Das MOLD'N SEAL Prozessverfahren
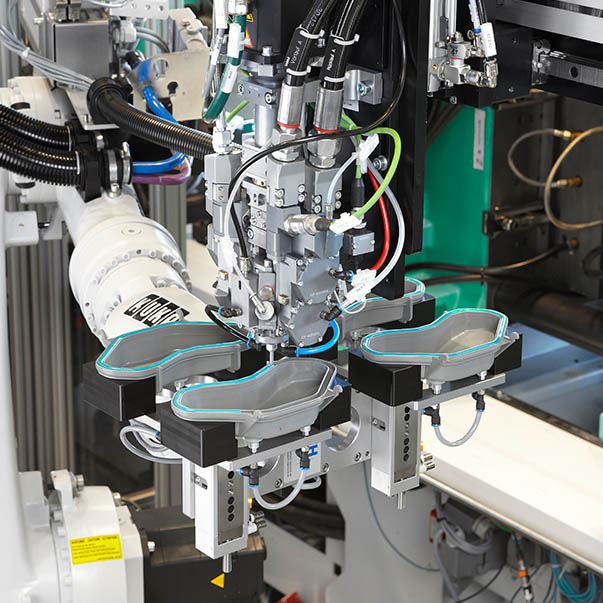
Kombination von Spritzgießen und Dichtungsschäumen
Das MOLD'N SEAL Prozessverfahren – die Kombination von Spritzgieß- und Misch- und Dosieranlage in einer Fertigungszelle – wurde in Kooperation mit den Spritzgießmaschinenherstellern Arburg und Engel entwickelt.
Unmittelbar nach der Entnahme aus dem Spritzgusswerkzeug wird auf das spritzgegossene Bauteil eine dafür speziell entwickelte Fast-Cure Polyurethanschaumdichtung aus der Produktfamilie FERMAPOR K31 aufgetragen.
Durch die Integration der bisher getrennten Prozesse Spritzgießen und Dichtungsschäumen in einem Fertigungsschritt unter den Gesichtspunkten Effizienz und Produktqualität kann auf eine teure Zwischenlagerung vorproduzierter Spritzgießteile verzichtet werden.
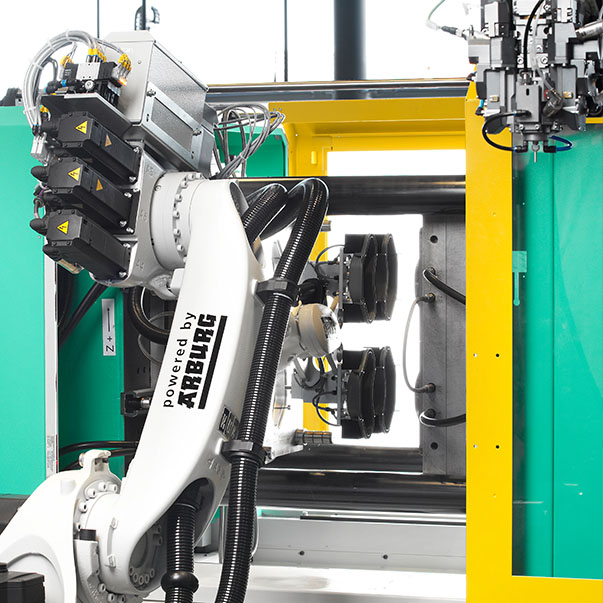
Mit MOLD'N SEAL können folgende Einsparpotentiale realisiert werden:
- Aufgrund einer kürzeren Ausreaktion des Fast-Cure Dichtungsmaterials (nach ca. 120 Sekunden klebfrei) ist eine schnelle Weiterverarbeitung möglich.
- Anstatt bisher zwei wird nur noch ein Roboter für das Teile-Handling beider Abläufe (Spritzgießen und Dichtungsschäumen) benötigt, Investitions-, Lager- und Personalkosten können dadurch eingespart werden.
- Durch die Prozessintegration werden Spritzgussanlage, 6-Achs Handlingroboter, Misch- u. Dosiermaschine und Austaktband sehr platzsparend auf kleiner Stellfläche von nicht mehr als 24 bis 40 qm eingesetzt.
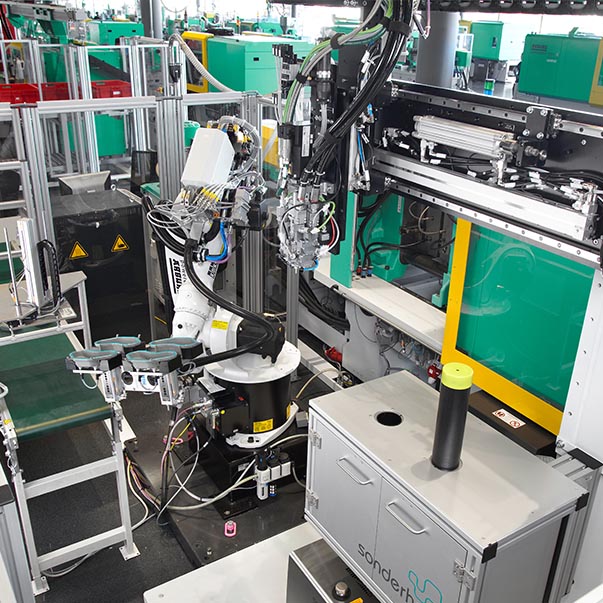
MOLD'N SEAL Prozessablauf:
Der Knickarmroboter entnimmt die noch warmen Spritzgussbauteile aus dem Werkzeug. Unmittelbar danach hält der Roboterarm die Teile unter den Mischkopf MK 800 der Dosieranlage DM 502/503, damit so das Dichtungsmaterial präzise auf die Teilekontur aufgetragen wird. Das Polyurethan Fast-Cure-System aus der Produktfamilie FERMAPOR K31 härtet durch die bewusste Nutzung der noch vorhandenen Restwärme des spritzgegossen Bauteils deutlich schneller aus. Bereits kurz nach dem Auftragen der Dichtung positioniert der Knickarmroboter das fertige Bauteil zur Weiterverarbeitung auf das Austaktband.
Das MOLD'N SEAL Prozessverfahren kann an unterschiedlich lange Spritzgießzyklen angepasst werden. Es können Bauteile mit unterschiedlichsten Geometrien und verschiedenen Werkzeugkavitäten (Ein- bis Vierfach-Werkzeuge) im direkten Anschluss an die Spritzgießfertigung beschäumt werden. Zusätzliche Prozesse wie Vorbehandlung der Kunststoffoberfläche durch Ionisierung oder Plasmabehandlung können ebenfalls integriert werden.
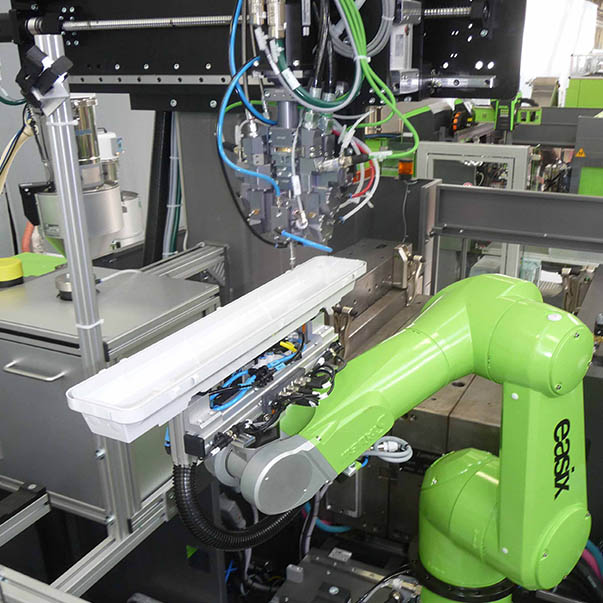
Automation mit Engel
Gemäß dem MOLD’N SEAL Prozessverfahren wurden auf einer hydraulischen Spritzgießmaschine von ENGEL, der Baureihe „victory 1350/300 tech“, Kunststoffgehäuse für Feuchtraumleuchten von Zumtobel Lighting gespritzt und unmittelbar danach über den Mischkopf der SONDERHOFF Misch- und Dosieranlage von Henkel eine Polyurethan Schaumdichtung der Produktlinie FERMAPOR K31 in die Gehäusenut aufgetragen.
Innerhalb von 55 Sekunden pro Spritzgießzyklus konnten in einer achtstündigen Fertigungsschicht ohne Unterbrechung insgesamt über 523 Leuchtengehäuse spritzgegossen, aus der Form entnommen, beschäumt und zur Aushärtung sowie Weiterverarbeitung auf ein Austaktband abgelegt werden.
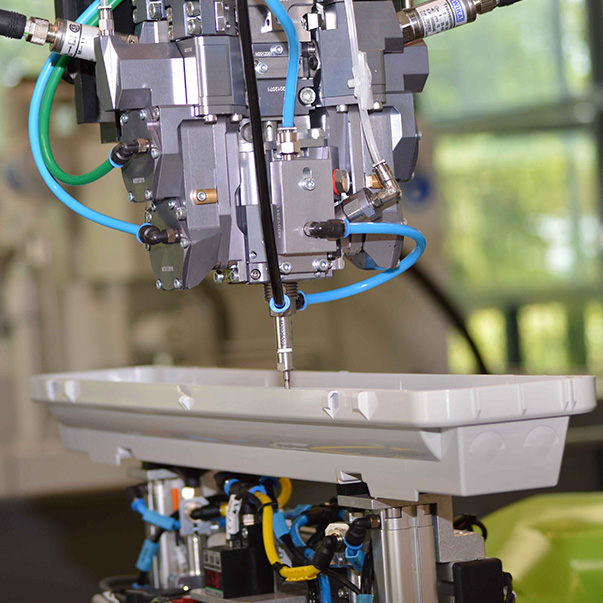
Prozessdetails
Der Prozessablauf im Einzelnen: Das Kunststoffgehäuse der Feuchtraumleuchte wird mittels „ENGEL easix“ Roboter aus der Spritzgießanlage entnommen und in eine Warte- und Abkühlposition abgelegt. Danach greift der Roboterarm ein bereits abgekühltes Bauteil, führt es an der Ionisierungsstation vorbei weiter zum Mischkopf MK 800 der Misch- und Dosieranlage DM 502 und positioniert die Nut des Leuchtengehäuses direkt unter die Mischkopfdosierdüse. Der Mehrachsroboter ist so programmiert, dass er die Bauteilnut in zwei Umläufen konturgenau abfährt, wobei die Dosierdüse des MK 800 das Dichtungsmaterial präzise am Grund der nur wenige Millimeter breiten Dichtungsnut aufträgt.
Die Austragsleistung pro Umlauf ist hierbei nur 0,45 g/s. Nach der Ablage auf dem Austaktband kühlt das Spritzgießteil ab und die Schaumdichtung wird innerhalb von zwei bis drei Minuten klebfrei. Eine Weiterverarbeitung ist somit bereits nach kurzer Zeit möglich.
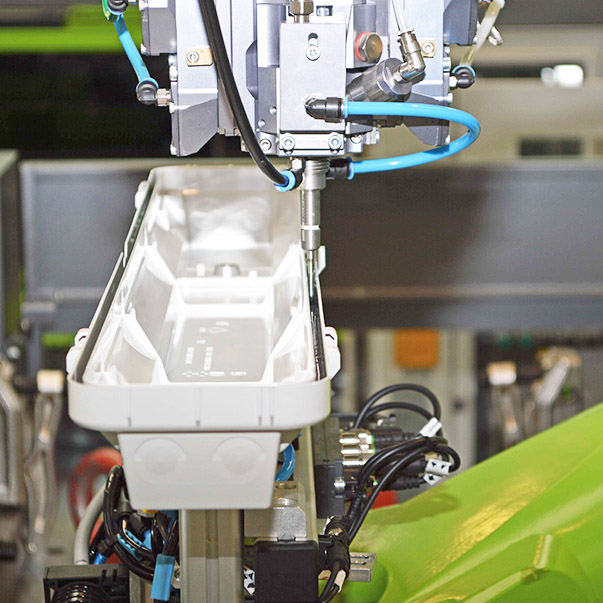
Materialauswahl
Das für MOLD'N SEAL speziell entwickelte, schnell reagierende 2-Komponenten Fast-Cure Dichtungsmaterial aus der FERMAPOR K31 Produktfamilie kann in diesem Fall eine Mischkopfwartezeit von 25 Sekunden überbrücken.
In dieser Zeit greift der Roboterarm ein neues Spritzgießteil aus dem Werkzeug, legt es in die Abkühlposition, entnimmt ein bereits dort abgelegtes Bauteil, führt es an der Ionisierungsstation vorbei und mit seiner Positionierung unter den Mischkopf beginnt der Dichtungsauftrag von neuem.
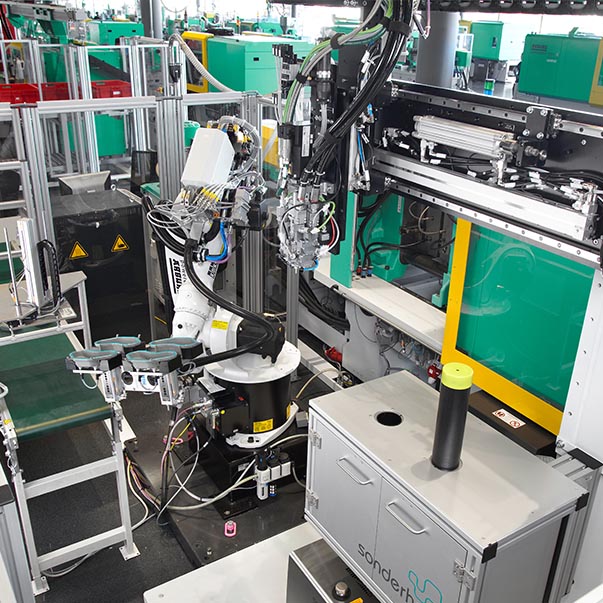
Automation mit Arburg
Mit dem MOLD'N SEAL Prozessverfahren wurden auf einer hydraulischen Spritzgießmaschine von Arburg, der Baureihe „Allrounder 570 S“ mit 2.200 kN Schließkraft, in einer Fertigungsschicht von acht Stunden insgesamt über 2.500 Scheinwerfergehäuseteile aus Kunststoff (back caps) spritzgegossen und unmittelbar danach mit einer Polyurethandichtung beschäumt.
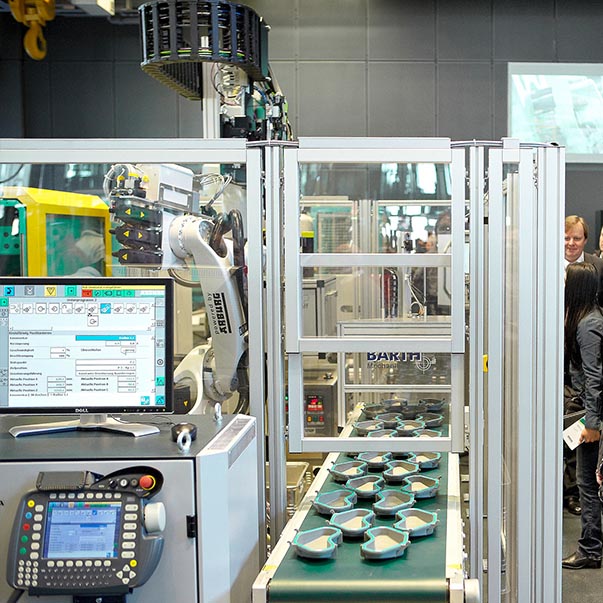
Prozessablauf
Der Prozessablauf im Einzelnen: Innerhalb einer Taktzeit von 45 Sekunden werden vier Bauteile spritzgegossen, mit Hilfe eines 6-Achs-Handlingroboters aus dem Vierfach-Werkzeug entnommen, unmittelbar danach mit der speziell für MOLD'N SEAL entwickelten Fast-Cure Polyurethandichtung FERMAPOR K31 mit Hilfe der Misch- und Dosieranlage DM 502 beschäumt und zur Aushärtung sowie Weiterverarbeitung auf das in der Fertigungszelle integrierte Austaktband abgelegt.
Der Mehrachsroboter ist so programmiert, dass er die Bauteilnut konturgenau abfährt, wobei die Dosierdüse des MK 800 das Dichtungsmaterial präzise in die Nut einbringt. Die Austragsleistung ist hierbei 1,17 g/s. Der Handlingroboter übergibt die Bauteile an die Umsetzstation, die sie zur Aushärtung auf das Austaktband ablegt. Die Schaumdichtung wird innerhalb von zwei bis drei Minuten klebfrei und die Bauteile können bereits nach kurzer Zeit weiterverarbeitet werden.
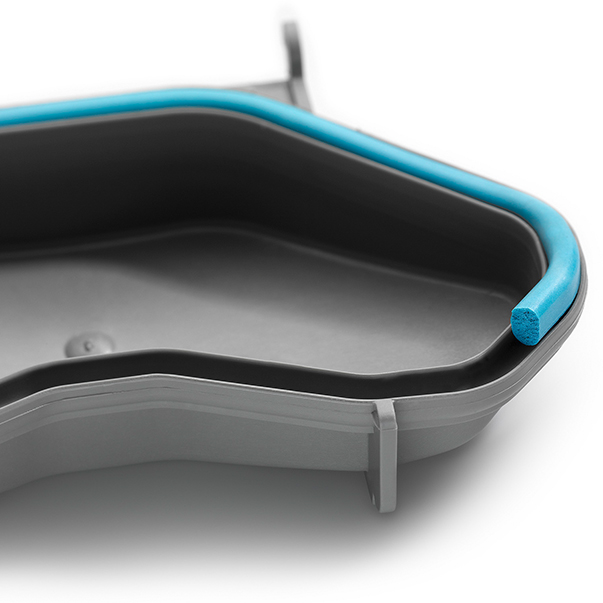
Materialauswahl
Das für MOLD'N SEAL speziell entwickelte, schnell reagierende 2-Komponenten Dichtungsmaterial Fast-Cure aus der FERMAPOR K31 Produktfamilie ist an den Spritzgießzyklus so angepasst, dass es in diesem Fall eine Mischkopfwartezeit von 18 Sekunden überbrücken kann. In dieser Zeit greift der Roboterarm vier neue Spritzgießteile aus dem Werkzeug, hält sie unter den Mischkopf MK 800, der nacheinander die Kontur der vier Bauteile zum Auftragen der Schaumdichtung abfährt.
Nach der Übergabe an die Umsetzstation, die Scheinwerfergehäuseteile auf das Austaktband zur weiteren Verarbeitung positioniert, startet der Dichtungsauftrag von neuem.