Dichtungsschäumen mit der FIPFG-Technologie
Der Industriestandard für viele Branchen
Das Dichtungsschäumen mit der FIPFG-Technologie (Formed-In-Place-Foam-Gasket) ist im Vergleich zu konventionellen Einlegedichtungen (EPDM, TPE, NBR) deutlich wirtschaftlicher und effizienter. Die flüssige oder thixotrope 2-Komponenten Dichtmasse wird über den in der Regel beweglichen Mischkopf der SONDERHOFF Misch- und Dosieranlage direkt („in-place“) auf das Bauteil aufgetragen, wo sie zur Schaumdichtung („foam gasket“) bei Raumtemperatur ausreagiert.
Damit können, bei gleichzeitiger Kostenersparnis und hoher Reproduzierbarkeit, wesentlich bessere Dichtungsergebnisse erzielt werden als mit herkömmlichen, von Hand eingelegten Dichtungen.
Von der natürlichen zur synthetischen Dichtung
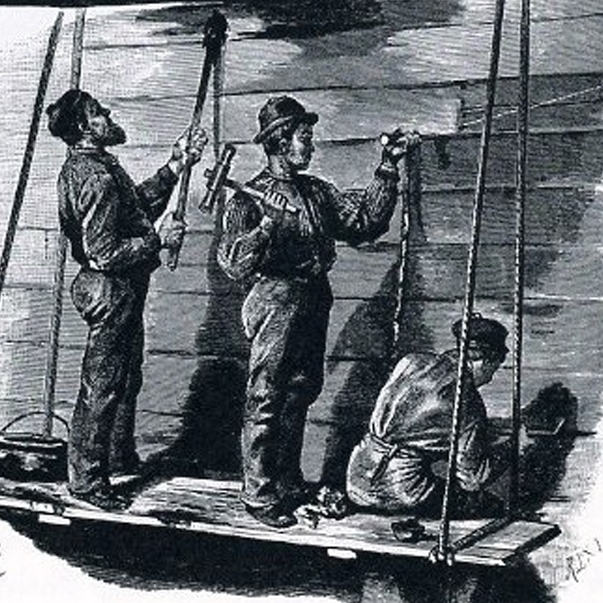
Das Abdichten von Fugen und Spalten beherrschen die Menschen schon seit langer Zeit, z.B. zum Abdichten von Holzplanken im Schiffsbau. Man benutzte Bienenwachs, Baumharz oder Teer.
Die Geschichte der modernen Dichtstoffe beginnt mit der Polymerchemie in den 1930er Jahren, der Entwicklung synthetischer Kunst- und Dichtstoffe. Und die Geschichte wird weiter fortgeschrieben. Heute steht für das Abdichten von Bauteilen eine große Vielfalt an Materialien und Technologien zur Verfügung.
Zusätzlich ist durch die industrielle Fertigung der Neuzeit eine entscheidende Anforderung hinzugekommen. Die Abdichtprozesse müssen idealerweise vollautomatisch ablaufen. Dieser automatische Applikationsprozess für das Dichtungsschäumen wird allgemein als FIPFG-Technologie (Formed-In-Place-Foam-Gasket) bezeichnet.
Die Chemie macht’s möglich
Polymere Reaktionswerkstoffe
Die polymeren Reaktionswerkstoffe der SONDERHOFF Produkte von Henkel bestehen aus einer flüssigen bis pastösen A-Komponente (Polyol) mit unterschiedlich langen Molekularketten für Weich- und Hartschäume und einem Härter, der B-Komponente (MDI-Isocyanat). Die Materialsysteme auf Basis von Polyurethan sind unter dem Markennamen FERMAPOR K31 zusammengefasst. Die Silikon basierten Produkte heißen FERMASIL.
Ein Polymer ist ein Stoff, dessen Moleküle aus verketteten Monomereinheiten bestehen. Je länger die Molekülketten der Polyole (A-Komponente), desto flexibler sind die Weichschäume. Durch eine chemische Reaktion mit Wasser und dem Härter (B-Komponente) wird eine vernetzte Struktur der Molekülketten ausgebildet. Dabei entsteht als Spaltprodukt Kohlendioxid, das beim Niederdruckverfahren für das Aufschäumen verantwortlich ist. Es entsteht eine Weischaumdichtung, die bei Raumtemperatur, ohne Einsatz eines Temperofens, aushärtet.
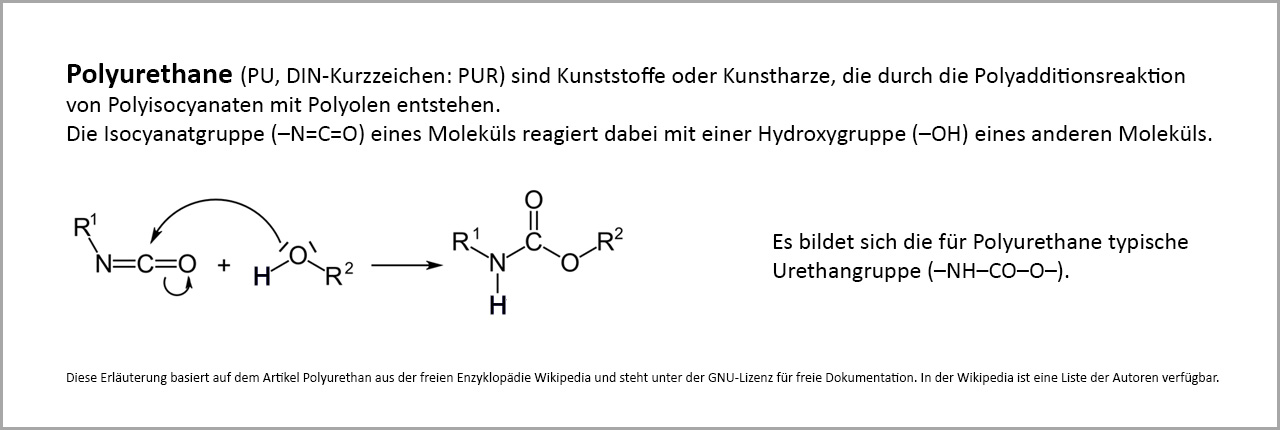
2-Komponenten Materialsysteme
Die A-Komponente (Polyol) ist der Träger für die chemischen und physikalischen Eigenschaften der Dichtungsschäume. Die B-Komponente (Isocyanat) stößt die chemische Reaktion an und beeinflusst vor allem die Reaktionsgeschwindigkeit. Wir sprechen daher von „2K“, also 2-Komponenten-Materialsystemen. Das Mischungsverhältnis von A- und B-Komponente spielt dabei eine entscheidende Rolle.
Ungefähr 90 % der Schaumdichtungssysteme sind 2K-PU-Materialsysteme, die unter Einsatz von Polyurethan Polyolen entwickelt werden. Dieser Werkstoff ist besonders vielseitig in der Anwendung.
Je nach Wahl des Polyols und des Isocyanats können Polyurethane unterschiedliche Eigenschaften aufweisen. Je nach Kettenlänge und ihrer Verzweigungen im Polyol werden die mechanischen Eigenschaften positiv beeinflusst.
Silikon wird vor allem dann eingesetzt, wenn es um hohe Beständigkeit gegen Chemikalien, Lösungsmittel, sehr hohe Temperaturen und Witterungseinflüsse geht.
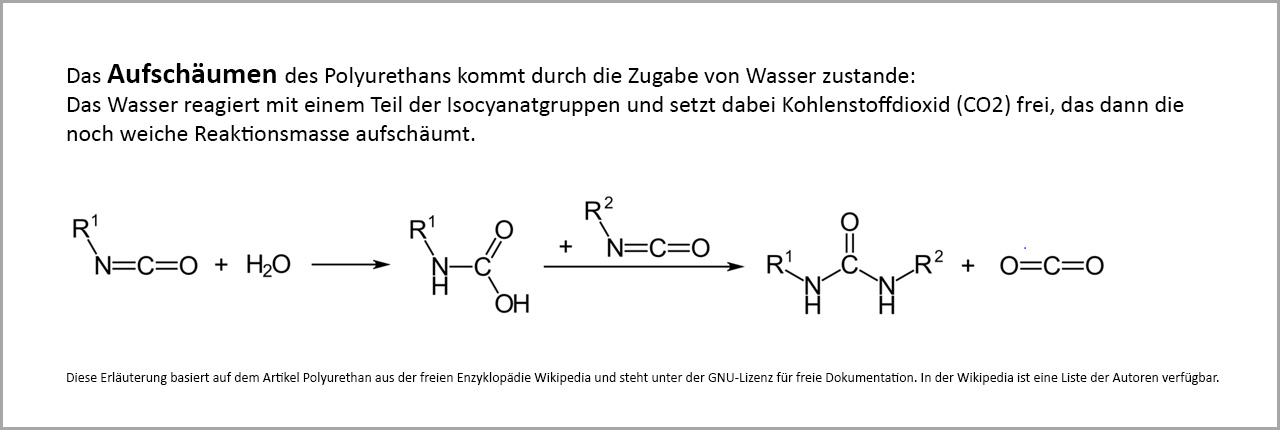
Topfzeit und Steigzeit
Topfzeit
Die Dauer der Verarbeitbarkeit von reaktiven Werkstoffen wird als Topfzeit bezeichnet. Beim Dichtungsschäumen ist es die Zeit der Vermischung der A- mit der B-Komponente in der Mischkammer vor Dosierung auf das Bauteil. Bildlich gesprochen ist es die Zeitspanne, in der sich die Substanzen noch aus dem Topf nehmen und verarbeiten lassen. Meist zeigt sich das Ende der Topfzeit durch deutlichen Viskositätsanstieg, der eine weitere Verarbeitung verhindert. Die Dauer der Topfzeit ist abhängig von den chemischen Eigenschaften der eingesetzten Komponenten und von den Umweltbedingungen.
So ist die Angabe der Topfzeit eines Stoffes nur sinnvoll und aussagekräftig mit zusätzlicher Angabe der Menge, Durchmischung, Umgebungsklima (Temperatur und Feuchte) und Gefäßform.
Steigzeit
Die Steigzeit beim FIPFG-Verfahren ist die Zeitspanne nach der Topfzeit, in der die homogen vermischte Dichtmasse des eingesetzten Materialsystems aufschäumt und zu einem Dichtungskörper expandiert.
Mit der chemischen Reaktion zwischen Isocyanat und dem Wasser der Polyol-Komponente entsteht als Spaltprodukt das zur Schaumherstellung erforderliche Treibgas CO2. Durch die während der Reaktion ansteigende Temperatur (exotherme Reaktion) schäumt das CO2-Gas die Dichtmasse auf.
Zum Ende der Steigzeit hat das Treibgas seinen Dienst getan und kann durch die gemischtzellige Zellstruktur der Polyurethan Weichschäume entweichen.
Flüssigdichtungen, in-situ-Dichtungsschäumen, Cured-In-Place - FIPFG (Formed-In-Place-Foam-Gasket)!
Traditionell erfolgt die Abdichtung von Bauteilen mit vorgestanzten Moosgummidichtungen oder durch Verkleben von Dichtungsschnüren. Heute, bei zunehmendem Automatisierungsgrad, werden flüssige oder thixotrope Dichtungsschäume mit Dosieranlagen direkt an Ort und Stelle auf die Bauteile aufgetragen. Dort härten sie unter Raumtemperatur aus. Geläufig sind auch die Begriffe In-Situ-Dichtungsschäumen, das Auftragen von Flüssigdichtungen auf ein Bauteil an Ort und Stelle, ortsgeschäumte Dichtungen oder Cured-In-Place (CIP). Letzteres stellt das Aushärten der Schaumdichtung unter Raumtemperatur heraus.
Die FIPFG-Technologie hat sich als Industriestandard für unterschiedlichste Bauteilanwendungen durchgesetzt. Entscheidend für die FIPFG-Technologie sind das Zusammenspiel von Materialsystem und Maschinen- technologie sowie das anwendungsspezifische Verständnis für den Prozess.
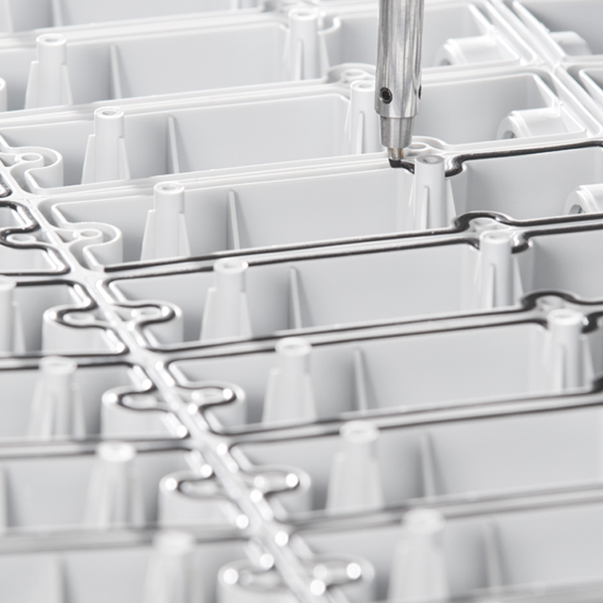
Der FIPFG-Schaumdichtungsprozess
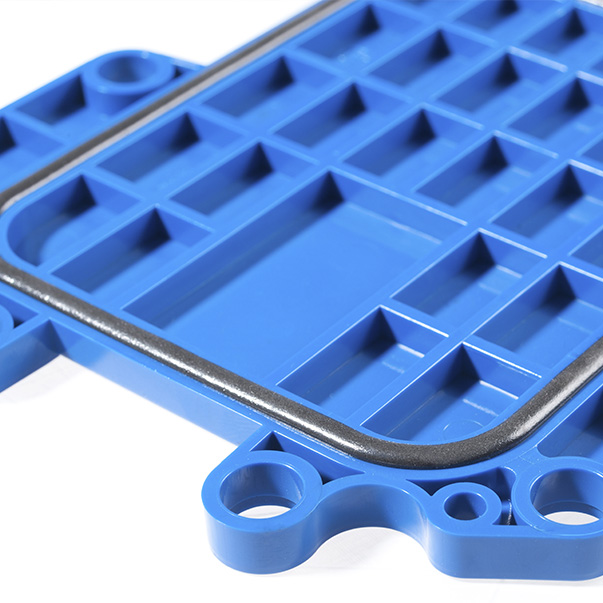
Chemisches oder physikalisches Schäumen
Bei der chemischen Reaktion der Komponenten A (Polyol) und B (Isocyanat) mit Wasser entsteht CO2, das als Treibmittel wirkt und das Material aufschäumt. Es bildet sich eine gemischtzellige Weichschaumdichtung.
Beim physikalischen Aufschäumen, unter direkter Luftzufuhr in die Dosierkopf-Mischkammer, bildet sich eine geschlossenzellige Polyurethan-Schaumdichtung. Diese SONDERHOFF FIP CC Systeme sind am Namenszusatz „CC“ für „closed cells“ zu erkennen.
Bei beiden Verfahren werden keine formenden Werkzeuge benötigt. Allein durch freies Aufschäumen auf der Bauteiloberfläche entsteht die Weichschaumdichtung in der gewünschten Form auf der Oberfläche oder in der Nut des Bauteils.
Ein eleganter und hoch effizienter Prozess:
mischen, dosieren, schäumen.
Die Schaumkomponenten A und B werden in der Mischkammer der Dosieranlage in einem vorgegebenen Mischungsverhältnis homogen vermischt. Dafür werden je nach Rezeptur und Anforderungsprofil unterschiedlich designte Rührwerke eingesetzt.
Unmittelbar danach wird die flüssige oder thixotrope 2-Komponenten Dichtmasse über den CNC gesteuerten Mischkopf der Dosieranlage direkt („in-place“) auf die vorprogrammierte Bauteilkontur präzise aufgetragen. Die dort konturgenau abgelegte Dichtungsraupe schäumt um das mehr als 3-fache ihres ursprünglich flüssigen Materialvolumens auf.
Schon nach wenigen Minuten hat sich bei Raumtemperatur eine weiche, nahtlos geschlossene Schaumdichtung ausgebildet. Im Gegensatz zur eingelegten Dichtungsschnur oder Moosgummidichtung entsteht keine Nahtstelle, durch die z.B. Feuchtigkeit in das Bauteil dringen kann. Die Kopplungs- stelle der Dichtungsraupe ist zudem fast völlig unsichtbar.
Die FIPFG-Schaumdichtung passt sich an jede beliebige Werkstückgeometrie an und gleicht Maßtoleranzen aus.
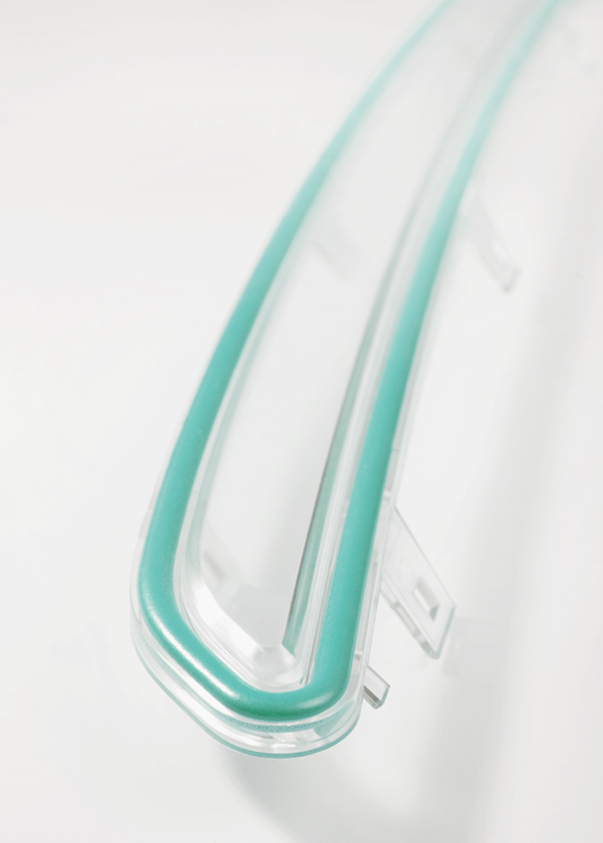
Mit der richtigen Maschine geht’s quasi von allein
Vollautomatisch, präzise, wiederholgenau
Aufgrund der präzisen vollautomatischen Steuerung der Dosieranlage lässt sich der Schäumungsprozess jederzeit exakt reproduzieren. Dazu bewegt der Linearroboter den Mischkopf mit einer Wiederholgenauigkeit von +/- 0,1 mm über dem Bauteil. Die Steuerung der Dosieranlage koordiniert die Dosierung der Auftragsmenge mit der Verfahrgeschwindigkeit des Linearroboters.
Das ortsgeschäumte Dichtungsschäumen kann bei den thixotropen (pastösen) Dichtungssystemen mit hoher Viskosität auf ebener oder 3-dimensionaler Fläche auch ohne Nut erfolgen. Auch extreme Schrägen sind mit dem FIPFG-Dichtungsschäumen möglich, ohne dass Material zurück oder zur Seite fließt.
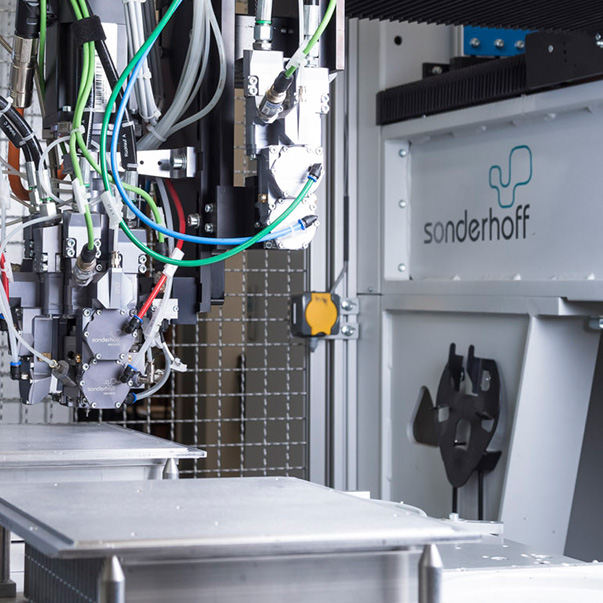
SONDERHOFF SYSTEM SOLUTIONS: Optimales Zusammenspiel von Material und Maschine für Ihren Fertigungsprozess sowie Lohnfertigungslösungen
Als FIPFG-Experte stellen wir mit unseren SONDERHOFF Misch- und Dosieranlagen die Genauigkeit der Abdichtungs- prozesse sicher. Im Sondermaschinenbau bauen wir die Dosieranlagen optimiert auf Ihre Anforderungen, um sie bestmöglich in Ihre Fertigungskonzepte zu integrieren.
Unterschiedliche Automationslösungen sowohl für 2D- als auch 3D-Bauteile können realisiert werden. Mit 3-Achs-Linearrobotern ist ein Verfahrbereich für den Misch- und Dosierkopf von bis zu X/Y/Z 3.000 x 1.000 x 500 Millimetern darstellbar. Bei Einsatz von 6-Achs-Robotern sind praktisch keine Grenzen mehr gesetzt und bei Verwendung von Matrialsystemen mit geeigneter Viskosität sind sogar Überkopf-Applikationen möglich.
Modularer Aufbau für individuelle Konfigurationen
Für das Dichtungsschäumen mit der FIPFG-Technologie stehen den Anwendern SONDERHOFF Misch- und Dosieranlagen in offener und geschlossener Bauweise zur Auswahl, um so für größere als auch kleinere Bauteile den Raumbedarf zu optimieren. Für gemischtzellige Schaumdichtungen bieten wir unseren Kunden die sehr erfolgreichen und bewährten Niederdruckanlagen an. Für die geschlossenzellige Schaumdichtung steht die exklusive Weltneuheit der Mitteldruckanlagen zur Verfügung.
Die Dosieranlagen übernehmen die Aufgaben Material- aufbereitung, Materialauftrag über den Mischkopf, Automation und Prozessteuerung. Flüssige, mittel- und hochviskose Reaktionswerkstoffe aus Polyurethan, Silikon, Epoxidharz können so mit diesen Anlagen exakt verarbeitet werden.
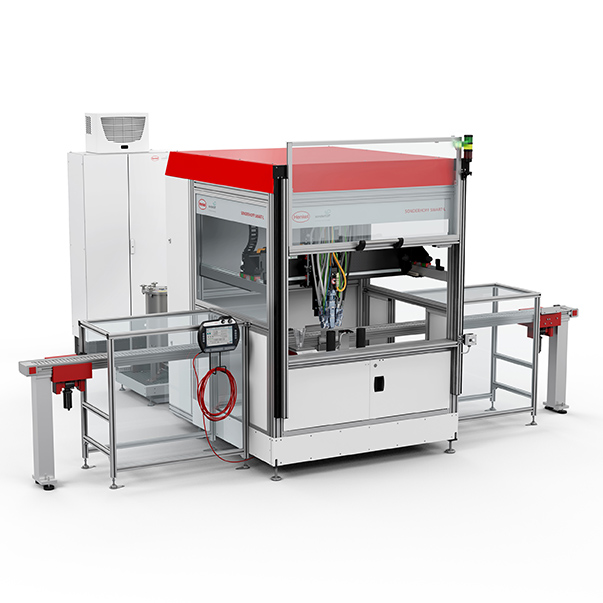
Kompressionsverhalten der Dichtung
Bauteile werden durch Kompression von 2-Komponenten Schaumdichtungssystemen auf Basis von Polyurethan oder Silikon dauerhaft abgedichtet.
Die gemischtzelligen Polyurethanschäume erreichen optimale Dichtigkeit bei einer Kompression von 30 bis 60 %, die nahezu geschlossenzelligen Silikonschäume bei einer Kompression von 10 bis 30 %, – je nach Härtegrad des Schaums und gemäß der konkreten Anforderungen zur Dichtigkeit.
Je nach Anforderung erfüllen die mit der Schaumdichtung abgedichteten Bauteile in der Gesamtkonstruktion die hierfür geltenden Normen und Schutzklassen (IP bzw. NEMA) zum Schutz vor Staub und Wasser – erreicht werden Schutzklassen bis IP 68 bzw. NEMA 4 und 12.
Für die Dichtigkeit ist ebenso entscheidend, wie feinzellig die Schaumzellenstruktur ist. Aufgrund des Phänomens der Kapillardepression wird Wasser aus sehr kleinen Zellen im größeren Maße hinausgedrängt als aus den Kapillaren einer groben Zellstruktur.
Für den Außeneinsatz bieten die Polyurethanschaumdichtungen eine Temperaturbeständigkeit von -40 bis + 80 °C. Die besonders temperaturbeständigen Silikonschäume bieten einen guten Schutz vor Witterungseinflüssen wie extremer Hitze oder Kälte in einem Bereich von -60 bis +180 °C.
Das gute Rückstellverhalten der komprimierten Schaumdichtung nach ihrer Entlastung ermöglicht ein häufiges Öffnen und Wiederschließen des Bauteils bei einer gleichbleibend hohen Dichtigkeit. Die Rückstellfähigkeit wird im Allgemeinen durch Messung des sogenannten Druckverformungsrestes (DVR) bestimmt und nach DIN EN ISO 1856 geprüft.
Der DVR beschreibt die dauerhaft zurückbleibende Verformung nach Kompression. Die Rückstellfähigkeit von Polyurethanschaum liegt bei > 95 % - das bedeutet im Umkehrschluss, dass der DVR bei < 5 % liegt. Bei Silikonschaum beträgt die Rückstellfähigkeit > 97 %, der DVR < 3 %.
Die Rückstellfähigkeit kann unter verschiedenen Bedingungen (Kompression, Temperatur und Lagerzeit) unterschiedlich sein.
Kompressionsverhalten der PU Schamdichtung auf ebener Fläche
Das Video zeigt die Polyurethan Schaumdichtung FERMAPOR K31 im Querschnitt - zuerst im unverpressten Zustand, dann zu 50 % verpresst, damit ist die Dichtfunktion der Abdichtung gegeben.
Kompressionsverhalten der PU Schamdichtung in einer Nut
Das Video zeigt die Polyurethan Schaumdichtung FERMAPOR K31 im Querschnitt in einer Nut - zurst im unverpressten Zustand, dann zu ca. 50 % verpresst, damit ist die Dichtfunktion der Abdichtung gegeben und das Bauteil dicht.
Kompressionsverhalten der Silikon Schamdichtung auf ebener Fläche
Das Video zeigt die Silikon Schaumdichtung FERMASIL im Querschnitt - zuerst im unverpressten Zustand, dann zu 30 % verpresst, damit ist die Dichtfunktion der Abdichtung gegeben.
Kompressionsverhalten der Silikon Schaumdichtung in einer Nut
Das Video zeigt die Silikon Schaumdichtung FERMASIL im Querschnitt in einer Nut - zurst im unverpressten Zustand, dann zu ca. 30 % verpresst, damit ist die Dichtfunktion der Abdichtung gegeben.
Mit der FIPFG-Technology flexibel auf individuelle Kundenanforderungen eingehen
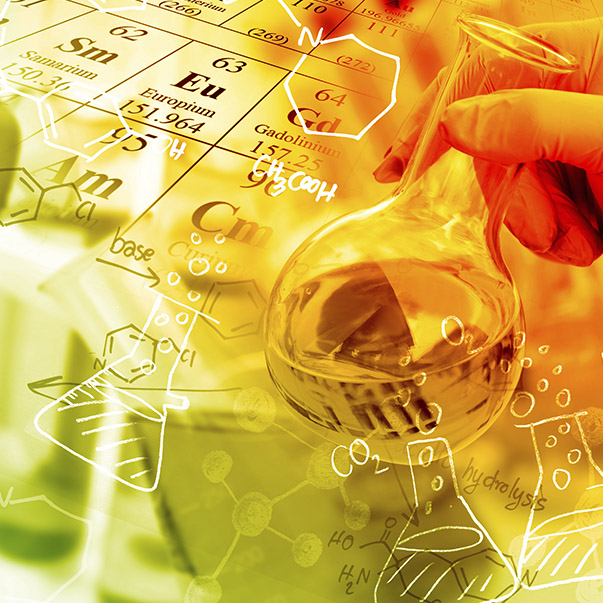
Mit der FIPFG-Dichtungstechnologie (Formed-In-Place-Foam-Gasket) erfüllen wir die hohen Anforderungen unserer Kunden an Abdichtgüte und konturgenauer Dichtigkeit der Bauteile.
Unsere mehr als 1000 Materialformulierungen bieten ein breites Eigenschaftsspektrum. Haftung, Temperaturstabilität, Elastizität, mechanischer Belastbarkeit und chemischer Beständigkeit sind dabei die am häufigsten geforderten Eigenschaften für die Schaumdichtung aus Polyurethan oder Silikon.
So lassen sich Bauteile unterschiedlichster Anwendungen optimal vor dem Eindringen von Luft, Gasen, Staub, Feuchtigkeit und andere Medien schützen.
Starke Gründe für die FIPFG Dichtungstechnologie
- Vollautomatisch, prozesssicher, flexibel
- Schnell, wirtschaftlich und effizient
- Geringer Personalaufwand durch hohen Automationsgrad
- Kurze Fertigungszyklen und hohe Produktionsgeschwindigkeiten
- Reproduzierbare Qualität nahtloser, konturgenauer Schaumdichtungen
- Fast unsichtbare selbst nivellierende Kopplungsstelle
- Frei dosierbarer Applikationsprozess – keine formenden Werkzeuge notwendig wie bei 2K-Spritzguss
- Kostengünstige Alternative insbesonders für komplexe Bauteilgeometrien
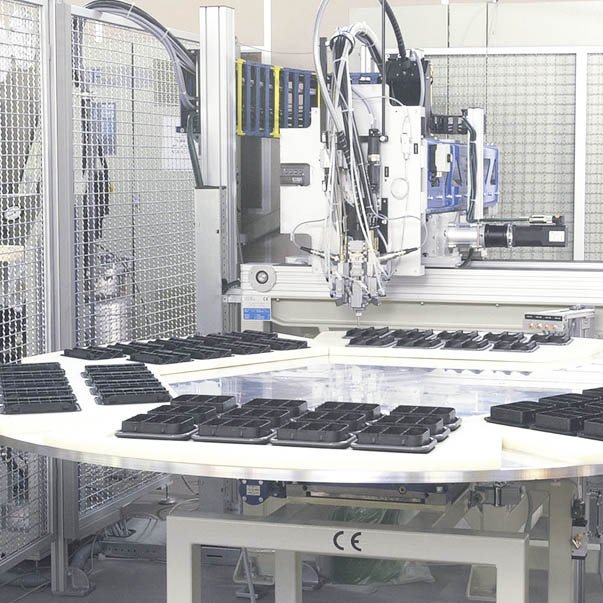
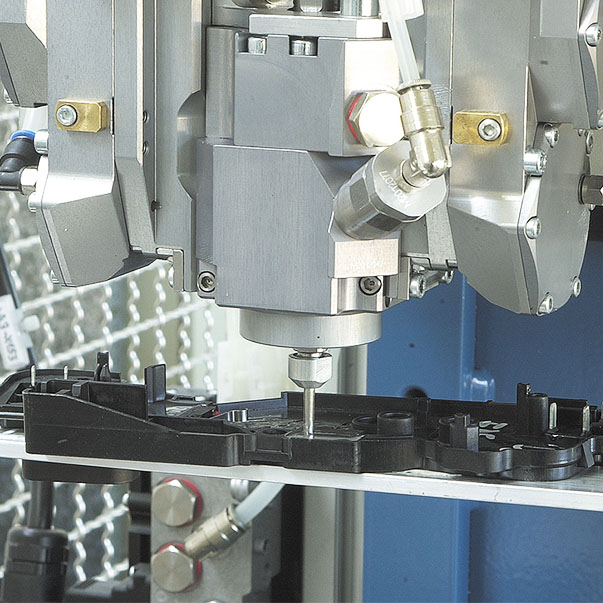
- Größtmögliche Materialausnutzung – keine Stanzabfälle wie bei Einlegedichtung
- Maximal flexibel weil jederzeit neu programmierbar – Änderungen in laufender Produktion bis zu kompletten Modelwechseln spontan möglich
- Auch für kleinste Serien geeignet durch freie Programmierbarkeit der Dosieranlage
- Gemischte „chaotische“ Teilefertigung mit Teileerkennung der Dosieranlage
- Gute Integration in bestehende Produktionen
Einsparmöglichkeiten durch die geschäumte Dichtung
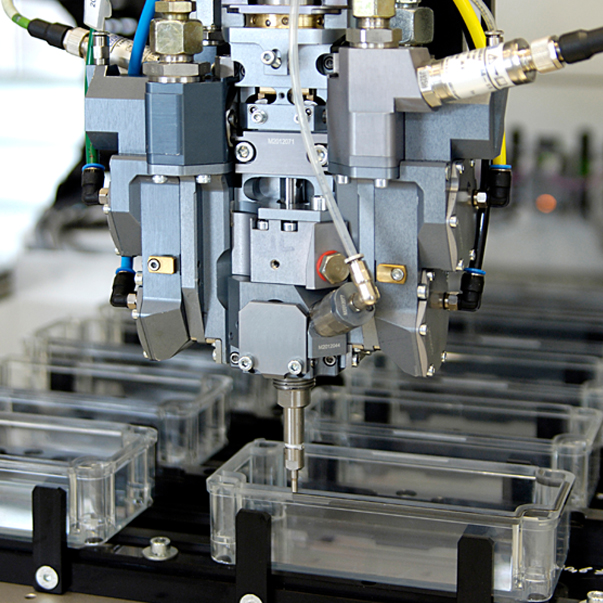
Mit dem FIPFG-Technologie (Formed-In-Place-Foam-Gasket) lässt sich, im Vergleich zum manuellen Einlegen vorgefertigter Dichtungen, viel Geld sparen. Insbesondere dann, wenn es sich um hohe Fertigungszahlen handelt und die Bauteile nur relativ arbeitsintensiv mit einer herkömmlichen Gummidichtung (wie EPDM oder NBR) versehen werden können, ist das direkte Anschäumen einer Dichtung - das automatisierte FIPFG-Verfahren - klar im Vorteil.
Mit der folgenden Beispielrechnung kann der Kosteneffekt prinzipiell nachvollzogen werden. Auch wenn es sich um eine stark vereinfachende Betrachtung handelt, ist sie für eine erste Einschätzung auch auf andere Anwendungen durchaus übertragbar.
Im folgenden Beispiel soll eine Elektronikbox betrachtet werden, Produktionsmenge 2.000.000 Stück pro Jahr, mit einer Dichtungslänge von 30 cm und einem Dichtungsdurchmesser von 4 mm.
Berechnung der Kosten eines herkömmlichen, manuell applizierten Dichtungsverfahrens
Die wesentlichen Kosten sind die Material- und Arbeitskosten.
Die Materialkosten ergeben sich aus der benötigten Dichtungsschnurmenge (2.000.000 Bauteile x 30 cm) und dem Materialpreis (EPDM-Schnur auf Rolle 1.000 m für 300 €). Umgelegt auf die einzelne Dichtung belaufen sich die Materialkosten damit auf ca. 0,09 € pro herkömmlicher Dichtung.
Die Arbeitszeit pro Dichtungsschnur ist oft nicht genau bekannt. Sie wird überschlägig hergeleitet aus der Anzahl und Arbeitszeit der dazu notwendigen Mitarbeiter. In diesem Beispiel montieren je drei Mitarbeiter im 2-Schichtbetrieb, 8 Stunden pro Tag, 250 Arbeitstage pro Jahr, um 2.000.000 Teile herzustellen - und haben trotzdem nur 21 Sekunden Zeit, um eine Dichtung zu montieren. Der Stundenlohn beträgt 20 €. Daraus ergeben sich Arbeitskosten von 240.000 € pro Jahr beziehungsweise 0,12 € pro Teil.
Durch Addition der Material- und Arbeitskosten ergeben sich für die handeingelegte Dichtung Gesamtkosten von 0,21 € pro Dichtung beziehungsweise 420.000 €/Jahr.
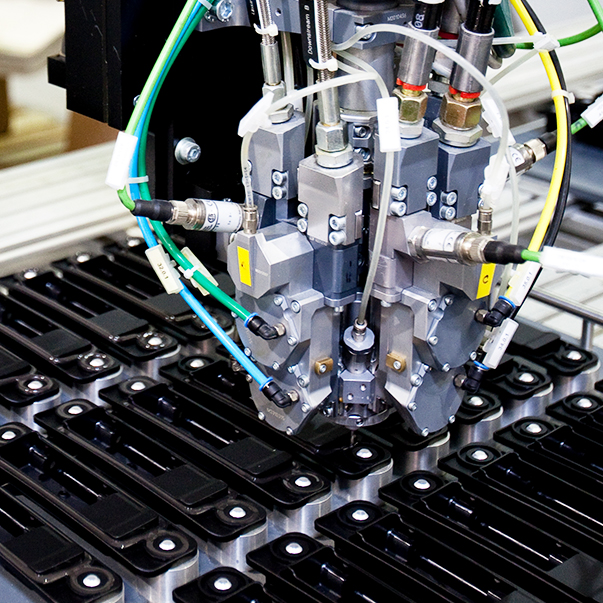
Berechnung der Kosten für die FIPFG-Technologie
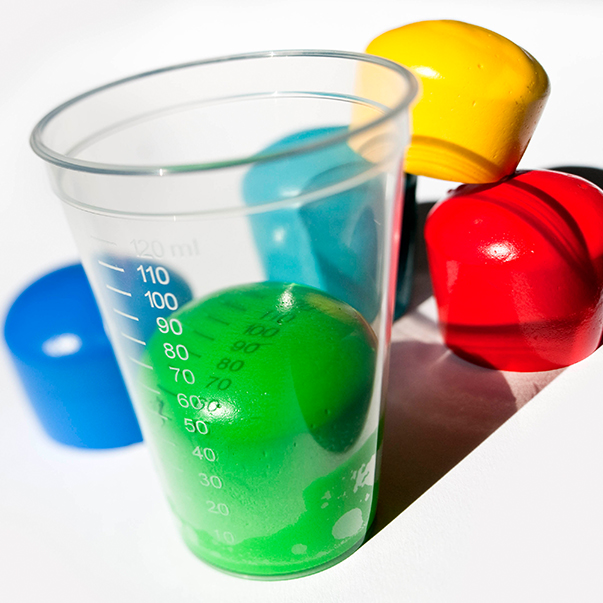
Die Materialkosten ergeben sich aus der notwendigen Dichtungsmasse und den Materialkosten pro kg. Die Dichtungsmasse ergibt sich aus der Multiplikation von Dichte und Volumen. Das Dichtungsvolumen wird durch Multiplikation von Dichtungslänge (30cm) und dem (idealisierten) Durchmesser (4mm) errechnet. Die Dichte wird hier mit typischen 0,4 g/cm3 angenommen. Zur Herstellung einer Dichtung werden also 1,52 g Rohstoff benötigt. Der Materialpreis wird mit 6 €/kg (0,006 €/g) angenommen. Die Materialkosten der geschäumten Dichtung betragen somit ca. 0,01 € pro Dichtung.
Die Kosten der FIPFG-Anlage hängen davon ab in welchem Zeitraum sich die Maschine amortisiert haben soll. In diesem Beispiel gehen wir von einem Investitionsvolumen von 200.000 € und einem Amortisationszeitraum von zwei Jahren aus. Damit ergeben sich Jahresmaschinenkosten von 100.000 €. Umgerechnet auf ein Bauteil liegen die Maschinenkosten pro geschäumter Dichtung bei 0,05 € pro Teil. Bei einer länger gewählten Pay-Off Dauer sind die auf ein Teil umgelegten Kosten entsprechend noch erheblich niedriger.
EPDM | FIPFG | |||
---|---|---|---|---|
Kosten | pro Dichtung | Kosten p.a. (Beispiel) | pro Dichtung | Kosten p.a. (Beispiel) |
Material | 0,09 | 180.000 | 0,01 | 20.000 |
Arbeit | 0,12 | 240.000 | 0,04 | 160.000 |
Maschine | / | / | 0,05 | 100.000 |
Sonstiges | / | / | 0,01 | 20.000 |
Gesamt | 0,21 | 420.000 | 0,11 | 300.000 |
Ersparnis | 0,10 |
120.000 |
Fazit des Kostenvergleichs
Der Vergleich der Kosten der vorgestellten Beispielrechnung zeigt deutlich die Einsparmöglichkeiten, die das FIPFG-Verfahren bietet.
Gleichwohl ist es eine idealisierte Betrachtung. Kosten für elektrische Energie, Druckluft, Wasser, Ersatzteile, Ausschussteile etc. wurden lediglich für die FIPFG-Technologie und dort pauschal mit 10 % angesetzt. In der konkreten Umsetzung muss jeder Fall einzeln betrachtet und verglichen werden.
Erfahrungsgemäß gilt aber, dass sich die Investition in eine Maschine meist schon ab einer Jahresproduktion von ca. 50.000 Teilen lohnt und ein Vergleich der Kosten durchgeführt werden sollte.
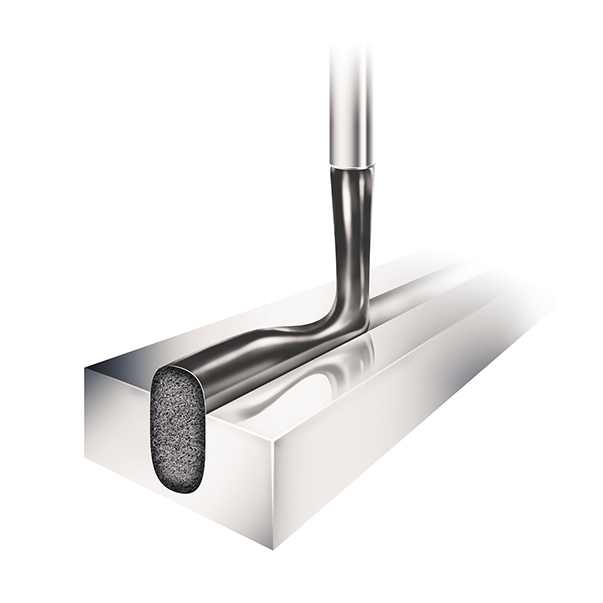