leveling property of this silicone adhesive results in an almost seamless coupling of the circumferential adhesive bead. This aesthetic eliminates the need to cover the gap between the inserted glass pane and the adhesive-sealed frame.
LOCTITE®SI 5619 A/B has a good bond strength to porcelain coated metals, steel and stainless steel, as well as Ceran® glass, polycarbonate and ABS surfaces.
Reference material
LOCTITE® SI 5619 A/B |
||
Mixing ratio (by weight) |
4 : 1 | |
Adhesive release time at 23 °C / 50 % RH |
approx. 10 min. |
|
Curing at ambient temperature |
approx. 30 min. |
|
Viscosity A-Component |
approx. 19,000 mPa·s |
|
Viscosity B-Component |
approx. 20,000 mPa·s |
|
Shore-A-Hardness (ISO 868) |
approx. 35 |
|
Elongation at break (ISO 527-3) |
200 % |
|
Tensile strength (ISO 527-3) Tear strength (ISO 34-1) |
approx. 0.9 (130 psi) 1.1 N/mm |
|
Service temperature |
from -40 to +200 °C |
Structural adhesive application with precision mixing head MK 825 PRO
The silicone structural adhesive LOCTITE® SI 5619 A/B is applied directly into the gap between the inserted glass pane and the door frame of the microwave door using FIP (Formed-In-Place) technology and our fully automatic dosing machines – very precisely, safely and efficiently.
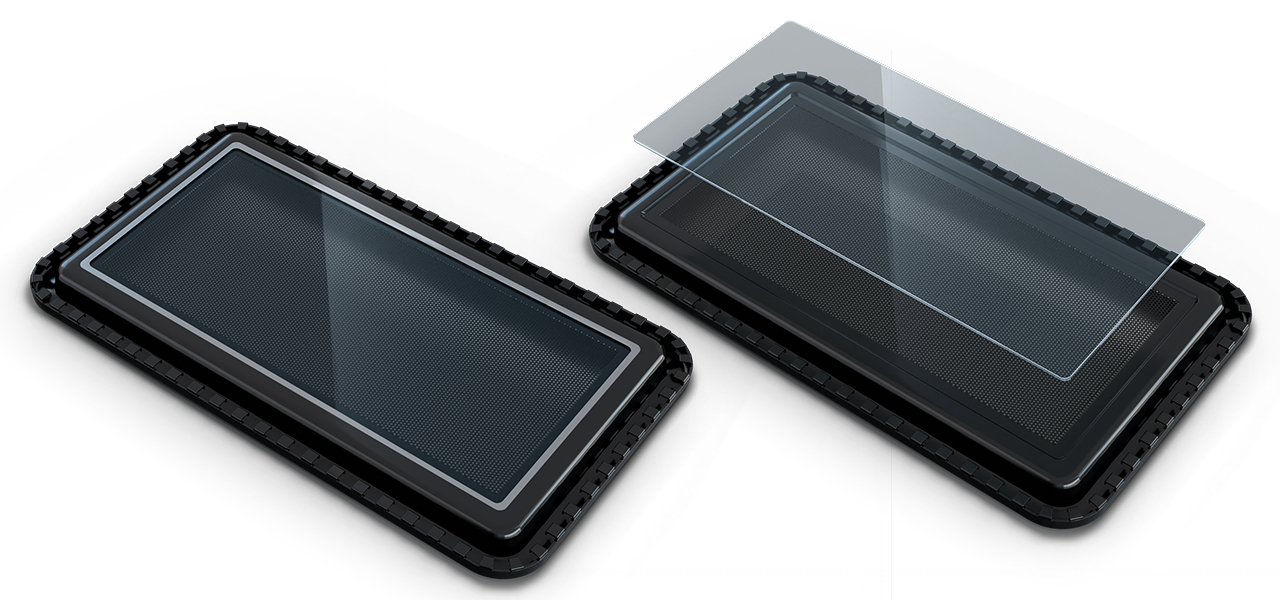
DM 502 mixing and dosing system with 3-axis linear robot for adhesive application for glass bonding of microwave doors
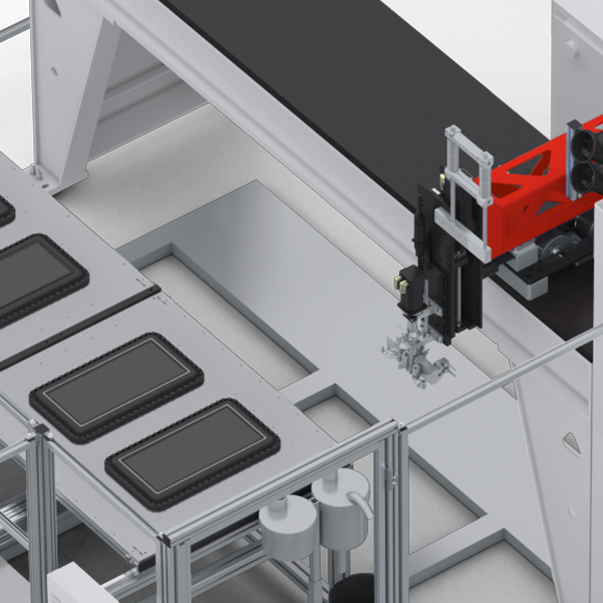
Flexible and fully automatic – according to your requirements
Leading appliance manufacturers rely on our joining and bonding technologies, as well as our formed-in-place (foam gasket) sealing technology, for the fully automated application of LOCTITE® structu- ral adhesives.
The reference configuration shown here consists of the DM 502 mixing and dispensing system with a 3-axis linear robot and a shuttle/sliding table. It is used for precise, fully automated adhesive application for glass bonding of microwave doors. For these applica- tions, we also offer the option of using a transfer belt when different processing steps are combined in a production line at the customer‘s premises.
Parts are picked up and processed on the WT 1-LEVEL shuttle table in continuous pendulum operation in one plane.
The highly dynamic LR-HD ensures that the MK 825 PRO precision mixing head is guided over the part with contour accuracy. The mi- xing head applies the adhesive precisely and fully automatically with high dosing accuracy into the gap between the frame and the glass pane inserted on the inside of the door.
The LOCTITE® structural adhesive and the dispensing machine used are optimally matched and ensure a precise and efficient application process for the glass bonding of the microwave door thanks to the contour robot-controlled mixing head.
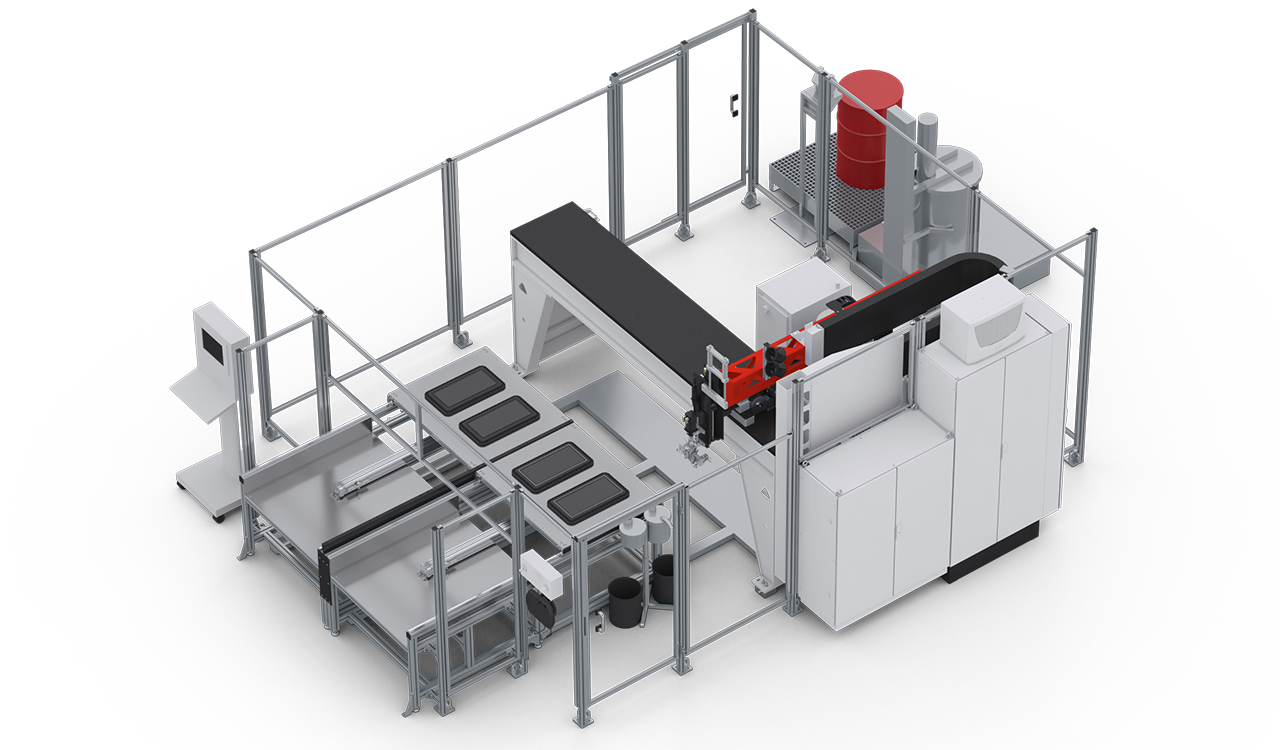
Mixing head 825 PRO
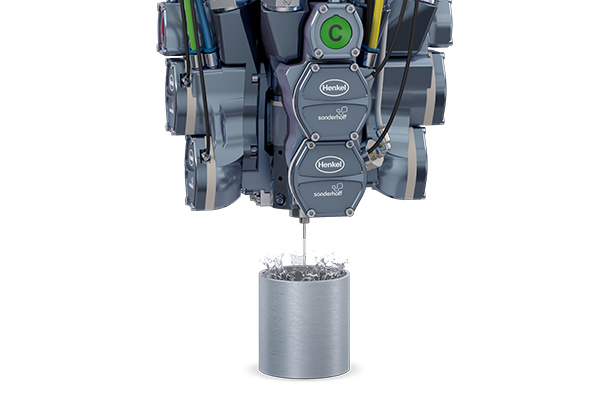
MK 825 PRO precision mixing head with high-pressure water rinsing or alternative component rinsing system
More information to our mixing headsDosing machine cabinet
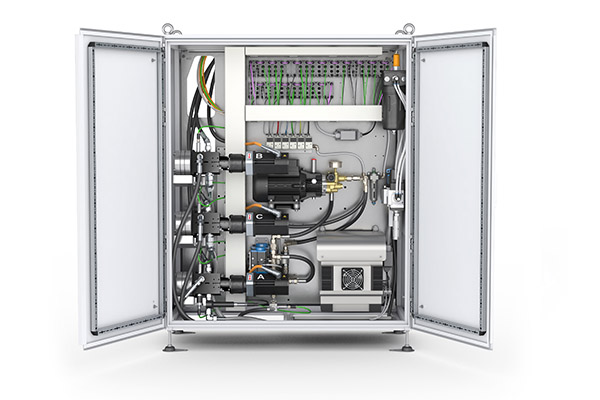
The dosing machine cabinet contains the components of the dosing periphery, e.g. the dosing pumps.
More information to our dosing machine cabinetsControl cabinet
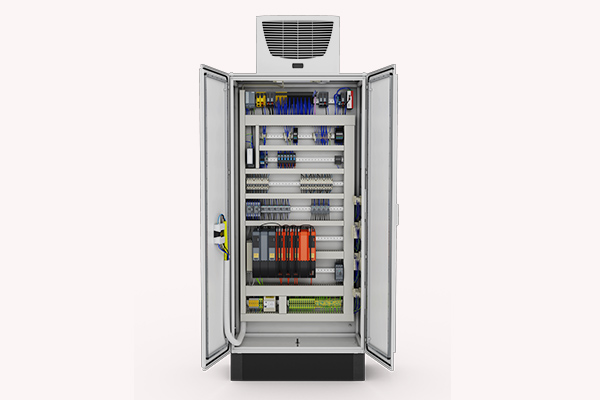
The control electronics, safety engineering and industrial PC are installed in the control cabinet.
More information to our control cabinetsCONTROL 2
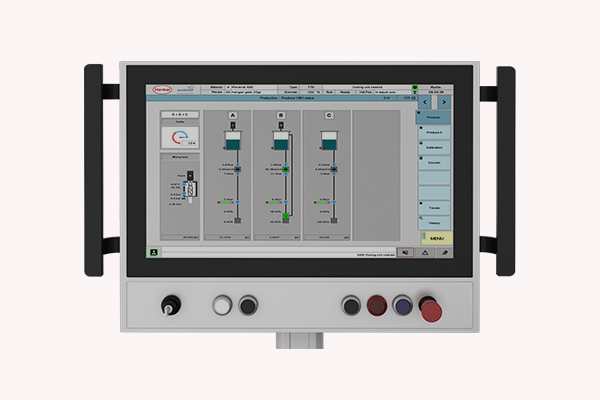
Optionally available: CONTROL touchscreen operating panel (21.5“) for operating the dosing system
More information to our operating panelsWT 1-LEVEL shuttle / sliding table
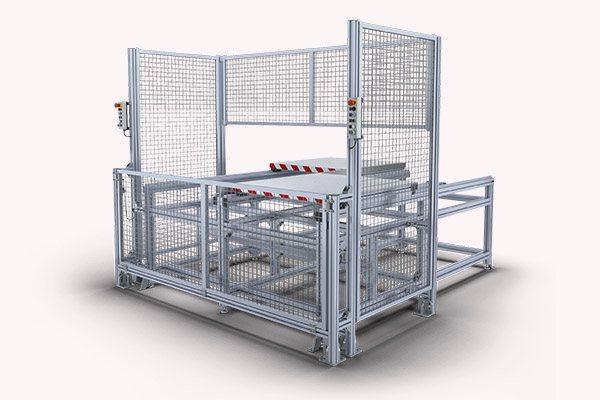
Two pick-up plates operating in pendulum mode in one plane
More information to our shuttle tablesSUPPLY TAP
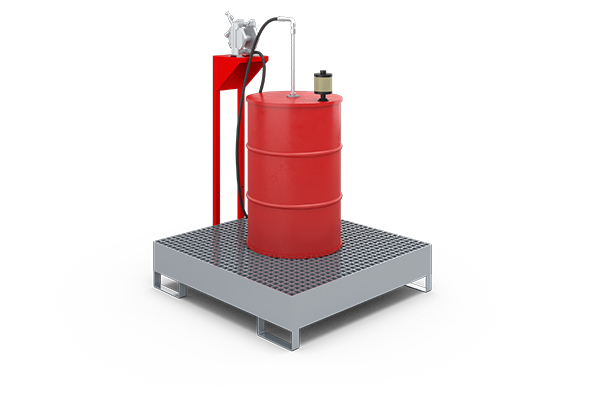
Optional for B-material component: automatic SUPPLY TAP drum refilling station
More information to our refilling stationsELEVATOR
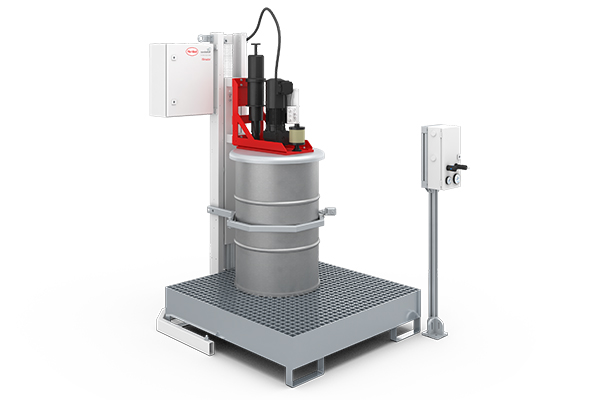
Optional for A-material component: automatic ELEVATOR drum refilling station with pneumatic lift and agitator
More information to our refilling stationsMP 2 mobile panel
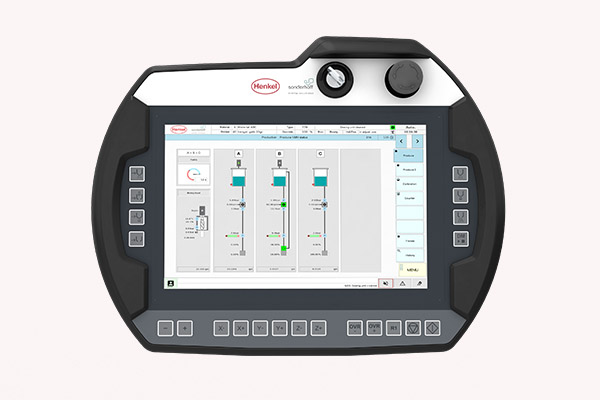
The multifunctional MP 2 mobile panel (10.1” WXGA TFT) enables convenient operation of the dosing system.
More information to our operating panelsMaterial pressure tanks
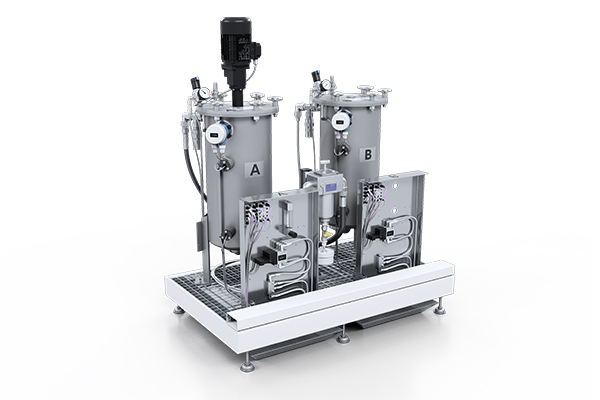
Material pressure tanks (24 l or 44 l, single-walled or double-walled) with minimum level sensors, on a grating platform with adjustable leveling feet and drip tray
More information to our material Pressure TanksLinear robot LR-HD
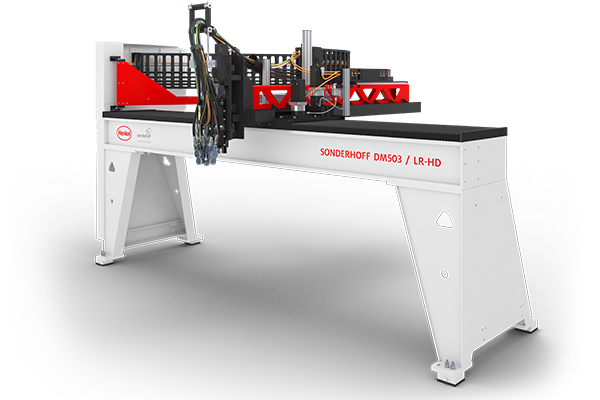
Highly dynamic 3-axis linear robot LR-HD for the precise guidance of mixing heads for the application of polymer reaction materials. The rack and pinion drive with high rigidity and acceleration enables dynamic application speeds.
More information to our linear robots